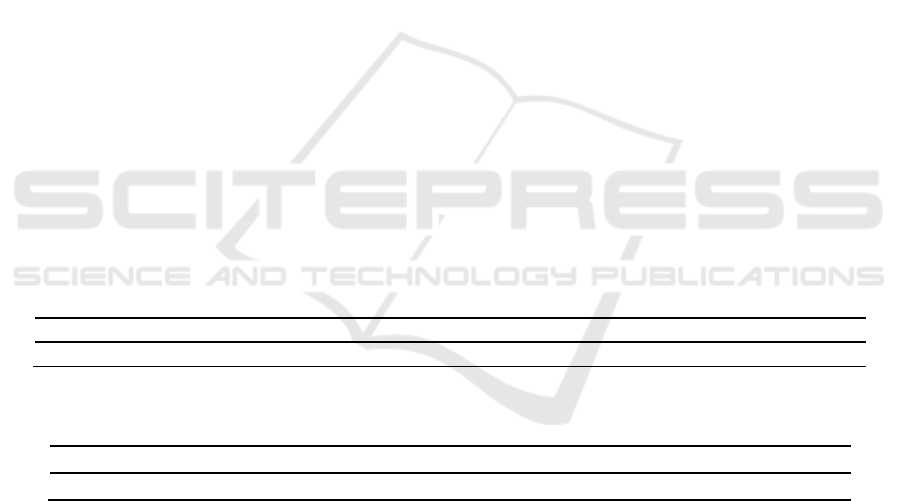
phases. They pointed out that the FeSi
2
Ti phase became enriched with P in the Ca-alloyed samples,
however, no P content was detected in CaSi
2
phase in their work.
Slag treatment using CaO-based slag coupled with acid leaching is also applied in removing metal
impurities and P elimination from Si. In our previous study [11], we found that part of P was likely
reduced to Ca-Si-P compounds uniformly distributed into the CaSi
2
phase among Si grains after a
short period of slag refining using CaO-SiO
2
-CaF
2
system under air atmosphere, and the scattered
distributed CaSi
2
phase contributed to the removal of Fe, Al and Ca impurities from MG-Si. And, it
is found that the removal effect had a positive correlation with the content of Ca in Si.
However, research on the effect on the removal of B from Si by slag treatment using CaO-based
slag or by alloying with Ca has not been conducted so far. In the present paper, the result of slag
refining using CaO-based slag is simulated, a certain amount of Ca-Si alloy is molten with MG-Si to
be refined in medium frequency induction, which results in a certain amount of Ca in Si. And the
distribution of B and P in Si and CaSi
2
, the removal efficiency of B and P will be discussed.
2. Experiments
2.1. Alloy refining
The alloy refining experiments was conducted in a laboratory scale medium frequency induction
furnace. Si-Ca alloy used in this study was provided by Shaanxi Shenghua metallurgical Co. Ltd.,
and its element analysis was shown in Table 1. The composition of MG-Si to be refined in the
present paper was shown in Table 2. Samples of MG-Si and Ca-Si alloy were placed in a high-purity
dense graphite crucible (99.99%, 45 mm outer diameter, 30 mm inner diameter, 120 mm height, and
105 mm depth). Thereafter, the crucibles with the samples were placed in medium frequency
induction furnace. After melting and holding at 1723 K ± 20 K for 10 min, the samples were cooled
to 1273 K at 10 K/min for solidification refining. After cooling to room temperature, the samples
were cut into pieces, and some parts were polished to examine the morphology and microarea
composition by SEM-EDS.
Table 1. Contents of main elements in Ca-Si alloy.
Table 2. Content of main impurities in MG-Si analyzed by ICP-AES.
2.2. Acid leaching
Samples after alloy refining were crushed into powder to be leached with aqua regia (HCl:HNO
3
=
3:1 by volume, diluted by deionized water by volume ratio of 3:2) and HF (diluted by deionized
water by volume ratio of 1:1) successively at room temperature for 1 hour, respectively. Finally, the
concentrations of impurities in the leached Si powder was analyzed by inductively couple plasma-
atomic emission spectroscopy (ICP-AES, Thermo Fisher iCAP 6300).
3. Results and discussions
According to the content of Ca and Si in CaSi
2
listed in Table 1, the raw material Ca-Si alloy can be
considered as a mixture of CaSi
2
and Si. In our previous study [11], it’s found that CaSi
2
phase was
produced among the silicon grains after slag treatment by CaO-SiO
2
-CaF
2
system. After solvent
refining, CaSi
2
will be produced by a eutectic reaction at 1301 K during the cooling of Ca-Si melt
IWMCE 2018 - International Workshop on Materials, Chemistry and Engineering
128