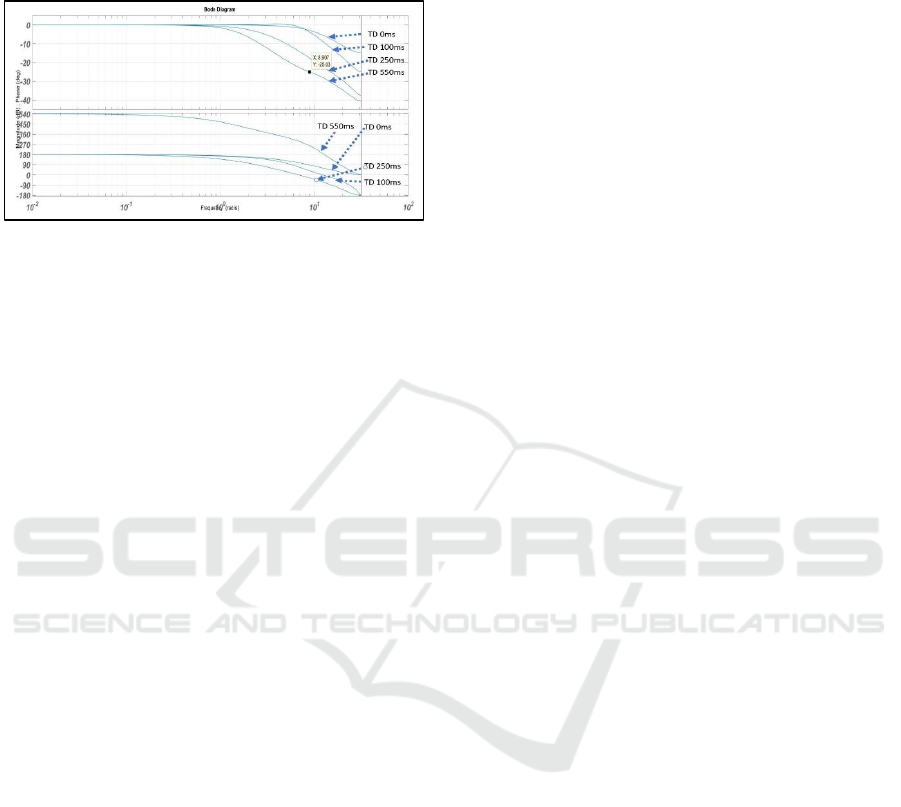
system increases demanding for more computation
power. Since the system gets the linearised system is
controllable even when the frequency is increased.
Figure 14: Bode plot for the system under different time
delays.
4 DISCUSSIONS
MPC as a force controller can be used to develop
haptic feedback in a surgical system suffering
from time delays.
The approach’s effectiveness was tested in
different scenarios and results were compared
with the observations of the previous work by
researchers. MPC shows a stable response in all
the scenarios.
MPC can be used even when the time delay is
more significant than 500ms and shows the
system is robust enough to carry out the surgery.
The response of the system gets slower when
time delay goes beyond 500ms increasing total
time to carry out the operation.
Previewing can be used to compensate for the
dead time using MPC when reference is known.
The response of the system is closer to a delay-
free system in that case. This feature can be used
in surgical robots with the capability of
performing in autonomous mode.
5 FUTURE WORK
Introducing impact and velocity model into the
system to have a zero-impact velocity during the
contact is the proposed future work. Such work will
also show the more considerable difference in the
performance of MPC over PID. Gain scheduling
using MPC can help to handle the system with
random delays.
6 CONCLUSIONS
In this paper, force feedback by using Model
Predictive Control (MPC) for surgical robots was
developed and discussed that will give an extra
dimension to the existing surgical systems. MPC can
compensate the time delays when the delays are
known by previewing. The goal is to design control
signal at each sampling time k such that state
feedback law minimises the cost function to
constraints of control input. The benefit of using the
previewing in case of known references helps
controller to predict the delayed free future.
Simulation experiments show the effectiveness of the
concept.
REFERENCES
Tachi, S., Arai, H. & Maeda, T., 1990. Tele-existence
master-slave system for remote manipulation. II. 29th
IEEE Conference on Decision and Control, pp.85–90.
Buss, M. & Schmidt, G., 1999. Control Problems in Multi-
Modal Telepresence Systems. Advances in Control,
pp.65–101.
Ortmaier, T., Reintsema, D., Seibold, U., Hagn, U. and
Hirzinger, G., 2001. The DLR minimally invasive
robotics surgery scenario. Hieronymus
Buchreproduktions GmbH, München Proceedings.
Preusche, C., Ortmaier, T. and Hirzinger, G., 2002.
Teleoperation concepts in minimal invasive
surgery. Control engineering practice, 10(11), pp.1245-
1250.
Lanfranco, A.R., Castellanos, A.E., Desai, J.P. and Meyers,
W.C., 2004. Robotic surgery: a current
perspective. Annals of surgery, 239(1), p.14.
Guthart, G.S. and Salisbury, J.K., 2000. The Intuitive/sup
TM/telesurgery system: overview and application.
In Robotics and Automation, 2000. Proceedings.
ICRA'00. IEEE International Conference on (Vol. 1,
pp. 618-621). IEEE.
Hannaford, B., Friedman, D., King, H., Lum, M., Rosen, J.
and Sankaranarayanan, G., 2009. Evaluation of
RAVEN surgical telerobot during the NASA extreme
environment mission operations (NEEMO) 12
mission. Electrical Engineering Department,
University of Washington, SeattleTech. Rep, 2.
Hannaford, B. and Okamura, A.M., 2008. Chapter 30:
Haptics, Handbook of Robotics.
Arata, J., Takahashi, H., Pitakwatchara, P., Warisawa, S.I.,
Tanoue, K., Konishi, K., Ieiri, S., Shimizu, S.,
Nakashima, N., Okamura, K. and Fujino, Y., 2007,
April. A remote surgery experiment between Japan and
Thailand over Internet using a low latency CODEC
system. In Robotics and Automation, 2007 IEEE
International Conference on (pp. 953-959). IEEE.
Marescaux, J., Leroy, J., Gagner, M., Rubino, F., Mutter,
D., Vix, M., Butner, S.E. and Smith, M.K., 2001.
Force Control of Surgical Robot with Time Delay using Model Predictive Control
199