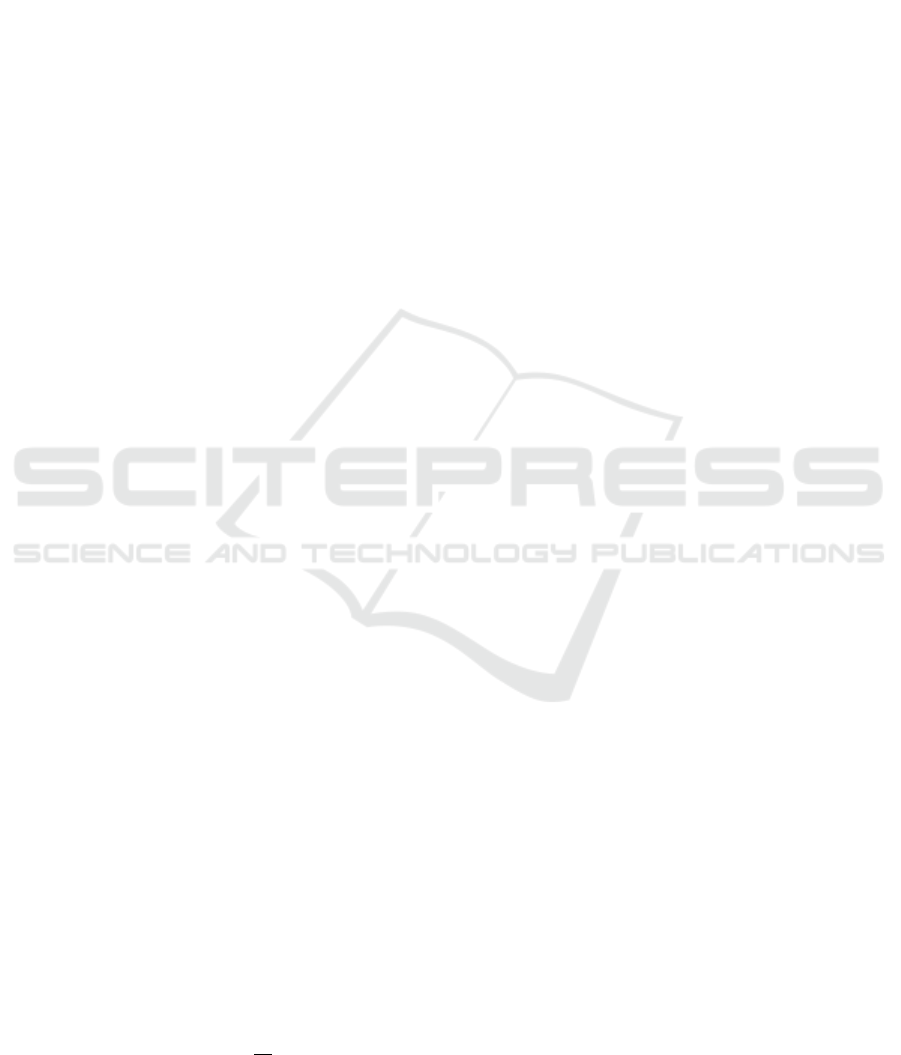
Dynamic Analysis of the Fractional PID Controller
Juliana Tonasso Herdeiro and Renato Aguiar
Dept. of Electrical Engineering, Centro Universit
´
ario FEI,
Av. Humberto de Alencar Castelo Branco, SBC, Sao Paulo, Brazil
Keywords:
PID Controller, Fractional PID Controller, Fractional Calculus, Data Aquisition, Robustness.
Abstract:
This article presents as main objective the study and application of the fractional PID controller in a positioning
system, a controller that has basis on the fractional calculus theory originated in 1695 and, despite having
generated several paradoxes in the decade, nowadays there are important applications of this theory, as the
one reported in this paper. Initially, the controller will be designed by means of computational simulation for
the nominal model of a plant, using a program in Matlab and optimization algorithms and, then, applying in
a real process using a data acquisition technique in order to analyse its dynamic behavior in the presence of
real external disturbances. Given that the fractional PID is a generalization of the traditional PID, the goal is
to obtain, in practice, the benefits of this one in relation to the another, mainly observing the requirements of
robustness and stability that must be present in the system.
1 INTRODUCTION
The great industrial growth in recent years, along with
the technological advance, produced constant chan-
ges in society as a whole. Increasingly the indus-
trial processes become independent of human being
and industrial automation reflects this process, for ex-
ample, in the use of the robotic arm, which allows,
when properly controlled, to perform welding, pain-
ting, displacement of objects, among other applicati-
ons, automatically.
The PID controller (Proportional + Integrative +
Derivative), widely used in industry, is one of the
most traditional controllers in control theory and there
are several methods for obtaining it (Dorf and Bishop,
2009). Result of the combination of three basic con-
trollers, in other words, the combination of propor-
tional, integrative and derivative controllers, its effi-
ciency on making a response of a system display pre-
determined characteristics motivated studies that pro-
vided several methods for tuning this type of control-
ler (Ogata, 1998).
The following transfer function (Dorf and Bishop,
2009) describes that controller which, in this paper,
will be denominated as traditional PID (or classical
PID, as it is also known in academic publications):
PID
trad
(s) = K
p
+
K
i
s
+ K
d
s, (1)
where K
p
, K
i
and K
d
are, respectively, proportional,
integrative and derivative gains of the controller.
Over the years, a new use possibility for the tradi-
tional PID controller has been noticed, which is know
as fractional PID. As it is a generalization of the tradi-
tional PID, it promises to be a model closer to reality,
and provide a more refined control system.
Herewith, it can be thought about implementing
the fractional PID in several industrial applications,
being able to replace the so called traditional PID.
As an example, in (Tepljakov et al., 2011) the aut-
hors comment on the focus given to fractional calcu-
lus in the last years, applied to control systems design
due to more precise modeling and control enhance-
ment possibilities. Already in (Tavazoei, 2012) the
author highlights the use of fractional order dynamics
to obtain more realistic models for real world pheno-
mena and physical processes such as thermal systems
and polarization phenomena. Other practical applica-
tions are also mentioned, such as suppression of chao-
tic oscillations in electrical circuits and compensating
disturbances on the position and velocity servo sys-
tems.
In more recent studies, as in (Sandhya et al.,
2016), examples of the best fractional controller that
can be designed are given, arguing that it overcomes
the best integer order controller even though it is ve-
rified that this latter works comparatively well. One
of these examples considers a fractional controller for
an integer order plant (DC motor with elastic shaft -
a model from Mathworks, 2006), and the optimiza-
Herdeiro, J. and Aguiar, R.
Dynamic Analysis of the Fractional PID Controller.
DOI: 10.5220/0006852904270434
In Proceedings of the 15th International Conference on Informatics in Control, Automation and Robotics (ICINCO 2018) - Volume 1, pages 427-434
ISBN: 978-989-758-321-6
Copyright © 2018 by SCITEPRESS – Science and Technology Publications, Lda. All rights reserved
427