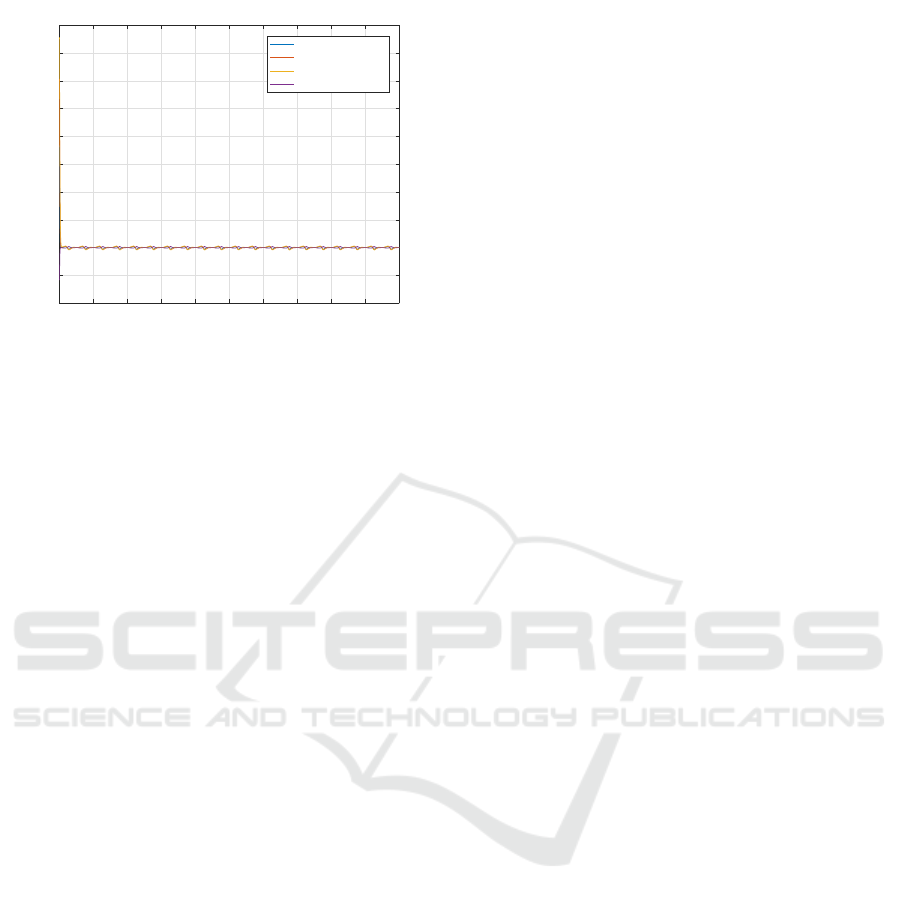
0 2 4 6 8 10 12 14 16 18 20
time(s)
-0.4
-0.2
0
0.2
0.4
0.6
0.8
1
1.2
1.4
1.6
Angle actuator error (rad)
angle actuator error 1
angle actuator error 2
angle actuator error 3
angle actuator error 4
Figure 7: Joint errors.
The robot model is developed taking into account the
cable and the mobile platform flexibilities to describe
the kinematics and the dynamics of the coupled sys-
tem. The proposed control strategy rests on actuator
joint coordinates feedback compared to desired tra-
jectory given in mobile platform joint space and trans-
formed to the actuator joint space. The obtained error
is used to design the sliding control law. As prin-
cipal issue of cable robot is to ensure the cable ten-
sionnability during motion. In this order, constrained
optimization algorithm is developed based on mobile
platform dynamics. The cable tensions are computed,
and thereby used as another input of controller. The
stability of the proposed controller is discussed based
on Lyapunov function.
To validate the feasibility and the effectiveness of
the Multi-Body Cable Driven Robot control, a ref-
erence trajectory is generated to move all the mo-
bile platform degrees of freedoms, and thereby, ap-
plied to the proposed conltrol strategy. Using suitable
gains controller, the simulation results have presented
a good motion tracking.
The present study can be improved by introduc-
ing into the controller, a cable tension feedbacks via
the use of the appropriate sensors or by solving the
Forward Kinematic of the Multi-Body Cable Driven
Robot. if the main is to incorporate the dynamic of
system
ACKNOWLEDGMENT
This work has been supported by Automatic and In-
dustrial Informatics Laboratory (LAII), Ecole Mo-
hammadia dŠIngenieurs, Mohammed V University,
Rabat, Morocco; Integration of Systems and Ad-
vanced Technologies Laboratory (LISTA), Sciences
Faculty, Fes, Morocco; The Department of Electrical
Engineering, Ecole de Technologie Superieure, Mon-
treal, Canada.
REFERENCES
A.Badi, M.Saad, G. and Archambault, P. (2018). A ca-
ble driven robot for locomotor rehabilitation of lower
limb. PCT/CA2016/051376, WO 2017/088055 A1.
A.Chemori, G. El-Ghazaly, M. G. V. C. (2014). Adap-
tive terminal sliding mode control of a redundantly-
actuated cable-driven parallel manipulator: Cogiro.
Springer, Proceedings of the Second International
Conference on Cable- Driven Parallel Robots.
C.Gosselin and M.Grenier (2011). On the determination of
the force distribution in overconstrained cable-driven
parallel mechanisms. Meccanica, 46.
H.Faqihi, M.Saad, K.-M. and M.N.Kabbaj (2016). Track-
ing trajectory of a cable-driven robot for lower limb
rehabilitation.
H.Faqihi, M.Saad, K.-M. M. (2017). Optimization algo-
rithm for an exoskeleton robotic inverse kinematic ap-
plication. Lecture Notes in Electrical Engineering.
M.A.Khosravi and H.D.Taghirad (2014). Robust pid con-
trol of fully-constrained cable driven parallel robots.
Mechatronics, 24.
R.Babaghasabha, M. and H.D.Taghirad (2015). Adaptive
robust control of fully-constrained cable driven paral-
lel robots. In Mechatronics, volume 25.
S. Rezazadeh, S. B. (2011). Workspace analysis of multi-
body cable-driven mechanisms. Journal of Mecha-
nisms and Robotics ASME.
S.K.Agrawal and Y.Mao (2012). Design of a cable-
driven arm exoskeleton (carex) for neural rehabilita-
tion. IEEE Transactions on Robotics, 28.
S.Rezazadeh and S.Behzadipour (2008). Impedance con-
trol of cable driven mechanisms. In Proceedings of
International Design Engineering Technical Confer-
ences and Computers and Information in Engineering
Conference IDETC/CIE.
T.Madani, B.Daachi, K. (2016). Non-singular terminal slid-
ing mode controller: Application to an actuated ex-
oskeleton. Mechatronics, 33.
T.Madani, B.Daachi, K. (2017). Modular-controller-design-
based fast terminal sliding mode for articulated ex-
oskeleton systems. IEEE Transactions on Control Sys-
tems Technology, 25.
V.U.J.Guldner, J. (1999). Sliding mode control in elec-
tromechanical systems. Taylor-Francis.
W.Lv, L. and Z.Ji (2017). Sliding mode control of cable-
driven redundancy parallel robot with 6 dof based on
cable-length sensor feedback. Mathematical Prob-
lems in Engineering, 17.
W.M.Spong, S. and M.Vidyasagar (2006). Robot modeling
and control. ohn Wiley & Sons.
Y.Kali, M.Saad, K. M. (2015). Sliding mode with time delay
control for mimo nonlinear systems with unknown dy-
namics. Recent Advances in Sliding Modes (RASM).
Sliding Mode Control in Mobile Platform Joint Space for Multi-body Cable Driven Robot
363