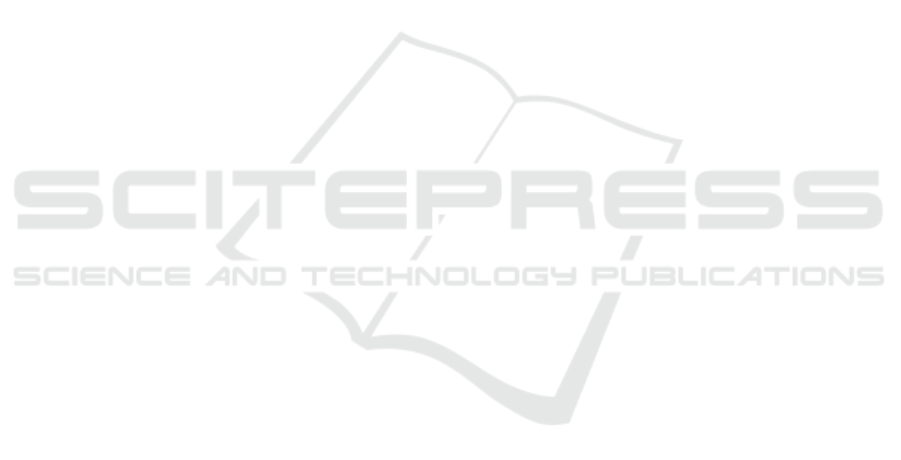
time to reach the desired speed (around 2 seconds),
now are suitable to control our vehicle.
6 CONCLUSIONS AND FUTURE
WORK
This paper presented a low cost speed control method
using extremely low resolution sensors under low-
speed conditions. Using a particularization of the
Kalman Filter (SDKF), we were able to increase the
sensor hall sampling time thus reducing considerably
the quantification noise while keeping the required
control rate. The proposed solution has been tested in
an Unmanned Ground Vehicle and compared against
a Differential GNSS system, showing that is suitable
to perform an effective speed control. We provide
the developed software and CAD designs through a
GitHub repository.
As future work, we plan to study the possibil-
ity of extending the proposed control method to ac-
celeration and jerk adding a PLL structure to obtain
smoother transients. Moreover, we want to evaluate
the speed control performance using a high-level sen-
sor fusion system to make asynchronous updates of
the Kalman filter.
ACKNOWLEDGEMENTS
This work has been supported by the Spanish Gov-
erment through grant FPU15/04446 and the research
project DPI2015-68087-R.
REFERENCES
Andrade-Cetto, J. (2002). The kalman filter. Institut de
Rob
´
otica i Inform
´
atica Industrial, UPC-CSIC.
AUROVA (2018). Software and cad repository:
https://github.com/aurova-lab/clear.
Borenstein, J., Everett, H. R., Feng, L., and Wehe, D.
(1997). Mobile robot positioning-sensors and tech-
niques. Technical report, Naval Command Control
and Ocean Surveillance Center RDT and E Div. San
Diego CA.
Briz, F., Cancelas, J., and Diez, A. (1994). Speed mea-
surement using rotary encoders for high performance
ac drives. In Industrial Electronics, Control and In-
strumentation, 1994. IECON’94., 20th International
Conference on, volume 1, pages 538–542. IEEE.
Carnegie, D., Loughnane, D., and Hurd, S. (2004). The
design of a mobile autonomous robot for indoor se-
curity applications. Proceedings of the Institution of
Mechanical Engineers, Part B: Journal of Engineer-
ing Manufacture, 218(5):533–543.
De Luca, A., Oriolo, G., and Samson, C. (1998). Feed-
back control of a nonholonomic car-like robot. In
Robot motion planning and control, pages 171–253.
Springer.
H
¨
agglund, T. (2012). Signal filtering in pid control. IFAC
Proceedings Volumes, 45(3):1–10.
Indiveri, G., Nuchter, A., and Lingemann, K. (2007). High
speed differential drive mobile robot path following
control with bounded wheel speed commands. In
Robotics and Automation, 2007 IEEE International
Conference on, pages 2202–2207. IEEE.
Jin, Q. B. and Liu, Q. (2014). Imc-pid design based on
model matching approach and closed-loop shaping.
ISA transactions, 53(2):462–473.
Kim, H.-W. and Sul, S.-K. (1996). A new motor speed esti-
mator using kalman filter in low-speed range. IEEE
Transactions on Industrial Electronics, 43(4):498–
504.
Park, M., Lee, S., and Han, W. (2015). Development of
steering control system for autonomous vehicle using
geometry-based path tracking algorithm. ETRI Jour-
nal, 37(3):617–625.
Petrella, R., Tursini, M., Peretti, L., and Zigliotto, M.
(2007). Speed measurement algorithms for low-
resolution incremental encoder equipped drives: a
comparative analysis. In Electrical Machines and
Power Electronics, 2007. ACEMP’07. International
Aegean Conference on, pages 780–787. IEEE.
Ramsden, E. (2011). Hall-effect sensors: theory and appli-
cation. Elsevier.
Santamaria-Navarro, A., Loianno, G., Sol
`
a, J., Kumar, V.,
and Andrade-Cetto, J. (2017). Autonomous naviga-
tion of micro aerial vehicles using high-rate and low-
cost sensors. Autonomous Robots, pages 1–18.
Shaowei, W. and Shanming, W. (2012). Velocity and accel-
eration computations by single-dimensional kalman
filter with adaptive noise variance. Przegld Elek-
trotechniczny, (2), pages 283–287.
Siegwart, R., Nourbakhsh, I. R., and Scaramuzza, D.
(2011). Introduction to autonomous mobile robots.
MIT press.
Thrun, S., Montemerlo, M., Dahlkamp, H., Stavens, D.,
Aron, A., Diebel, J., Fong, P., Gale, J., Halpenny,
M., Hoffmann, G., et al. (2006). Stanley: The robot
that won the darpa grand challenge. Journal of field
Robotics, 23(9):661–692.
Troncoso, C. and Su
´
arez, A. (2017). Control del nivel
de pulpa en un circuito de flotaci
´
on utilizando una
estrategia de control predictivo. Revista Iberoamer-
icana de Autom
´
atica e Inform
´
atica Industrial RIAI,
14(3):234–245.
Speed Estimation for Control of an Unmanned Ground Vehicle using Extremely Low Resolution Sensors
213