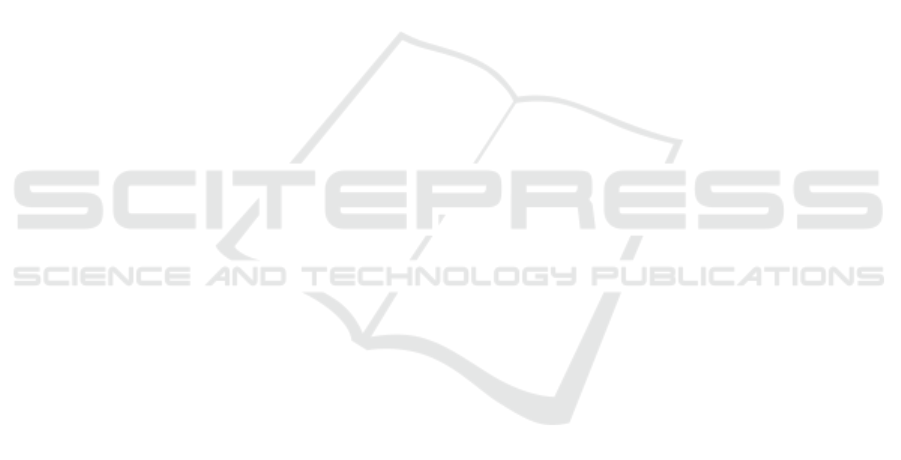
by the choice of frames where joint twists are related:
global (Okamura and Park, 1996) or local (Chen et al.,
2001).
Non-kinematic errors are often attributed to elastic
deformations, transmission nonlinearities, and ther-
mal expansion. To account for these errors corre-
sponding effects are analytically expressed with gear
or elastic models as in (Klimchik et al., 2015) or
(Marie et al., 2013). However, this approach depends
on having an accurate representation of the different
processes that can potentialy influence the accuracy of
the manipulator and inclution of additional parametrs
to be identified (e.g. moments of inertia of the robot
links, friction parameters). As a result these physical
processes are often simplified, leading to inaccuracies
in the model.
Instead, learning approaches are proposed to
model the behaviour of a robot. This allows us to
solve the calibration problem as a function estima-
tion task based on the measured data. The learning
approach requires no a-priori knowledge of the phys-
ical model. Instead, the model can be obtained di-
rectly using measured data. By not attributing errors
to specific physical processes we can distribute kine-
maticic and non-kinematic influences over introduced
error parameters. In general errors of the robot’s EE
may originate from five factors (Liou et al., 1993):
environmental (e.g. temperature or the warm-up pro-
cess), parametric (e.g. Kinematic parameter varia-
tion due to manufacturing and assembly errors, influ-
ence of dynamic parameters, friction and other non-
linearities), measurement (resolution and nonlinearity
of joint position sensors), computational (computer
round-off and steady-state control errors) and appli-
cation (e.g. installation errors). To be able to reflect
different influences in the model, experiments that in-
clude variations of the relevant factors would have to
be conducted. This work considers the influence of
only a limited amount of described factors, mainly
concentrating on the internal parameters of the robot.
However due to the nature of the proposed method,
in case the proper experimental data is available the
model could be easily extended to include other pa-
rameters.
In this paper, a learning based method for robot
calibration using Adjoint error model is presented
along with a comparison of different modeling ap-
proaches. The output of the calibration procedure is
a trained model that based on the input variables (e.g.
robot joint values and nominal Cartesian position of
the EE) would calculate the resulting pose of the ma-
nipulator under the influence of kinematic and non-
kinematic errors. This model can then be applied to
more accurately plan the tasks of the manipulator.
This paper is organised as follows. In Section 2,
the forward kinematics based on POE formula along
with the Adjoint error model are presented. A method
to calculate the values of the introduced error parame-
ters based on measurement data is introduced. We de-
scribe different modeling techniques in Section 3. In
Section 4, the proposed method is applied to the per-
formance evaluation of a KUKA LBR iiwa 7 R800
manipulator and the modeling thechniques are com-
pared. We conclude our paper in Section 5.
2 ROBOT KINEMATIC AND
ERROR MODELING USING
POE FORMULA
In this section, a method applied for calculation of
error parameters is described. First the POE repre-
sentation and Adjoint error model is used to describe
the robotic manipulator. After that the difference be-
tween reference poses of a robots flange measured
by a tracking system and the corresponding nominal
poses of the robot is used to obtain the values of the
introduced error parameters.
2.1 Robot Kinematic Model
According to Brockett (Brockett, 1984), the POE
model needs two coordinate frames attached in an ar-
bitrary position. Typicaly a frame S is attached to the
robot base link and a tool frame T to the EE. The rigid
displacement of T with respect to S can be described
by a 4 × 4 homogeneous matrix g
g
g
st
as:
g
g
g
st
=
R
R
R p
p
p
0
0
0 1
(1)
where R
R
R
3×3
∈ SO(3) is an orthogonal matrix de-
scribing coordinate axes of T in S and p
p
p
3×1
∈ R
3
is
the position vector of the origin of T in S.
Each joint of the manipulator is associated with a
twist ξ
ξ
ξ
i
, i = 1, . . . , n, of the Lie algebra se(3) of SE(3)
as
b
ξ
ξ
ξ
i
=
b
w
w
w
i
v
v
v
i
0
0
0 0
(2)
where v
v
v
i
= [v
i1
, v
i2
, v
i3
]
T
∈ R
3
and
b
w
w
w
i
∈ so(3) is a
skew symmetric matrix of w
w
w
i
= [w
i1
, w
i2
, w
i3
]
T
∈ R
3
,
and is given by:
b
w
w
w
i
=
0 −w
i3
w
i2
w
i3
0 −w
i1
−w
i2
w
i1
0
(3)
The twist
b
ξ
ξ
ξ
i
can also be expresed as a 6×1 vector
ξ
ξ
ξ
i
= (v
v
v
T
i
, w
w
w
T
i
)
T
∈ R
6
. For a revolute joint, w
w
w
i
is the
Learning-based Kinematic Calibration using Adjoint Error Model
373