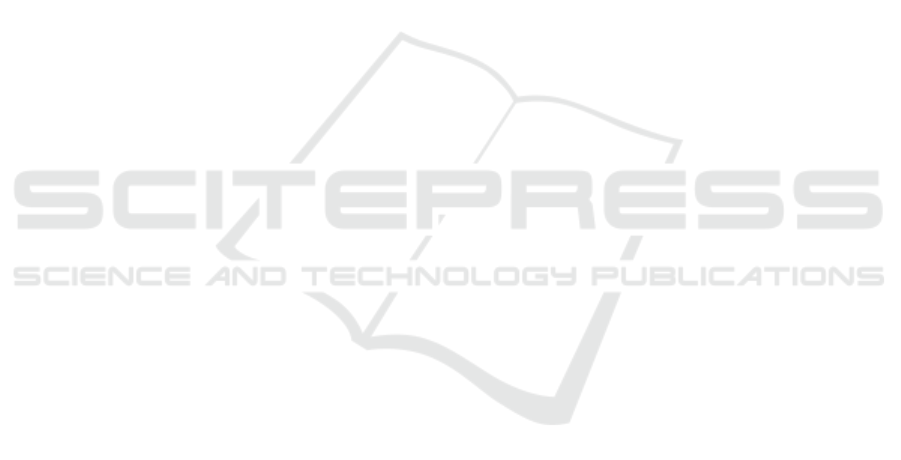
between surface roughness, tactile sensation and roughness[10, 14], the effect of wood treatment
conditions on surface roughness
[18], Application of image processing method in surface roughness
measurement[19, 20, 21], Effect of surface roughness on finishing treatment[22, 23], the influence of
material on surface roughness[24, 25, 26], the study of the influence of cutting tool and tool material
on surface roughness[27, 28], basically covers various factors that affect the surface roughness of
wood processing. With the continuous improvement of people's living standard and the rapid
development of wood industry, building decoration industry and furniture industry, the surface
quality requirements and importance of wood parts are more and more high. The surface roughness
not only affects the appearance quality of wood parts, but also affects the processing technology and
production cost. However, at present, there is no special measuring equipment and the ideal
evaluation method. The measuring parameters and standard methods of surface roughness of wood
parts are developed on the basis of the standardized measurement theory of the contact needle
homogeneous materials [29, 30, 31]. The method of surface roughness measurement can be divided
into two types: contact measurement and non-contact measurement. Contact measurement mainly
refers to the stylus type measurement, this method can reproduce the surface condition of workpiece,
but it is easy to damage the surface of the workpiece, at the same time the size of probe needle
directly affects the precision of measurement, low measurement precision, and can not directly
identify the structure of wood, it is difficult to meet the requirements of modern measurement
technology. Non-contact measurement has the advantages of fast, non-contact, non-destructive and
high precision, which is paid attention to by people. The Non-contact method, represented by the
laser method with high measurement accuracy and relative measuring speed, is more suitable for the
determination of wood surface roughness. In this study, a shape measuring laser microscope system
was used to determine the surface roughness of wood with different parts, different processing modes,
different magnification and different test modes, so as to propose a method for evaluating the surface
roughness of wood processing.
2. Materials and methods
2.1. Test materials
The Elm (Ulmus rubra) and Poplar (Populus beijingensis) used in this experiment were taken from
the woodland of Yuquan District Dalai Zhuang village, Hohhot. The age of Elm is 45-48 years. The
sapwood is consisted of 6 rings; Heartwood is consisted of 41rings. The ring width distribution of
0.35-7.90mm and the average diameter of ring is about 303mm.
Poplar is of 34-37 years. The sapwood is consisted of 13 rings, while heartwood of 23. The ring
width distribution is of 0.57-9.68mm and the average diameter is of 315mm.
Pinus sylvestris was obtained from the Forest in the Ude (Ulam) region of Russia, with the age of
79-83 years. The Sapwood has about 44 rings, the heartwood is consisted about 38. The ring width is
from 0.21 to 3.65mm and the average diameter is about 310mm.
2.2. Sample processing
Each log selected two sections after the cross-section saw into a disk-wood section, the disk of wood
at intervals 90° intercept 50mmx50mmx70mm hardness test block, with 80 mesh abrasive belt
grinder sanding into a specimen. Sawing machine with rotational speed of 3600rpm rotary sawing
machines. Log cross-section saw the processing of 40mm wide rotary cutting wood section, with the
modified lathe to spin cut out the chip samples, cutting edge arc radius 0.3m [32], cutting thickness
of 0.32mm.
IWMCE 2018 - International Workshop on Materials, Chemistry and Engineering
84