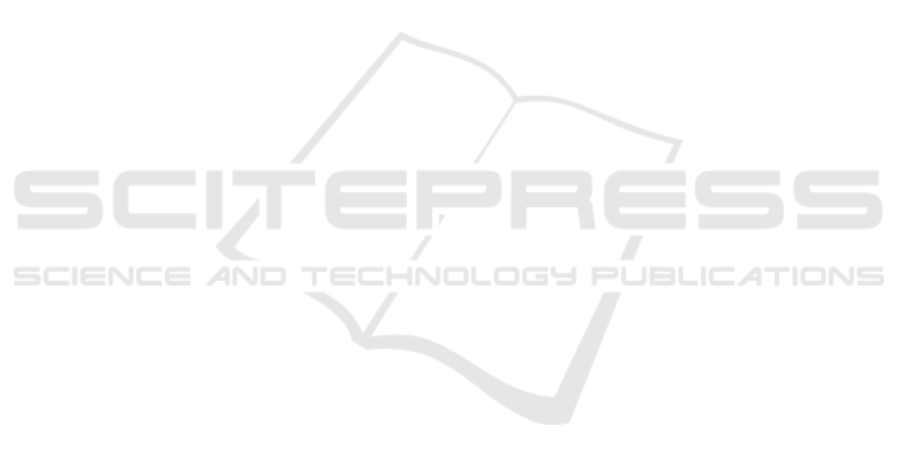
2 LITERATURE REVIEW
The Six Sigma philosophy maintains that reducing
‘variation’ will help solve process and business
problems (Pojasek, 2003). This quality management
methodology is extensively used to improve
processes, products and/or services by discovering
and eliminating defects. The goal is to streamline
quality control in manufacturing or business
processes so there is little to no variance throughout.
The strategic use of Six Sigma principles and
practices ensures that process improvements
generated in one area can be leveraged elsewhere to a
maximum advantage, resulting in quantum increasing
product quality, continuous process improvement
resulting in corporate earnings performance (Sharma
2003).
There is still a limited number of reported flexible
manufacturing system optimization using Six Sigma
or a combination of both Lean principles and Six
Sigma. Moreover, there is virtually no documentation
on the merge of Six Sigma and Taguchi Quality Loss
Function in attempt to optimize a process and or
system. Sharma (2003) also mentions that there are
many advantages of using strategic Six Sigma
principles in tandem with lean enterprise techniques,
which can lead to quick process improvement and/or
optimization. More than 95% of plants closest to
world-class indicated that they have an established
improvement methodology in place, mainly
translated into Lean, Six Sigma or the combination of
both. Valles et. al 2009 use a Six Sigma methodology
(variation reduction) to achieve a 50% reduction in
the electrical failures in a semi-conductor company
dedicated to the manufacturing of cartridges for ink
jet printers. Han et al. 2008 also use Six Sigma
technique to optimize the performance and improve
quality in construction operations. Hansda et. al
(2014) use a Taguchi QLF in a multi-characteristics
optimization scheme to optimize the response in
drilling of GFR composites. Tsui (1996) proposes a
two-step procedure to identify optimal factor settings
that minimize the variance and adjust to target using
a robust design inspired from Taguchi methodology.
Zhanga et. al (2013) use a QLF to adjust a process in
an experimental silicon ingot growing process.
3 THE ROBUST
DESIGN - (DEFINE)
Being part of what is known today as the Taguchi
Methods, Robust Design includes both design of
experiments concepts, and a particular philosophy for
design in a more general sense (e.g. manufacturing
design). Taguchi sought to improve the quality of
manufactured goods, and advocated the notion that
“quality” should correspond to low variance, which is
also the backbone of the Six Sigma methodology
today as it seeks a reduction of variance as a means to
stabilize a process and, hence, improve “quality”. The
present study uses a robust design configuration
inspired by Taguchi robust design methodology.
However, because of the high amount of criticism
against Taguchi’s experimental design tools such as
orthogonal arrays, linear graphs, and signal-to-noise
ratios, the robust design formulation adopted here
avoids the use of Taguchi’s statistical methods and
rather uses an empirical technique developed by
Tshibangu (2003). Overall, implementing a robust
design methodology or formulation requires the
following steps:
• Define the performance measures of interest, the
controllable factors, and the uncontrollable factors or
source of noise.
• Plan the experiment by specifying how the
control parameter settings will be varied and how the
effect of noise will be measured.
• Carry out the experiment and use the results to
predict improved control parameter settings (e.g., by
using the optimization procedure developed in this
study).
• Run a confirmation experiment to check the
validity of the prediction.
In a robust design experiment, the settings of
control parameters are varied simultaneously in few
experimental runs, and for each run, multiple
measurements of the main performance criteria are
carried out in order to evaluate the system sensitivity
to noise.
This study investigates the FMS performance
with respect to the mean flow time (MFT) and
throughput rate (TR) separately by considering 5
variables Xi as controllable parameters, namely: i) the
number of AGVs (X
1
), ii) the speed of AGV (X
2
), iii)
the queue discipline (X
3
), iv) the AGV dispatching
rule (X
4
), v) and the buffer size (X
5
). These
parameters are not the only variables susceptible to
affect the performance of the FMS under study.
However, because one objective of the research is to
design a robust FMS, the parameters considered here
are those related to the performances of the most
costly and vulnerable components of the system, also
potential sources of disturbances, namely: machines
and material handling (AGVs). The controllable
Taguchi Loss Function to Minimize Variance and Optimize a Flexible Manufacturing System (FMS): A Six Sigma Approach Framework
593