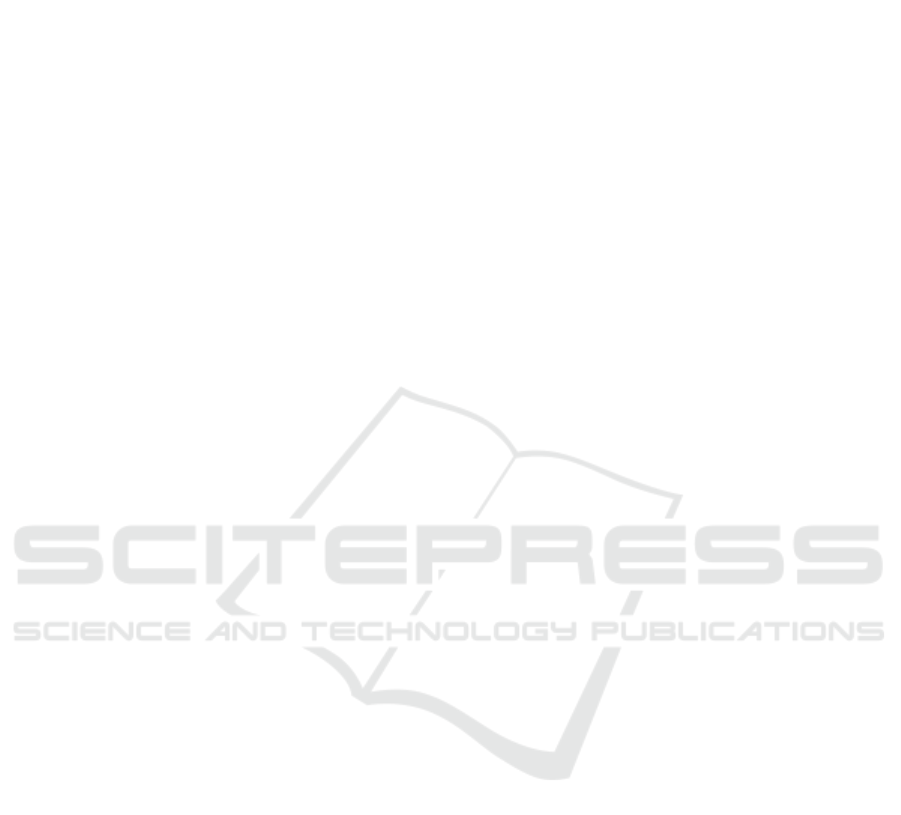
particle size of SiO
2
, and the application is limited.
In this paper, we focused on the influence of mixing process of SiO
2
nanoparticles and binder on
interface structure between micro/nano structure and glass. The voids and holes on the interface were
controlled, and mechanically robust transparent superhydrophobic coatings were successfully
prepared on glass.
2. Experimental
2.1. Preparation of micro/nano structural coatings
Reagents: tetraethoxysilane (TEOS), ethanol, coupling reagent (KH560), deionized water, dilute
nitric acid, commercial hydrophilic SiO
2
nanopowder A380 (7 nm, Degussa) and A200 (25nm,
Degussa), and fluoroalkylsilane (1H, 1H, 2H, 2H-perfluorodecyl three chlorinated silane) were used
as received.
The preparation of acidic SiO
2
sol is based on our previous report [14]. TEOS was hydrolyzed in
aqueous-ethanol solution of dilute nitric acid and KH560 was added as coupling reagent.
0.2 g of A380 SiO
2
nanopowder and 0.2 g of A200 SiO
2
nanopowder were added to 20 g of
ethanol, stirred for 50 min, and sonicated for 1 h to prepare SiO
2
nanopowder dispersion sol (labeled
as AA sol). 2.5 g of AA sol was mixed with 1.0 g of the prepared acidic SiO
2
sol and 4.0 g of
isopropanol, sonicated for 1 h to prepare a mixed sol of SiO
2
nanopowder and acidic SiO
2
sol
(labeled as AAS sol).
A commercial green glass of 50 mm x 50 mm x 3.2 mm pre-treated by polished and
decontaminated was used as substrate. Before coating, glass substrate was chemically activated by
ultraviolet ozone irradiation (UVO irradiation, 10 min) to form a highly active hydroxyl polar surface
[15]. The sol was coated onto glass substrate by spin coating with a KW-4A homogenizer (speed 600
rpm, time 10 s), followed by pre-curing at 80 °C for 20 min and solidification at 180 °C for 1 h.
Monolayer coatings were prepared as follows. In order to study interface structure of monolayer
coatings, (1) acidic SiO
2
sol, (2) AA sol and (3) AAS sol were coated on glass substrate to fabricate
monolayer coatings of (1) SiO
2
gel (labeled as sample S), (2) SiO
2
nanoparticle aggregation (labeled
as sample AA), and mixed SiO
2
nanoparticle with SiO
2
gel (labeled as sample AAS), respectively.
Bilayer coatings were prepared as follows. In order to study interface structure of bilayer coatings,
at first, acidic SiO
2
sol was coated as under-layer. After air-dried and UVO irradiated, (4) AA sol and
(5) AAS sol were coated as upper layer to fabricate bilayer coatings of (4) SiO
2
gel/SiO
2
nanoparticle
aggregation (labeled as sample S/AA), and (5)SiO
2
gel/mixed SiO
2
nanoparticle with SiO
2
gel
(labeled as sample S/AAS), respectively.
Fluoroalkylsilane modification was implemented by chemical vapor deposition according to
reference [16]. The coated glass was placed in the reactor with polytetrafluoroethylene as inner tank,
on the bottom of which was distributed three droplets of 1H, 1H, 2H, 2H-perfluorodecyl three
chlorinated silane. There was no direct contact between the coated glass and the droplets. The reactor
was heat treated at 120 °C for 2 h, after natural cooling, the coated glass was removed and heat
treated at 150 °C for 1.5 h.
2.2. Characterizations
Abrasive resistance was conducted according to ISO 5470-1:2016 using a reciprocating linear
wear-resistance instrument (x-5750-J, Shenzhen Xinhengsen Trading Co., Ltd.), under condition of
load of 1 kg/cm
2
and reciprocating 200 times. Interface structure before and after abrasion was
observed using a scanning electron microscope (SEM, SU-70, Hitachi) with an accelerating voltage
of 5 kV. Since conductivity of glass sample was poor, sample surface was treated with gold spray
IWMCE 2018 - International Workshop on Materials, Chemistry and Engineering
94