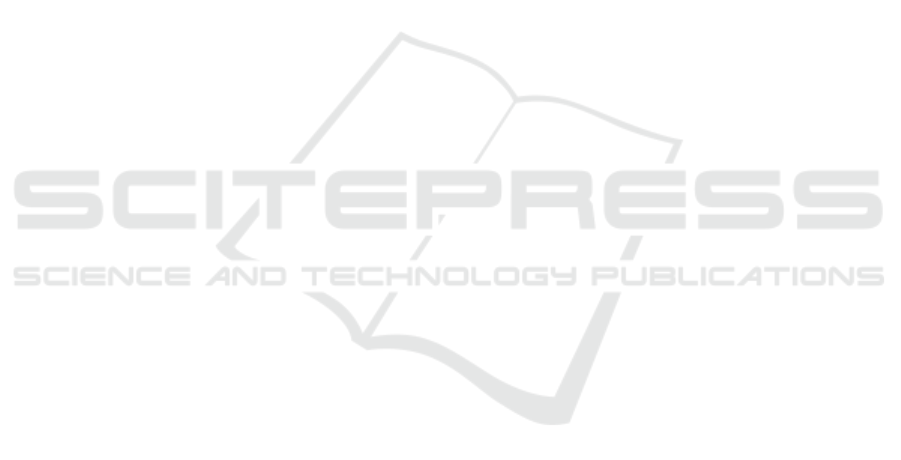
Huckaby, J., Vassos, S., and Christensen, H. I. (2013). Plan-
ning with a task modeling framework in manufactu-
ring robotics. In Proc. 2013 IEEE/RSJ Intl. Conf. on
Intelligent Robots and Systems (IROS), pages 5787–
5794.
Imeson, F. and Smith, S. L. (2014). A language for robot
path planning in discrete environments: The tsp with
boolean satisfiability constraints. In Proc. 2014 IEEE
Intl. Conf. on Robotics and Automation (ICRA), pages
5772–5777.
Kaelbling, L. P. and Lozano-P
´
erez, T. (2011). Hierarchical
task and motion planning in the now. In Proc. 2011
IEEE Intl. Conf. on Robotics and Automation (ICRA),
pages 1470–1477.
Kagermann, H., Wahlster, W., and Helbig, J., editors
(2013). Umsetzungsempfehlungen f
¨
ur das Zukunfts-
projekt Industrie 4.0 – Abschlussbericht des Ar-
beitskreises Industrie 4.0. acatech – Deutsche Aka-
demie der Technikwissenschaften e.V.
Knepper, R. A., Layton, T., Romanishin, J., and Rus, D.
(2013). Ikeabot: An autonomous multi-robot coordi-
nated furniture assembly system. In Proc. 2013 IEEE
Intl. Conf. on Robotics and Automation (ICRA), pages
855–862.
Koenig, N. and Howard, A. (2004). Design and use para-
digms for gazebo, an open-source multi-robot simula-
tor. In Proc. 2004 IEEE/RSJ Intl. Conf. on Intelligent
Robots and Systems (IROS), pages 2149–2154.
Levihn, M., Kaelbling, L. P., Lozano-P
´
erez, T., and Stilman,
M. (2013). Foresight and reconsideration in hierarchi-
cal planning and execution. In Proc. 2013 IEEE/RSJ
Intl. Conf. on Intelligent Robots and Systems (IROS),
pages 224–231.
Macho, M., N
¨
agele, L., Hoffmann, A., Angerer, A., and
Reif, W. (2016). A flexible architecture for automa-
tically generating robot applications based on expert
knowledge. In Proc. 47
th
Intl. Symp. on Robotics,
ISR 2016, Munich, Germany. VDE Verlag.
Malec, J., Nilsson, A., Nilsson, K., and Nowaczyk, S.
(2007). Knowledge-based reconfiguration of automa-
tion systems. In Proc. 2007 IEEE Intl. Conf. on Auto-
mation Science and Engineering (CASE), pages 170–
175.
McDermott, D., Ghallab, M., Howe, A., Knoblock, C.,
Ram, A., Veloso, M., Weld, D., and Wilkins, D.
(1998). PDDL — the planning domain definition lan-
guage. Technical Report TR 98 003/DCS TR 1165,
Yale Center for Computational Vision and Control.
Michniewicz, J. and Reinhart, G. (2014). Cyber-physical
robotics – automated analysis, programming and con-
figuration of robot cells based on cyber-physical-
systems. Procedia Technology, 15:566–575.
N
¨
agele, L., Macho, M., Angerer, A., Hoffmann, A., Vistein,
M., Sch
¨
onheits, M., and Reif, W. (2015). A backward-
oriented approach for offline programming of com-
plex manufacturing tasks. In Proc. 6
th
Intl. Conf.
on Automation, Robotics and Applications (ICARA
2015), pages 124–130.
Neto, P., Norberto Pires, J., and Paulo Moreira, A. (2010).
High-level programming and control for industrial ro-
botics: using a hand-held accelerometer-based input
device for gesture and posture recognition. Industrial
Robot, 37(2):137–147.
Pfrommer, J., Schleipen, M., and Beyerer, J. (2013). PPRS:
production skills and their relation to product, process,
and resource. In Proc. IEEE 18
th
Conf. on Emerging
Technologies & Factory Automation (ETFA 2013).
Pfrommer, J., Stogl, D., Aleksandrov, K., Navarro, S. E.,
Hein, B., and Beyerer, J. (2015). Plug & produce by
modelling skills and service-oriented orchestration of
reconfigurable manufacturing systems. Automatisie-
rungstechnik, 63(10):790–800.
Pires, J. N. (2006). Robotics for small and medium enterpri-
ses: control and programming challenges. Industrial
Robot, 33(6).
Reichardt, M., F
¨
ohst, T., and Berns, K. (2013). On soft-
ware quality-motivated design of a real-time frame-
work for complex robot control systems. In Proc. 7
th
Intl. Workshop on Software Quality and Maintainabi-
lity, Genova, Italy.
Rohmer, E., Singh, S. P., and Freese, M. (2013). V-rep: A
versatile and scalable robot simulation framework. In
Proc. 2013 IEEE/RSJ Intl. Conf. on Intelligent Robots
and Systems (IROS), pages 1321–1326.
Smits, R., Laet, T. D., Claes, K., Soetens, P., Schutter, J. D.,
and Bruyninckx, H. (2009). Orocos: A software fra-
mework for complex sensor-driven robot tasks. IEEE
Rob. & Autom. Mag.
Stenmark, M. and Malec, J. (2015). Knowledge-based in-
struction of manipulation tasks for industrial robo-
tics. Robotics and Computer-Integrated Manufactu-
ring, 33:56–67.
Vanthienen, D., Klotzbuucher, M., De Schutter, J., De Laet,
T., and Bruyninckx, H. (2013). Rapid application de-
velopment of constrained-based task modelling and
execution using domain specific languages. In Proc.
2013 IEEE/RSJ Intl. Conf. on Intelligent Robots and
Systems (IROS), pages 1860–1866.
Xiao, J. and Ji, X. (2001). Automatic generation of high-
level contact state space. Rob. Research, 20(7):584–
606.
Yun, S. and Rus, D. (2014). Adaptive coordinating
construction of truss structures using distributed
equal-mass partitioning. IEEE Trans. on Robotics,
30(1):188–202.
ICINCO 2018 - 15th International Conference on Informatics in Control, Automation and Robotics
612