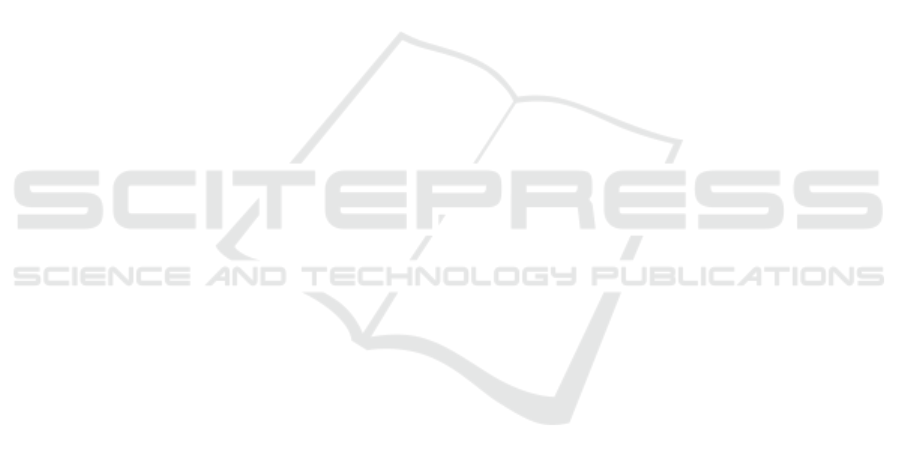
(3-D) Printing” of Titanium Alloys.” JOM 66 (7):
1299–1309. doi:10.1007/s11837-014-1007-y.
Cook, D. F., C. T. Ragsdale, and R. L. Major. 2000.
“Combining a neural network with a genetic algorithm
for process parameter optimization.” Engineering
Applications of Artificial Intelligence 13 (4): 391–96.
doi:10.1016/S0952-1976(00)00021-X.
Quality management systems - Fundamentals and
vocabulary (ISO 9000:2015). DIN EN ISO 9001:2015.
2015.
Ding, Donghong, Chen Shen, Zengxi Pan, Dominic Cuiuri,
Huijun Li, Nathan Larkin, and Stephen van Duin. 2016.
“Towards an automated robotic arc-welding-based
additive manufacturing system from CAD to finished
part.” Computer-Aided Design 73: 66–75.
Geometrical product specifications (GPS) — ISO code
system for tolerances on linear sizes. ISO 286-1:2010.
2010.
James, Gareth, Daniela Witten, Trevor Hastie, and Robert
Tibshirani. 2013. An introduction to statistical
learning: With applications in R. Springer texts in
statistics 103. New York: Springer.
Kommenda, M., B. Burlacu, R. Holecek, A. Gebeshuber,
and M. Affenzeller. 2015. “Heat treatment process
parameter estimation using heuristic optimization
algorithms.” In Proceedings of the European Modeling
and Simulation Symposium, edited by M Affenzeller,
Bruzzone, Jimenez, Longo, Merkuryev, and Zhang,
222–27.
Miller, Alan J. 2002. Subset selection in regression. 2nd ed.
Monographs on statistics and applied probability 95.
Boca Raton: Chapman & Hall/CRC.
Mohamed, Omar A., Syed H. Masood, and Jahar L.
Bhowmik. 2016. “Investigation of dynamic elastic
deformation of parts processed by fused deposition
modeling additive manufacturing.” Advances in
Production Engineering & Management 11 (3): 227–
38. doi:10.14743/apem2016.3.223.
Murtaugh, Paul A. 2010. “Methods of variable selection in
regression modeling.” Communications in Statistics -
Simulation and Computation 27 (3): 711–34.
doi:10.1080/03610919808813505.
Oliaei, Erfan, Behzad S. Heidari, Seyed M. Davachi,
Mozhgan Bahrami, Saeed Davoodi, Iman Hejazi, and
Javad Seyfi. 2016. “Warpage and Shrinkage
Optimization of Injection-Molded Plastic Spoon Parts
for Biodegradable Polymers Using Taguchi, ANOVA
and Artificial Neural Network Methods.” Journal of
Materials Science & Technology 32 (8): 710–20.
doi:10.1016/j.jmst.2016.05.010.
Park, Hong S., and Trung T. Nguyen. 2014. “Optimization
of injection molding process for car fender in
consideration of energy efficiency and product quality.”
Journal of Computational Design and Engineering 1
(4): 256–65. doi:10.7315/JCDE.2014.025.
Park, Kyung S., and Soung H. Kim. 1998. “Artificial
intelligence approaches to determination of CNC
machining parameters in manufacturing: A review.”
Artificial Intelligence in Engineering 12 (1-2): 127–34.
doi:10.1016/S0954-1810(97)00011-3.
Pawar, P. J., and R. V. Rao. 2013. “Parameter optimization
of machining processes using teaching–learning-based
optimization algorithm.” The International Journal of
Advanced Manufacturing Technology 67 (5): 995–
1006. doi:10.1007/s00170-012-4524-2.
Robinson, Carol J., and Manoj K. Malhotra. 2005.
“Defining the concept of supply chain quality
management and its relevance to academic and
industrial practice.” International Journal of
Production Economics 96 (3): 315–37.
doi:10.1016/j.ijpe.2004.06.055.
Tian, Maosheng, Xiaoyun Gong, Ling Yin, Haizhou Li,
Wuyi Ming, Zhen Zhang, and Jihong Chen. 2017.
“Multi-objective optimization of injection molding
process parameters in two stages for multiple quality
characteristics and energy efficiency using Taguchi
method and NSGA-II.” The International Journal of
Advanced Manufacturing Technology 89 (1-4): 241–
54. doi:10.1007/s00170-016-9065-7.
Venkata Rao, R., and V. D. Kalyankar. 2013. “Multi-pass
turning process parameter optimization using teaching–
learning-based optimization algorithm.” Scientia
Iranica 20 (3): 967–74.
doi:10.1016/j.scient.2013.01.002.
Widrow, Bernard, David E. Rumelhart, and Michael A.
Lehr. 1994. “Neural networks: Applications in industry,
business and science.” Communications of the ACM 37
(3): 93–105. doi:10.1145/175247.175257.
Wuest, Thorsten, Christopher Irgens, and Klaus-Dieter
Thoben. 2014. “An approach to monitoring quality in
manufacturing using supervised machine learning on
product state data.” Journal of Intelligent
Manufacturing 25 (5): 1167–80. doi:10.1007/s10845-
013-0761-y.
Wuest, Thorsten, Dieter Klein, and Klaus-Dieter Thoben.
2011. “State of steel products in industrial production
processes.” Procedia Engineering 10: 2220–25.
Xiong, Jun, Guangjun Zhang, Jianwen Hu, and Lin Wu.
2014. “Bead geometry prediction for robotic GMAW-
based rapid manufacturing through a neural network
and a second-order regression analysis.” Journal of
Intelligent Manufacturing 25 (1): 157–63.
doi:10.1007/s10845-012-0682-1.
DATA 2018 - 7th International Conference on Data Science, Technology and Applications
32