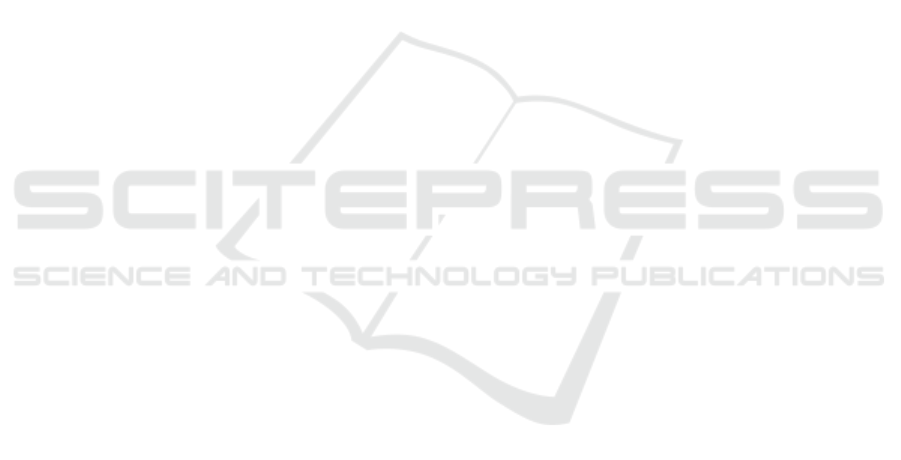
blems to be solved for the new industry infrastructure.
Several standards have emerged to ensure that equip-
ment from different sources can collect and transmit
data in a safe and efficient way.
Another point that has a great prominence in this
scenario is the decentralization of control and incre-
ment of complexity for the accomplishment of all the
operations. Thus the need to develop the autonomous
behavior of the system through approaches such as
multi-agent systems.
In this context, the present article proposes a clas-
sification of Single Board Computers (SBC) for in-
dustrial applications based on an intelligent agent ba-
sed CPS architecture. Once the CPS architecture,
based on 5C (Lee et al., 2015), was developed, it
was necessary to define constraints for supported har-
dware to deploy it. The CPS architecture aims to meet
most of the principles of Industry 4.0 using establis-
hed technologies. The SBC classification indicates
which levels of the CPS architecture on each device
type are able to run on it.
2 OVERVIEW OF CONCEPTS
AND TECHNOLOGIES FOR
INDUSTRY 4.0
This section presents some concepts of techniques as
well as technologies that are gaining prominence with
the development of the next industrial revolution.
2.1 Industry 4.0 Principles
Industry 4.0 is based on six basic principles (Hermann
et al., 2016):
• Real-time operation capability: consists of in-
stant acquisition and processing of data, allowing
decision-making within the constraints time of the
environment;
• Virtualization: proposes the existence of a virtual
copy of the intelligent factories, allowing the re-
mote traceability and monitoring of all the proces-
ses through the numerous sensors spread throug-
hout the plant;
• Decentralization: decision-making can be done
by the cyberphysical system according to the
needs of real-time production. In addition, ma-
chines will not only receive commands, but will
be able to provide information about their work
cycle;
• Service Orientation: Use of service-oriented soft-
ware architectures coupled with the Internet of
Services concept.
• Modularity: Production according to the demand,
coupling and uncoupling of modules in the pro-
duction, offering flexibility to change the tasks of
the machines easily.
• Interoperability: The ability of machines, devices,
sensors and humans to connect and communicate
through the Internet of Things and the Internet.
2.2 Cyber Physical Systems
According to (Lee et al., 2015) the CPS is a system
composed of the union of physical subsystems in net-
work with the computation. The CPS is responsible
for connecting the virtual world with physical rea-
lity, which integrates computing, communication and
storage capacities, and can operate in real time in a
reliable, secure, stable and efficient way.
According to (Barbosa et al., 2016) CPS is an es-
sential aspect for the consummation of the 4th Indus-
trial Revolution, ie, is the key point for the current
industry transformation in Industry 4.0. Cyber Phy-
sical Systems aim to monitor and control industrial
processes through a network of intelligent devices and
sensors, using virtual models of processes that corre-
spond to real processes models, through the combi-
nation of computational, communication and control
elements (Kim and Kumar, 2012). With this it is pos-
sible to decentralize the decision making, that is, an
intelligent device has the power to self-contro
The constitution of CPS may involve the use of
various technologies, such as Multi Agent Systems
(MAS), Service-Oriented Architecture (SoA), Cloud
Computing, Big Data, Machine-to-Machine (M2M)
and Visual Computing.
The integration between different technologies
aims to contribute to the CPS facing challenges iden-
tified in the principles of Industry 4.0. Multi Agent
Systems, for example, can contribute on flexibility,
robustness, adaptation, configuration and distributed
control of these systems.
In the context of Industry 4.0, intelligent agents
and Multi Agent Systems share common ground with
CPS. They can enable CPS with a myriad of capa-
bilities to achieve complexity management, decentra-
lization, intelligence, modularity, flexibility, robust-
ness, and real-time responsiveness capabilities (Lei-
tao et al., 2016).
2.3 5C Architecture for CPS
Among the CPS architectures, the architecture deno-
minated 5C proposed by (Lee et al., 2015) has great
prominence in the literature. It serves as a guide for
Embedded Agent based on Cyber Physical Systems: Architecture, Hardware Definition and Application in Industry 4.0 Context
585