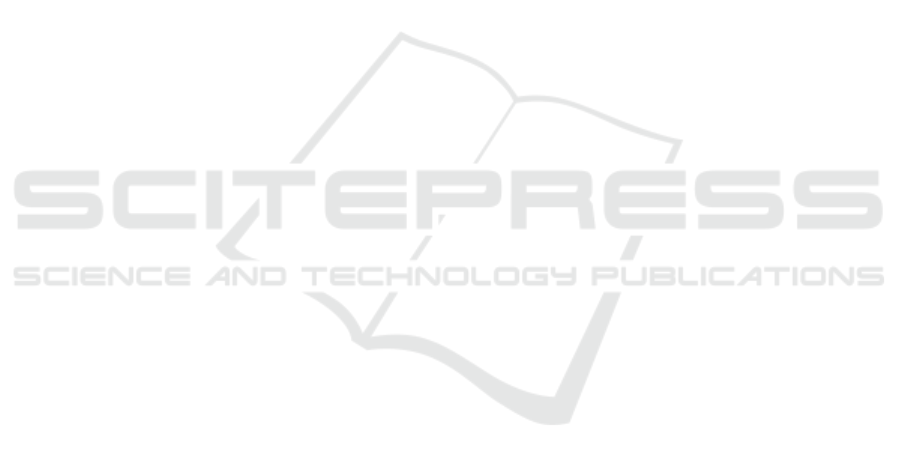
8 CONCLUSIONS AND
OUTLOOK
In this paper we introduced an approach for automatic
planning of manufacturing processes to build prod-
ucts with robots. It bases on modules which aim for
integrating expert knowledge and at the same time
separate different domain expertises such as automa-
tion, process and application into independent com-
ponents. The approach contains a heuristic search
based on cost estimations to find a suitable manu-
facturing program. Here, the modules contribute to
different steps in order to solve the overall problem:
They allow for deriving a structural model from an
engineer’s construction plan of a goal product and are
used to calculate processes to establish the structure.
Furthermore, modules can plan concrete robot actions
to perform the overall manufacturing of the final prod-
uct. We applied the presented concept to the domain
of LEGO and used it to plan the manufacturing of a
LEGO house with a robot. It has been evaluated with
different variations of heuristic properties.
As further work, we plan to improve the perfor-
mance of the heuristic search, for example by re-
ducing the state space through geometric reachability
analysis between manipulator and object. Especially
when planning with multiple manipulators, a strategy
for the selection of alternative manipulators for each
process action might be included into the approach.
As a major future research question, we will inves-
tigate strategies for parallel execution of tasks using
independent manipulators. The goal is to make plan-
ning for multiple robots in a multi-functional robot
cell feasible without the rapidly growing planning
time seen in the multi-robot evaluation results of our
work. In a further step, a second use case in a differ-
ent domain – such as CFRP – will be investigated to
demonstrate that the presented concepts can be gener-
ically applied to other domains and in real world.
ACKNOWLEDGEMENTS
This work is partly funded by the German Research
Foundation (DFG) under the TeamBotS grant.
REFERENCES
Angerer, A., Hoffmann, A., Schierl, A., Vistein, M., and
Reif, W. (2013). Robotics API: Object-oriented soft-
ware development for industrial robots. J. of Software
Engineering for Robotics, 4(1):1–22.
Angerer, A., Vistein, M., Hoffmann, A., Reif, W., Krebs, F.,
and Sch
¨
onheits, M. (2015). Towards multi-functional
robot-based automation systems. In Proc. 12th Intl.
Conf. on Inform. in Control, Autom. & Robot., pages
438–443.
Fikes, R. and Nilsson, N. J. (1971). STRIPS: A new ap-
proach to the application of theorem proving to prob-
lem solving. Artif. Intell., 2(3/4):189–208.
Hart, P. E., Nilsson, N. J., and Raphael, B. (1968). A for-
mal basis for the heuristic determination of minimum
cost paths. IEEE Transactions on Systems Science and
Cybernetics, 4(2):100–107.
Kaelbling, L. P. and Lozano-P
´
erez, T. (2011). Hierarchical
task and motion planning in the now. In Proc. IEEE
Intl. Conf. on Robot. & Autom., pages 1470–1477.
Knepper, R. A., Layton, T., Romanishin, J., and Rus, D.
(2013). Ikeabot: An autonomous multi-robot coordi-
nated furniture assembly system. In Proc. IEEE Intl.
Conf. on Robot. & Autom., pages 855–862.
Levihn, M., Kaelbling, L. P., Lozano-P
´
erez, T., and Stilman,
M. (2013). Foresight and reconsideration in hierarchi-
cal planning and execution. In Proc. IEEE/RSJ Intl.
Conf. on Intell. Robots and Systems, pages 224–231.
Macho, M., N
¨
agele, L., Hoffmann, A., Angerer, A., and
Reif, W. (2016). A flexible architecture for automat-
ically generating robot applications based on expert
knowledge. In Proc. 47
th
Intl. Symp. on Robotics.
VDE Verlag.
McDermott, D., Ghallab, M., Howe, A., Knoblock, C.,
Ram, A., Veloso, M., Weld, D., and Wilkins, D.
(1998). PDDL — the planning domain definition lan-
guage. Technical Report TR 98 003/DCS TR 1165,
Yale Center for Computational Vision and Control.
N
¨
agele, L., Macho, M., Angerer, A., Hoffmann, A., Vis-
tein, M., Sch
¨
onheits, M., and Reif, W. (2015). A
backward-oriented approach for offline programming
of complex manufacturing tasks. In Proc. 6
th
Intl.
Conf. on Autom., Robotics & Applications, pages 124–
130. IEEE.
Pfrommer, J., Stogl, D., Aleksandrov, K., Navarro, S. E.,
Hein, B., and Beyerer, J. (2015). Plug & produce
by modelling skills and service-oriented orchestration
of reconfigurable manufacturing systems. Automa-
tisierungstechnik, 63(10):790–800.
Vistein, M., Angerer, A., Hoffmann, A., Schierl, A., and
Reif, W. (2014). Flexible and continuous execution of
real-time critical robotic tasks. Intl. J. of Mechatronics
and Automation, 4(1):27–38.
Automatic Planning of Manufacturing Processes using Spatial Construction Plan Analysis and Extensible Heuristic Search
583