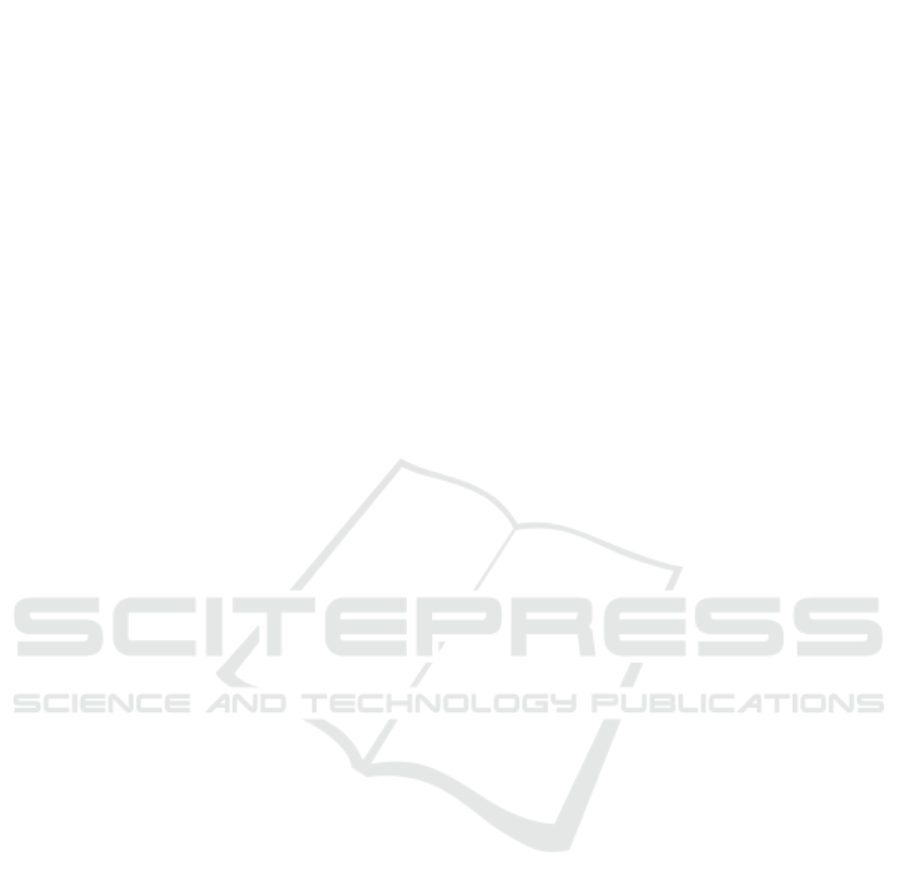
the observing and analyzing the simulation and real-
time results, when a fault occurs the PFTC scheme
using neural network plus PI controller design had
achieved its desired set point and stability.
Meanwhile, the PFTC using PI feedback control
design achieves its desired set point but does not
improve its steady state error as compared to PFTC
scheme. Hence, it can be proved that proposed PFTC
scheme using neural network plus PI controller mode
design is one of the most efficient techniques to
ensure the system performance does not degrade and
set point is achieved in spite of fault and disturbances.
Framework of PFTCS is a realistic choice when
efficient fault diagnosis procedure is not available.
However how to take into account the prior
knowledge of the system faults, is a key work in the
passive fault tolerant control system design. In further
works PFTC scheme can be designed for multiple
faults like system and sensor faults occurring at the
same time. Also other than neural network another
soft computing techniques can be used (e.g. Adaptive
Neuro-Fuzzy Inference System (ANFIS)) for PFTC
scheme.
ACKNOWLEDGMENT
This work was carried out in Instrumentation and
Process Control (IPC) Laboratory at the Department
of Chemical Engineering, Dharmsinh Desai
University, Nadiad-387001, Gujarat, India. The
authors also would like to express very great
appreciation to Dr. M. S. Rao and Mr. Pratik Soni for
his valuable and constructive suggestions during the
planning and development of this research work.
REFERENCES
Amoozgar, M.H., Chamseddine, A. & Zhang, Y., 2012.
“Fault-tolerant fuzzy gain scheduled PID for a
quadrotor helicopter test bed in the presence of actuator
faults,” In Advances in PID Control Brescia (Italy),
March 28-30. IFAC Proceedings Volumes, pp. 282–
287.
Basin, M. et al., 2015. “A finite-time-convergent fault-
tolerant control and its experimental verification for
DTS200 three-tank system,” In International Workshop
on Recent Advances in Sliding Modes (RASM 2015) 9-
11 April Istanbul (Turkey). IEEE, pp. 1–6.
Capiluppi, M. & Paoli, A., 2005. “Distributed fault tolerant
control of the two-tank system benchmark,” In 44
th
IEEE Conference on Decision and Control 15-15
December Seville (Spain). IEEE, pp. 1361–1366.
Casavola, A. et al., 2010. “A fault-tolerant real-time
supervisory scheme for an interconnected four-tank
System,” In American Control Conference (ACC 2010)
Baltimore June-30-July-2. IEEE, pp. 6210–6215.
Gao, Z., Cecati, C. & Ding, S.X., 2015. A Survey of Fault
Diagnosis and Fault-Tolerant Techniques—Part I: Fault
Diagnosis With Model-Based and Signal-Based
Approaches. IEEE Transactions on Industrial
Electronics, 62(6), pp.3757–3767.
He, X. et al., 2016. Active fault-tolerant control for an
internet-based networked three-tank system. IEEE
Transactions on Control Systems Technology, 24(6),
pp.2150–2157.
He, X. et al., 2017. Fault-Tolerant Control for an Internet-
Based Three-Tank System: Accommodation to Sensor
Bias Faults. IEEE Transactions on Industrial
Electronics, 64(3), pp.2266–2275.
Isermann, R. & Ballé, P., 1997. Trends in the application of
model based fault detection and diagnosis of technical
processes. Control Engineering Practice, 5(5), pp.709–
719.
Li, Z. et al., 2015. “Design of Passive Fault Tolerant
Control of A Process System,” In the 27th Chinese
Control and Decision Conference (2015 CCDC) 23-25
May Qingdao (China). IEEE, pp. 2776–2781.
Mendonca, L.F., Sousa, J.M.C. & Sa da Costa, J.M.G.,
2008. “Fault accommodation of an experimental three
tank system using fuzzy predictive control,” In IEEE
International Conference on Fuzzy Systems (IEEE
World Congress on Computational Intelligence) 1-6
June Hong Kong (China). IEEE, pp. 1619–1625.
Merheb, A.-R., Noura, H. & Bateman, F., 2013. “Passive
fault tolerant control of quadrotor UAV using regular
and cascaded Sliding Mode Control,” In Conference on
Control and Fault-Tolerant Systems (SysTol) 9-11
October. IEEE, pp. 330–335.
Noura, H., Theilliol, D. & Sauter, D., 2000. Actuator fault-
tolerant control design: demonstration on a three-tank-
system. Journal of International Journal of Systems
Science, 31(9), pp.1143–1155.
Orani, N., Pisano, A. & Usai, E., 2009. “Fault Detection and
Reconstruction for a Three-Tank System via high-order
sliding-mode observer,” In IEEE Control Applications,
(CCA) & Intelligent Control, (ISIC) 8-10 July St.
Petersburg (Russia). IEEE, pp. 1714–1719.
Parikh, N. et al., 2017. “A comparison between NMPC and
LQG for the level control of three tank interacting
system,” In Indian Control Conference (ICC 2017) 4-6
January Guwahati (India). IEEE, pp. 200–205.
Patel, H.R. & Shah, V.A., 2018a. Fault Tolerant Control
Systems: A Passive Approaches for Single Tank Level
Control System. Journal of Instrumentation and Control
Engineering, 6(1), pp.11–18.
Patel, H.R. & Shah, V.A., 2018b. “Fuzzy Logic Based
Passive Fault Tolerant Control Strategy for a Single-
Tank System with System Fault and Process
Disturbances,” In Proc. 5
th
International Conference on
Electrical and Electronics Engineering (ICEEE),
Istanbul (Turkey), 3-5 May 2018, pp. 257–262.
A Framework for Fault-tolerant Control for an Interacting and Non-interacting Level Control System using AI
189