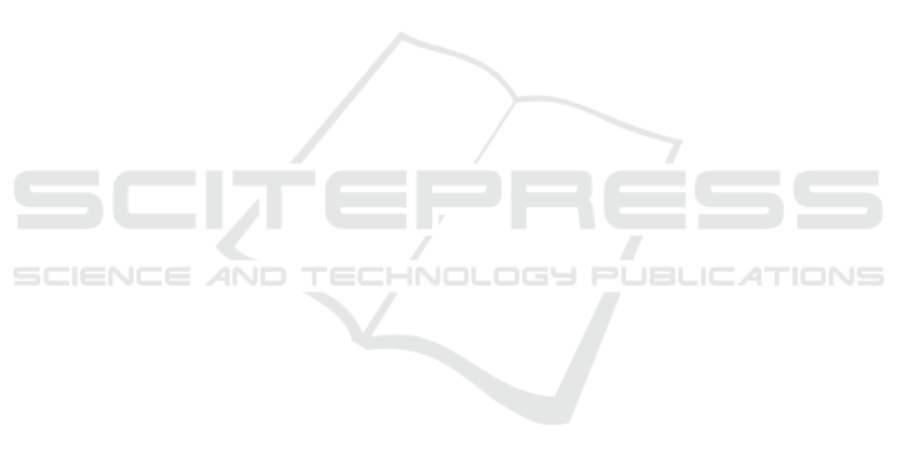
JBC, BEISSBATH, CORCHID, Three Jay Yi , and
so on.
Dynamic measurement refers to the method of
measuring the vehicle wheel alignment in the
moving state. The toe-in angle, track width, the
wheelbase and the inclination angle are all directly
when the vehicle is driving while they are distorted
in the stationary state, which are influenced by many
factors such as rim distortion, chassis clearance,
suspension deformation and heavy load. Thus, the
dynamic measurement becomes the mainstream
measurement method with higher precision. The 3D
wheel aligner is one of the most widely used
measurement equipment in the market, which is
attributed to its use of three-dimensional dynamic
measurement and the fast algorithm to achieve a
qualitative leap in principle, precision and real-time,
such as the JBC-V3D of the United States, the
German BOSCH-FWA4510, etc. The device has
many advantages such as high measurement
efficiency, accurate measurement and low failure
rate.
3 KEY TECHNOLOGY OF
DEVELOPING FOUR-WHEEL
ALIGNER
3.1 Measuring Datum and Positioning
Mode
There are two important rotating axes that affect the
four-wheel alignment, the steering axis of steering
wheel when turning and the rolling axis of the
wheel. Among them, the kingpin inclination angle
and the caster angle are the two-dimensional angle
of the steering axis, the camber angle and the toe-in
angle are two dimensional angles of the rolling axis
(ZHANG Mei, 2008). In addition, the four-wheel
positioning datum also comprises a OXY plane of
vehicle coordinate system, a geometrical centreline
and a thrust line.
The OXY plane refers to a plane formed by the
center of the front and rear axles, and the thrust line
is an imaginary line obtained from the intersection
of the two rear wheels plane and the OXY plane
(ZHAO Qiancheng, 2013). The positioning method
of the coordinate relation between the four wheels
and the suspension in the direction of X, Y and Z
axes is called the four-wheel alignment of the thrust
line, which takes the angular split line of the toe-in
angle of the rear wheel as the body Motion Center,
regardless of the body center offset (WEN Dong,
2009). Using the thrust line positioning, the first step
is to determine the position of the thrust line by
measuring the rear wheel, and then the thrust line is
used as reference to adjust the toe-in angle of the
directive wheel. When the thrust line does not
coincide with the geometrical centerline, the four
wheels deviate from the geometrical centerline,
which means that the deviation direction and
abnormal wear of the tires will appear when the
vehicle is running in a straight line.
The geometric centerline is the connection line
of the midpoint of the front and rear axle of the
vehicle, and it can be used as a reference to adjust
the toe-in angle of the wheel. When the rear wheel is
in the correct position, the adjustment of the front
wheel to the geometric centerline and the thrust line
coincide, the positioning effect is the best. Once the
rear wheel position is offset or the geometrical
centerline is not coincident with the thrust line, the
steering performance of the vehicle will be affected.
Therefore, the rear wheel alignment will be ignored
when the front wheel is adjusted with the geometric
centerline as the datum.
For modern four-wheel aligners, most of them
have the ability of complete four-wheel alignment.
The positioning method of the coordinate
relationship between the four wheels and the
suspension in the direction of X, Y and Z axes which
takes the wheel thrust line as the Body Motion
center line is called the complete four-wheel
alignment (WEN Dong, 2009). The specific
operation is to take the geometric centerline as the
datum, and realize the change of the relative position
between the thrust line and the geometrical center
line by adjusting the thrust angle continuously.
When the thrust line is coincident with the
geometrical centerline, the thrust line or the
geometrical centerline is used as reference, and the
wheel alignment is accomplished by adjusting the
toe-in angle of the directive wheel. Once the four
wheels are adjusted, the direction of each wheel is
parallel to the geometric centerline, at which time
the vehicle has the best running performance. This
method is by far the most ideal adjustment for four-
wheel alignment(XU Guan, 2009).
3.2 Measuring Principle of Typical
Four-wheel Aligners
The traditional four-wheel aligners ,such as pull-line
aligner and laser aligner, all use inclination sensors
to measure the kingpin angle and the camber angle
directly, and the steering wheel is positioned in the
center position before measuring. The measuring
ICECTT 2018 - 3rd International Conference on Electromechanical Control Technology and Transportation
556