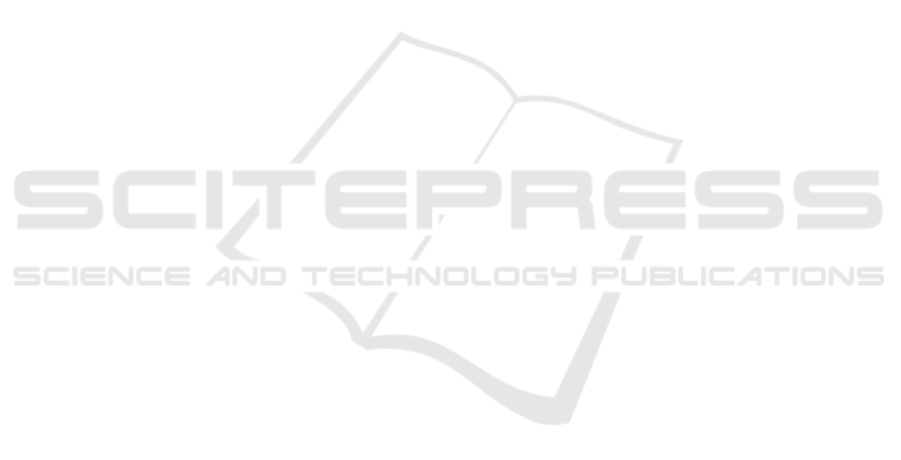
tion. This indicates that MOCS might need a rela-
tively high number of populations and executions in
order to achieve its best performance. On the other
hand, the high number of iterations in the simulation
test showed clearly the tendency of MOPSO to ge-
nerate solutions which are more concentrated in the
neighborhood of the leader particle (best global solu-
tion). This tendency was not emphasized as clearly in
the second experiment where only a limited number
of iterations is used.
7 CONCLUSION
In this work, an auto-tuning method of PID control-
lers for robot manipulators is introduced. Two multi-
objective optimization methods are considered, na-
mely MOCS and MOPSO. The main contribution of
this work is to compare the performance of the two
algorithms in the sense of achieving a good tracking
accuracy of a predefined trajectory without causing
a control action with high variations. The necessary
metrics for the comparison are considered and des-
cribed. Statistics taken from a simulation of the ro-
bot Puma 560 show clearly that MOCS is performing
much better than MOPSO with respect to all the con-
sidered metrics. The main advantage of MOCS co-
mes from the fact that its Pareto solutions have higher
spread and cover bigger region of the objective space
than the solutions of MOPSO. However, an experi-
ment on a real robot, where only a limited number of
iterations is used, showed that both algorithms perfor-
med equally well. This indicates that sufficiently high
number of populations and iterations might be neces-
sary for MOCS to achieve its best performance.
REFERENCES
Ayala, H. V. H. and dos Santos Coelho, L. (2012). Tuning of
pid controller based on a multiobjective genetic algo-
rithm applied to a robotic manipulator. Expert Systems
with Applications, 39(10):8968–8974.
Barthelemy, P., Bertolotti, J., and Wiersma, D. S. (2008). A
l
´
evy flight for light. Nature, 453(7194):495.
Coello, C. A. C., Pulido, G. T., and Lechuga, M. S. (2004).
Handling multiple objectives with particle swarm op-
timization. IEEE Transactions on evolutionary com-
putation, 8(3):256–279.
Corke, P. (2017). Robotics, Vision and Control: Funda-
mental Algorithms In MATLAB
R
Second, Completely
Revised, volume 118. Springer.
Desborough, L. and Miller, R. (2002). Increasing customer
value of industrial control performance monitoring-
honeywell’s experience. AIChE symposium series,
(326):169–189.
Eberhart, R. and Kennedy, J. (1995). A new optimizer using
particle swarm theory. Micro Machine and Human
Science, 1995. MHS’95., Proceedings of the Sixth In-
ternational Symposium on, pages 39–43.
Kim, E.-J., Seki, K., Iwasaki, M., and Lee, S.-H. (2012).
Ga-based practical auto-tuning technique for indus-
trial robot controller with system identification. IEEE
Journal of Industry Applications, 1(1):62–69.
Kwok, D. and Sheng, F. (1994). Genetic algorithm and si-
mulated annealing for optimal robot arm pid control.
Evolutionary Computation, 1994. IEEE World Con-
gress on Computational Intelligence., Proceedings of
the First IEEE Conference on, pages 707–713.
Ouyang, P. and Pano, V. (2015). Comparative study of de,
pso and ga for position domain pid controller tuning.
Algorithms, 8(3):697–711.
Pierezan, J., Ayala, H. H., da Cruz, L. F., Freire, R. Z., and
Coelho, L. d. S. (2014). Improved multiobjective par-
ticle swarm optimization for designing pid controllers
applied to robotic manipulator. Computational Intelli-
gence in Control and Automation (CICA), 2014 IEEE
Symposium on, pages 1–8.
Shi, Y. and Eberhart, R. C. (1998). Parameter selection
in particle swarm optimization. International Confe-
rence on Evolutionary Programming, pages 591–600.
Wu, J. and Azarm, S. (2001). Metrics for quality assessment
of a multiobjective design optimization solution set.
Journal of Mechanical Design, 123(1):18–25.
Yang, X.-S. and Deb, S. (2009). Cuckoo search via l
´
evy
flights. pages 210–214.
Yang, X.-S. and Deb, S. (2013). Multiobjective cuckoo se-
arch for design optimization. Computers & Operati-
ons Research, 40(6):1616–1624.
Zidan, A., Kotlarski, J., and Ortmaier, T. (2017). A practi-
cal approach for the auto-tuning of pd controllers for
robotic manipulators using particle swarm optimiza-
tion. 14th International Conference on Informatics in
Control, Automation and Robotics, pages 34–40.
Zitzler, E. and Thiele, L. (1998). Multiobjective optimiza-
tion using evolutionary algorithmsa comparative case
study. pages 292–301.
A Comparative Study on the Performance of MOPSO and MOCS as Auto-tuning Methods of PID Controllers for Robot Manipulators
247