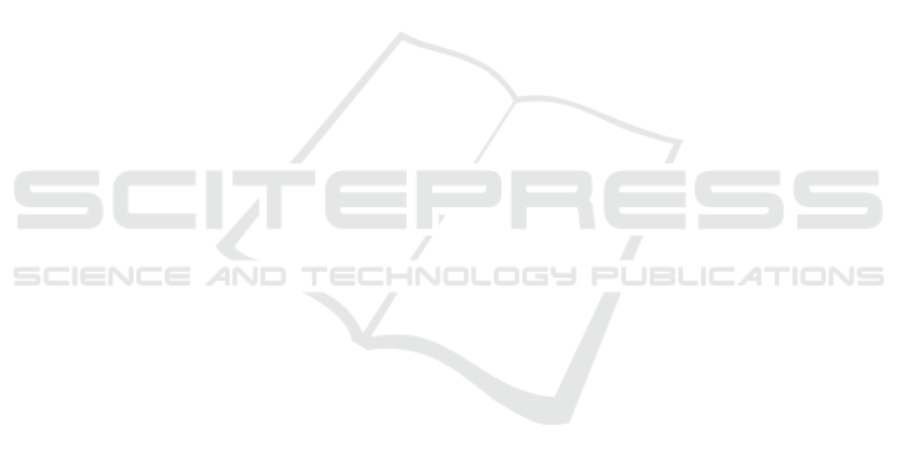
localization of the target even with a mis-calibration
between the manipulator and the sensor frames. The
results validated the proposed methodology for a low-
cost ground-truth system to be used in mobile robotic
applications.
Finally, as future work is intended to develop
a standardized bench to optimize the alignment of
the sensor and apply the ground truth in a low cost
localization application and the development of a
ROS node enhancing the cooperation among other re-
searchers community.
ACKNOWLEDGEMENTS
This work is financed by the ERDF European
Regional Development Fund through the Opera-
tional Programme for Competitiveness and Interna-
tionalisation - COMPETE 2020 Programme within
project POCI-01-0145-FEDER-006961, and by Na-
tional Funds through the Portuguese funding agency,
FCT -Fundac¸
˜
ao para a Ci
ˆ
encia e a Tecnologia
(Portuguese Foundation for Science and Technol-
ogy), within project SAICTPAC/0034/2015- POCI-
01- 0145-FEDER-016418 and as part of project
UID/EEA/50014/2013.
REFERENCES
ABB, R. (2003). Product manual irb 140. ABB Robotics
Products AB publication, (M2000):7564–1.
Hess, W., Kohler, D., Rapp, H., and Andor, D. (2016). Real-
time loop closure in 2d lidar slam. In Robotics and
Automation (ICRA), 2016 IEEE International Confer-
ence on, pages 1271–1278. IEEE.
Hokuyou (2018). Urg-04lx. Online; accessed 29/01/2018.
Kawata, H. (2006). Urg series communication protocol
specification scip-version2. 0. Drawing No. C-42-
03320B, Oct.
Lima, J. and Costa, P. (2017). Ultra-wideband time of
flight based localization system and odometry fu-
sion for a scanning 3 dof magnetic field autonomous
robot. In Iberian Robotics conference, pages 879–890.
Springer.
Lima, J., Gonc¸alves, J., Costa, P. J., and Moreira, A. P.
(2013). Modeling and simulation of a laser scanner
sensor: an industrial application case study. pages
245–258.
Nepali, M. R., Yadav, N., Dev, U., Mishra, S., and Shrestha,
S. L. (2015). A strategic methodology for 2d map
building in an indoor environment. In Next Genera-
tion Computing Technologies (NGCT), 2015 1st Inter-
national Conference on, pages 797–803. IEEE.
Okubo, Y., Ye, C., and Borenstein, J. (2009). Characteriza-
tion of the hokuyo urg-04lx laser rangefinder for mo-
bile robot obstacle negotiation. In Unmanned Systems
Technology XI, volume 7332, page 733212. Interna-
tional Society for Optics and Photonics.
Olson, E. (2015). M3rsm: Many-to-many multi-resolution
scan matching. In Robotics and Automation (ICRA),
2015 IEEE International Conference on, pages 5815–
5821. IEEE.
Rida, M. E., Liu, F., Jadi, Y., Algawhari, A. A. A., and
Askourih, A. (2015). Indoor location position based
on bluetooth signal strength. In Information Science
and Control Engineering (ICISCE), 2015 2nd Inter-
national Conference on, pages 769–773. IEEE.
Santos, J. M., Portugal, D., and Rocha, R. P. (2013). An
evaluation of 2d slam techniques available in robot
operating system. In Safety, Security, and Rescue
Robotics (SSRR), 2013 IEEE International Sympo-
sium on, pages 1–6. IEEE.
Siciliano, B. and Khatib, O. (2008). Springer handbook of
robotics. Springer Science & Business Media.
Sobreira, H., Moreira, A. P., Costa, P. G., and Lima, J.
(2015). Robust mobile robot localization based on
security laser scanner. In Autonomous Robot Sys-
tems and Competitions (ICARSC), 2015 IEEE Inter-
national Conference on, pages 162–167. IEEE.
Teixid
´
o, M., Pallej
`
a, T., Font, D., Tresanchez, M., Moreno,
J., and Palac
´
ın, J. (2012). Two-dimensional radial
laser scanning for circular marker detection and ex-
ternal mobile robot tracking. Sensors, 12(12):16482–
16497.
Xu, Z., Zhuang, Y., and Chen, H. (2006). Obstacle detec-
tion and road following using laser scanner. In Intel-
ligent Control and Automation, 2006. WCICA 2006.
The Sixth World Congress on, volume 2, pages 8630–
8634. IEEE.
Zeng, S. and Weng, J. (2007). Online-learning and
attention-based approach to obstacle avoidance using
a range finder. Journal of Intelligent and Robotic Sys-
tems, 50(3):219–239.
Zhong, Y., Wu, F., Zhang, J., and Dong, B. (2016). Wifi
indoor localization based on k-means. In Audio, Lan-
guage and Image Processing (ICALIP), 2016 Interna-
tional Conference on, pages 663–667. IEEE.
ICINCO 2018 - 15th International Conference on Informatics in Control, Automation and Robotics
348