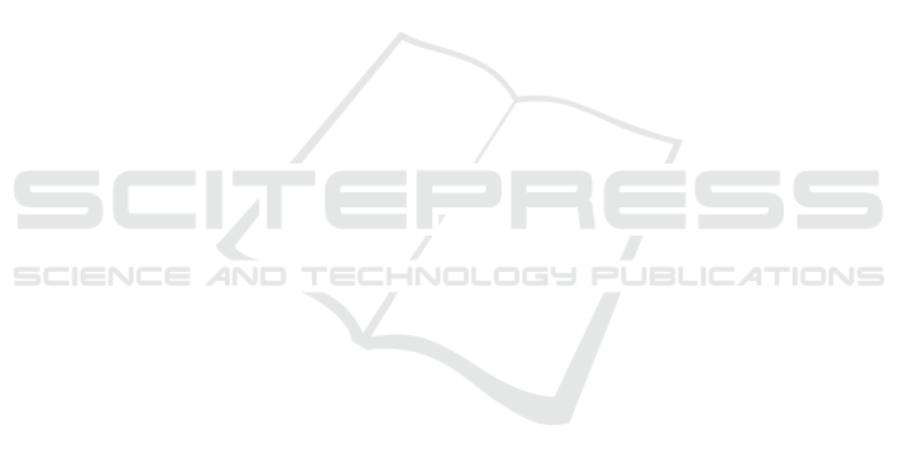
2 RELATED WORK
In general, there are three methods of initial tuning of
controllers for multirotor aerial platforms. The first
solution is based on the expert knowledge of the team
of engineers and parameters obtained during develop-
ment of previously constructed vehicles. If there are
no major differences in the airframe design and pro-
pulsion setup, there is a high probability that a new
design will require only some minor, in-flight tuning.
This is a situation very common in development pro-
jects, where new iterations of market products are re-
leased. However, there may be differences not only
in physical parameters and performance but in me-
chanical vibrations due to use of different materials
and specific aspects of structural design. It is a well-
known issue leading to errors and inadequacies in the
state estimation which automatically leads to failure
in the control process. To sum up, even in this ap-
proach it is recommended to test platform in the test
stand before carrying out free flight experiments.
The second method depends on the complete mat-
hematical model of the developed platform. Unfortu-
nately, it is hard to utilise such model for newly con-
structed UAV, while there is no data to tune the mo-
del itself. Sometimes the sub-models are used to sim-
plify this process. In such case, the problem is divi-
ded into several simpler simulations, i.e. concerning
single axis of rotation. In addition, noise in sensor re-
adings has a great impact on control quality as well.
Therefore, there is a requirement to perform noise le-
vels trimming.
Third approach utilises various test benches ((Pa-
nizza et al., 2016), (Bondyra et al., 2017), (Hoffmann
et al., 2010), (Tayebi and McGilvray, 2006)), which
allow performing tuning process in safe, laboratory
conditions without the risk of damaging the equip-
ment in-flight. In addition, this method is based on
the trial and error technique. Without reaching into
the details of mathematical modelling, parameters are
chosen on the basis of rules corresponding to the type
of the applied control technique. This process can
also be automated which leads to the reduction of
tuning time (Wang and Poksawat, 2017) (Howard,
2017). It has to be mentioned, that platform during
the tuning process on the test bench can change its
physical characteristics, since fixing the UAV in test
rig influences mainly the vibration levels in compari-
son to the in-flight performance. Test bench usually
dampens vibrations due to the dispersion in extended
mechanical structure. Therefore, during the real flight
tests, noise amplitude can be significantly higher, dis-
turbing state estimation and flight control. Another
important issue with fixing the UAV to the stationary
bench is the introduction of friction in axes of rota-
tion. Omitting this phenomenon causes higher overs-
hoot during flight attitude stabilisation.
Every mentioned approach has its own advanta-
ges and disadvantages since there is no perfect rou-
tine. A hybrid and flexible method described in the
next section constitutes the novel and safe approach
to selecting initial parameters of the flight controllers
with the high success rate preserved.
Proposed tuning process was used in various mo-
difications of the control algorithm in the Falcon V5
platform and during initial tuning of the Kruk UAV.
Both vehicles, shown in the Fig. 1, are quite different
in the terms of size, payload capabilities and configu-
ration of the propulsion system. The Falcon V5 UAV
was developed as an indoor research aerial platform
with extended lift capabilities. It is equipped with 8
motor-propeller sets arranged on 4 symmetrical arms
in the coaxial configuration. Such approach allowed
to achieve up to 6kg of maximum thrust force within
2.7kg of the UAV’s own mass. Payload capabilities
reach up to 1kg of equipment with the flight time of 12
minutes. On the other hand, the Kruk UAV is desig-
ned as asymmetrical hexacopter with heterogeneous
propulsion system consisting of four single units and
two double, coaxial ones. This UAV has the ability to
lift several kilograms of payload with the flight time
extended up to 40 minutes. However, both vehicles
were successfully developed, tuned and tested thanks
to the procedure described in this article.
3 METHOD DESCRIPTION
The proposed method is based on a fusion of previ-
ously mentioned solutions. It uses simple models of
propulsion units, gathered from the test bench, and
physical information about hardware from the CAD
software. This approach, connected with experimen-
tal verification on the rotary test stand, results with in-
creased safety of tuning process, especially with high
thrust platforms.
As mentioned above, the first element of the pro-
cedure is a model of the propulsion unit. It is develo-
ped on the basis of measurements from the propulsion
analysis system presented in (Aszkowski et al., 2017)
showed in Fig. 2. This test rig provides measure-
ments of thrust, reaction torque, angular velocity and
power consumption in relation to the duty cycle of
the control signal. Such equipment is especially use-
ful in case of coaxial propulsion units, which are way
harder to model in a mathematical manner. Sensors
of the propellers’ angular velocity are rarely available
on the multirotor UAVs, therefore all models have to
ICINCO 2018 - 15th International Conference on Informatics in Control, Automation and Robotics
466