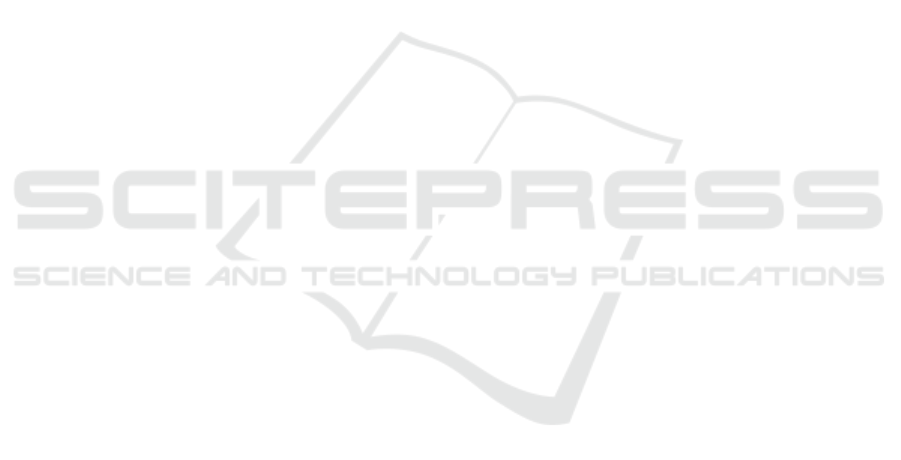
with sound state representations through encapsula-
tion of manifolds. Information Fusion, 14(1):57–77.
Hesslow, G. (2012). The current status of the simulation
theory of cognition. Brain research, 1428:71–9.
Hidalgo Carri
´
o, J., Arnold, S., B
¨
ockmann, A., Born, A.,
Dom
´
ınguez, R., Hennes, D., Hertzberg, C., Ma-
chowinski, J., Schwendner, J., Yoo, Y., and Kirchner,
F. (2016). EnviRe - environment representation for
long-term autonomy.
Howard, T. M. and Kelly, A. (2007). Optimal rough ter-
rain trajectory generation for wheeled mobile robots.
The International Journal of Robotics Research,
26(2):141–166.
K
¨
ummerle, R., Grisetti, G., Strasdat, H., Konolige, K.,
and Burgard, W. (2011). g
2
o: A general framework
for graph optimization. In Robotics and Automa-
tion (ICRA), 2011 IEEE International Conference on,
pages 3607–3613. IEEE.
K
¨
ummerle, R., Hahnel, D., Dolgov, D., Thrun, S., and Bur-
gard, W. (2009). Autonomous driving in a multi-level
parking structure. In 2009 IEEE International Confer-
ence on Robotics and Automation, pages 3395–3400.
Lacroix, S., Mallet, A., Bonnafous, D., Bauzil, G., Fleury,
S., Herrb, M., and Chatila, R. (2002). Autonomous
rover navigation on unknown terrains: Functions and
integration. The International Journal of Robotics Re-
search, 21(10-11):917–942.
Lee, J. et al. (2017). Flexible collision library.
https://github.com/flexible-collision-library/fcl.
Likhachev, M. et al. Search-based planning lab.
http://www.sbpl.net.
Likhachev, M., Gordon, G. J., and T., S. (2004). ARA*:
Anytime A* with provable bounds on sub-optimality.
In Thrun, S., Saul, L. K., and Sch
¨
olkopf, B., editors,
Advances in Neural Information Processing Systems
16, pages 767–774. MIT Press.
Lorensen, W. E. and Cline, H. E. (1987). Marching cubes:
A high resolution 3d surface construction algorithm.
In ACM siggraph computer graphics, volume 21,
pages 163–169. ACM.
Marques, H. G. and Holland, O. (2009). Architectures
for functional imagination. Neurocomputing, 72(4-
6):743–759.
Nesnas, I. A. D., Matthews, J. B., Abad-Manterola, P., Bur-
dick, J. W., Edlund, J. A., Morrison, J. C., Peters,
R. D., Tanner, M. M., Miyake, R. N., Solish, B. S., and
Anderson, R. C. (2012). Axel and duaxel rovers for
the sustainable exploration of extreme terrains. Jour-
nal of Field Robotics, 29(4):663–685.
Newcombe, R. A., Izadi, S., Hilliges, O., Molyneaux, D.,
Kim, D., Davison, A. J., Kohi, P., Shotton, J., Hodges,
S., and Fitzgibbon, A. (2011). KinectFusion: Real-
time dense surface mapping and tracking. In Mixed
and augmented reality (ISMAR), 2011 10th IEEE in-
ternational symposium on, pages 127–136. IEEE.
Preston, L., Barber, S., and Grady, M. (2012). Concepts for
activities in the field of exploration (cafe). tn2: The
cataloge of planetary analogues.
Rekleitis, I., Bedwani, J., Dupuis, E., Lamarche, T., and Al-
lard, P. (2013). Autonomous over-the-horizon naviga-
tion using LIDAR data. Autonomous Robots, 34(1):1–
18.
Rockel, S., Klimentjew, D., Zhang, L., and Zhang, J.
(2014). An hyperreality imagination based reasoning
and evaluation system (HIRES). In 2014 IEEE In-
ternational Conference on Robotics and Automation
(ICRA), pages 5705–5711.
Rockel, S., Kone
ˇ
cn
´
y,
ˇ
S.and Stock, S., Hertzberg, J., Pecora,
F., and Zhang, J. (2015). Integrating physics-based
prediction with semantic plan execution monitoring.
In 2015 IEEE/RSJ International Conference on Intel-
ligent Robots and Systems (IROS), pages 2883–2888.
Roßmann, J., Guiffo Kaigom, E., Atorf, L., Rast, M., Grin-
shpun, G., and Schlette, C. (2014). Mental models
for intelligent systems: eRobotics enables new ap-
proaches to simulation-based AI. KI - K
¨
unstliche In-
telligenz, 28(2):101–110.
Segal, A., Haehnel, D., and Thrun, S. (2009). Generalized-
ICP. In Robotics: Science and Systems, volume 2,
page 435.
Triebel, R., Pfaff, P., and Burgard, W. (2006). Multi-
level surface maps for outdoor terrain mapping and
loop closing. In Intelligent Robots and Systems, 2006
IEEE/RSJ International Conference on, pages 2276–
2282. IEEE.
Wynne, J. J. (2016). The scientific importance of caves in
our solar system: Highlights of the 2nd international
planetary caves conference, Flagstaff, Arizona. NSS
NewS, page 5.
Internal Simulation for Autonomous Robot Exploration of Lava Tubes
155