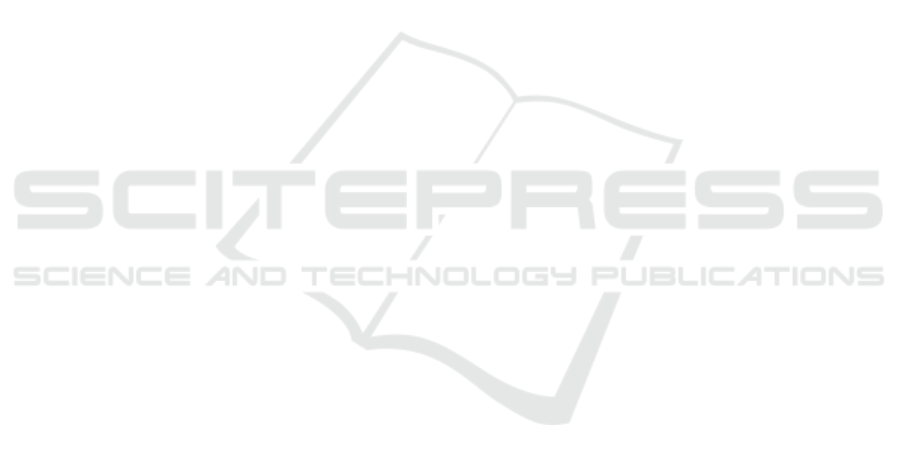
Parametric Modeling of Single-stage Double-suction
Centrifugal Pump Housing
L J Du
1
, Y Y Wang
2
, C H Li
2
, J Liu
2
, X R Chu
1, *
and J Gao
1
1
School of Mechanical, Electrical&Information Engineering, Shandong University,
Weihai, Weihai 264209, Shandong, China
2
Shandong Shuanglun Co., Ltd., Weihai 264203, China
Corresponding author and e-mail: X R Chu, xrchu@sdu.edu.cn
Abstract. In this work, a GS single-stage double-suction centrifugal pump is used to study
the method of three dimensional parameterize modeling. Based on the development of the
centrifugal pump shell template, when the thickness changes, it is unnecessary to rebuild the
whole model manually, the pump shell can be rebuilt rapidly by the equation which shortens
the product design and development cycles. Based on the developed model, the strength of
the pump shell under the design conditions was studied through numerical simulation and the
optimized shell thickness was obtained, which saves materials and reduces design cost.
1. Introduction
The single-stage double-suction centrifugal pump adopts a horizontal mid-open type structure and
it’s easy to maintain. It also has the advantages of small NPSH, large flow, and convenient
replacement of the shaft sleeve. Therefore, the single-stage double-suction centrifugal pump is the
most widely used pump in the industry. The wall thickness of centrifugal pump body is usually
designed based on traditional theory and empirical formula. Generally, the thicker the thickness is,
the safer and more durable it is. If the shell strength can meet the requirements, reducing the
thickness of the shell will save a large amount of raw materials. Thereby increasing economic
efficiency and increasing the market competitiveness for enterprises [1]. However, the structure of
single-stage double-suction centrifugal pump housing is complex. When three-dimensional modeling
is carried out, modifying one parameter will lead to reconstruction of the entire model, which is time-
consuming and laborious, and delays the design and development cycle of the product. Therefore, it
is very important to study a parametric modeling method which can quickly modify the wall
thickness and greatly increase work efficiency [2-3].
2. Analysis of single-stage double-suction centrifugal pump shell structure
2.1. Function of centrifugal pump pressure chamber
Centrifugal pump pressure chamber is important fluid flow component located behind the impeller
and is the main part of the pump. The main function of the pressure chamber is as follows [4]:
(1) Collect the liquid from the impeller and transport the liquid to the discharge port or the
impeller inlet of the next stage;
Du, L., Wang, Y., Li, C., Liu, J., Chu, X. and Gao, J.
Parametric Modeling of Single-stage Double-suction Centrifugal Pump Housing.
In Proceedings of the International Workshop on Materials, Chemistry and Engineering (IWMCE 2018), pages 243-249
ISBN: 978-989-758-346-9
Copyright © 2018 by SCITEPRESS – Science and Technology Publications, Lda. All rights reserved
243