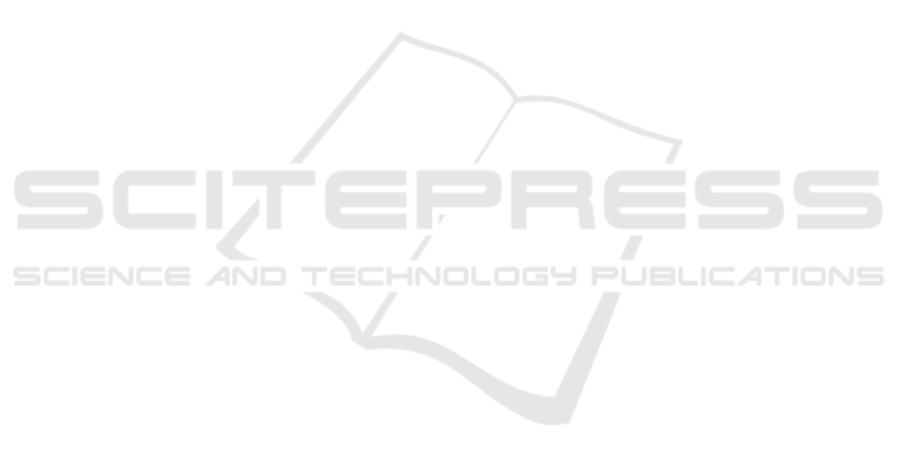
Sensitivity Analysis of Design Parameters on Fluidlastic
Isolators Performance
J H Deng and Q Y Cheng
*
Science and Technology on Rotorcraft Aeromechanics Laboratory, China Helicopter
Research and Development Institute, Jingdezhen 333001, China
Corresponding author and e-mail: Q Y Cheng, qy_cheng@163.com
Abstract. Control of vibration in helicopters has always been a complex and challenging task.
The fluidlastic isolators become more and more widely used because the fluids are non-toxic,
non-corrosive, nonflammable, and compatible with most elastomers and adhesives. In the
field of the fluidlastic isolators design, the selection of design parameters is very important to
obtain efficient vibration-suppressed. Aiming at getting sensitivity of property of fluidlastic
isolator to design parameters, a dynamic equation is set up based on the theory of dynamics.
The orthogonal experimental method is used to analyze the parametric sensitivity of the
design parameters on the property of fluidlastic isolator. Two control indexes for design are
taken as the experimental indexes, and five parameters influencing the property of the isolator
are taken as the experimental factors. Arranged for the tests based on the orthogonal
experiment table, 2 indexes 6 factors orthogonal experiment is carried out. Range analysis is
adopted to study the sensitivity. The results show that for the combustion efficiency of
dynamic stiffness of fluidlastic isolator, the order of significance levels in turn decreases with
η, K
1
, c , L, ρ and K
2
respectively. For the combustion efficiency of dynamic stiffness of
fluidlastic isolator, the order of significance levels in turn decreases with η, K
1
, c, K
2,
ρ and L
respectively.
1. Introduction
Helicopter vibration is a critical aspect of helicopter design and a major reason for extended lead time
during the aircraft development phase. Control of vibration in helicopters has always been a complex
and challenging task. Increasing demands for expanding the flight envelop of helicopters, such as nap
of earth flying, high speed, high maneuvers, coupled with the need to improve system reliability and
reduce maintenance costs has resulted in more stringent vibration specifications.
Various methods have been applied to vibration control in the engineering field [1-5].
Traditionally, passive isolators and dampers are used to attenuate mechanical vibrations. The
traditional approach to passive vibration isolation is to install relatively soft springs or elastomeric
isolators to provide a primary low natural frequency [6-9]. These isolators would also incorporate
sufficient damping to control resonant response. Soft systems with primary natural frequencies well
below the N/rev exciting frequency are required to achieve isolation. Such systems result in large
relative motion between the pylon and the airframe due to static loads. Natural frequencies low
enough to isolate N/rev vibration would have static (1G) deflections up to 0.50 inches. Since flight
64
Deng, J. and Cheng, Q.
Sensitivity Analysis of Design Parameters on Fluidlastic Isolators Performance.
In Proceedings of the International Workshop on Materials, Chemistry and Engineering (IWMCE 2018), pages 64-70
ISBN: 978-989-758-346-9
Copyright © 2018 by SCITEPRESS – Science and Technology Publications, Lda. All rights reserved