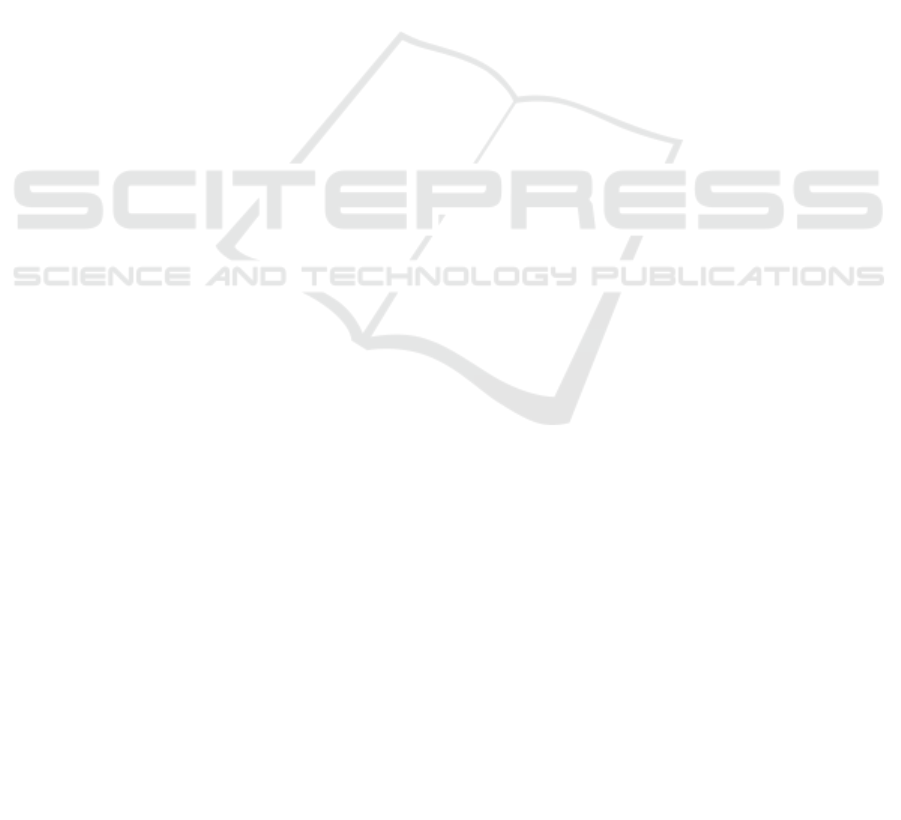
Missing Rail Fastener Detection Based on Machine Vision Method
Yongzhi
Min
1*
,
Benyu Xiao
1
, Hongfeng Ma
2
and Biao Yue
1
1
School of Automation and Electrical Engineering, Lanzhou Jiaotong University, Lanzhou, China
2
School of Electronical Information Engineering, Lanzhou Institute of Technology, Lanzhou, China
su_ymin01@qq.com, 13893178455@163.com, 13609345559@139.com, 1440127943@qq.com
Keywords: Fastener missing detection, area positioning, template matching, occlusion removal, machine vision,
minimum distance classifier.
Abstract: Rail fastener missing detection is an important part of railway daily inspection, according to the need of
modern railway automatic detection, a method of rail fastener missing detection based on template matching
is proposed in this paper. Firstly, in order to deal with the interference of environmental light, according to
the basic principle of machine vision, a simple rail inspection car is designed for image acquisition. Secondly,
according to the characteristics of the track image, the rail fastener area is located by using the mutation
information of the image. Then, through the establishment of template, test images are matched with the
template image, when the matching degree between test images and template images is low, it is need to detect
the occlusion area of the test image and if there is a occlusion in the test image, remove the occlusion area
from the test image and sample images to obtain new sample images and test image. Finally, the minimum
distance classifier is used to detect the missing rail fastener. Simulation results show that the correct detection
rate of this algorithm is 93.7% and the average detection time of each image is 385.74 ms, providing a
reference for real-time detection of railway line.
1 INTRODUCTION
With the rapid development of high-speed railway,
how to ensure the safe operation of the train has
attracted more and more attention of the public. Track
fastener is an important component for connecting
rail and track sleeper, playing an important role of
holding on the track gauge and preventing the rail
from vertically and horizontally moving relative to
the track sleeper, once be lost will bring security risks
to the safe operation of the train(Gibert, et al, 2017).
In recent years, many domestic and foreign
scholars have done a lot of research on the detection
of missing track fastener and have obtained some
achievements. Among them, Wang L et al.(2011) use
principal component analysis (PCA) algorithm to
extract the feature vector of the rail fastener nut and
use the minimum distance classifier to detect the
fastener. Yang J et al. (2011) use the orientation field
algorithm and the template matching method to detect
the state of the rail fastener. Jia L H(2014) carries on
processing to the image edge by using mathematical
morphology, intercepts the sub module from the test
images to match with the standard rail fastener image
and uses the support vector machine (SVM) method
to detect the missing fastener. Yan F(2014) extracts
the edge feature of the fastener image, and then
respectively use the BP neural network and fuzzy C
mean clustering method to identify the missing
fastener.
The existing researches mainly focuses on the
case that the track fastener image is not be occluded.
In that case, the local characteristics of rail fastener is
not interfered by the external environment and can be
easily extracted. However, the track fasteners may be
obscured by such as fallen leaves or food bags et al.
in the actual railway lines, causing some of local
features of track fastener be split and cannot be
accurately extracted.
Taking into account the situation that rail fastener
may be obscured by some occlusions, a method based
on machine vision method for the detection of
missing rail fastener is proposed in this paper. Firstly,
the rail fastener area is located by using the position
relationship among components of the track image.
Then, select a track image that contains rail fastener
a track image lacking of track fastener as the sample
images, and the test image is compared with the
sample images. When there is a high matching degree
between the test image and the sample images, the
Min, Y., Xiao, B., Ma, H. and Yue, B.
Missing Rail Fastener Detection Based on Machine Vision Method.
In 3rd International Conference on Electromechanical Control Technology and Transportation (ICECTT 2018), pages 119-124
ISBN: 978-989-758-312-4
Copyright © 2018 by SCITEPRESS – Science and Technology Publications, Lda. All rights reserved
119