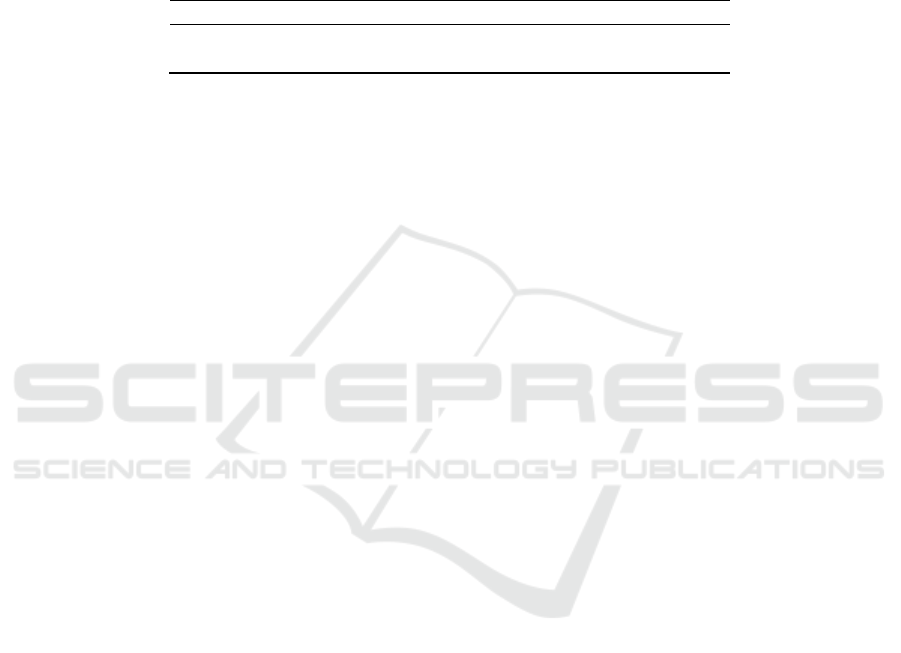
The erosion groove size of 60° specimen for precipitation hardening steel at different times are
shown in table 3. It can be seen that the expansion rate of width was obviously higher than that of
depth at the beginning of the experiment, which indicates that the main reason for the expansion of
the grooves is the shear effect of the lateral jet at this stage. After that, due to the formation of water
film on the side wall, the expansion of the groove width is slowed down.
Table 3.Characteristic sizes of erosion grooves for 60° specimen of precipitation hardening steel.
5. Conclusions
The experimental investigation on water erosion characteristics of three kinds of structural steel
materials at three impact angles was carried out in the present study. A detailed analysis of the water
erosion characteristics of each material of each stage and the curves of mass loss were obtained.
The water erosion resistance of three kinds of materials were compared based on the incubation
time (Ip) and maximum erosion rate (Q
e
). According to the mechanical parameters of materials, it is
found that the incubation time is mainly influenced by elastic modulus and shear modulus. Once the
defect occurs, the effect of hardness and tensile strength on the material is gradually enhanced.
The influence of impact angle on the water erosion resistance of materials was studied. On the one
hand, the greater impact angle causes the greater erosion rate. On the other hand, the 60° specimen
shows the shortest erosion incubation period for the testing three materials, which indicates that there
is the most dangerous water impact angle under the present experiment condition.
For the erosion grooves, the expansion rate of width was 2 times greater than that of the depth in
the early stage of the experiment, which indicates that the lateral jet produced by high-speed jet
impingement is the main factor of erosion groove expansion. Once the defect on the surface formed,
the shear effect of the lateral jet accelerated the expansion of the groove size, which resulted in the
acceleration of the mass loss. In the late erosion stage, due to the formation of the water film on the
side wall, the expansion speed of the groove size was slowed down to different degrees.
References
[1] Mann B S, Arya V 2002 An experimental study to corelate water jet impingement erosion
resistance and properties of metallic materials and coatings [J]. Wear 253(5) 650-661
[2] Briscoe B J, Pickles M J, Julian K S, et al. 1997 Erosion of polymer-particle composite
coatings by liquid water jets [J]. Wear 203: 88-97
[3] Hancox N L and Brunton J H 1966 The erosion of solids by the repeated impact of liquid
drops [J]. Philosophical Transactions of the Royal Society of London, Series A 260 (1110)
121-139
[4] Seleznev L I, Ryzhenkov V A and Mednikov A F 2010 Phenomenology of erosion wear of
constructional steels and alloys by liquid particles [J]. Thermal engineering , 57(9) 741-745
[5] Mahdipoor M S, Tarasi F, Moreau C, et al. 2015 HVOF sprayed coatings of nano-
agglomerated tungsten-carbide/cobalt powders for water droplet erosion application [J].
Wear 330 38-347
[6] Thomas G P and Brunton J H 1970 Drog impingement erosion of metals [J]. Proceedings of
the Royal Society of London, Series A 14 (1519) 49-565
[7] Kirols H S, Mahdipoor M S, Kevorkov D, et al. 2016 Energy based approach for
understanding water droplet erosion [J]. Materials & Design 04 6-86
Experimental Investigation of the Water Erosion Resistance of Turbine Blade Materials at Different Impact Angle
227