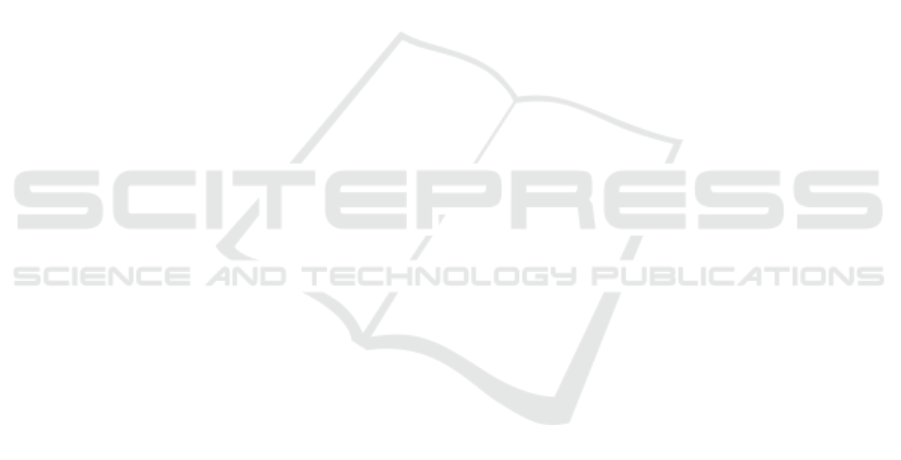
The calculated values are in the same order of magnitude as the experimental values. Yan et al.[10]
preparaed high strength composite silica aerogel which have a compressive modulus of 82.37 MPa.
Tang et al.[11] used disocyanate modification, and the high strength modified aerogels with elastic
modulus of 116.7MPa were obtained. Katti et al.[12] added an isocyanate in SiO
2
sol ,and aerogel
achieved the elastic modulus of 129 ± 8 MPa.
4. Concluctions
The atomic scale model of polymer cross-linked aerogel was constructed by molecular dynamics, and
the process of atomic self-assembly was simulated. The polymer chains coat on the surface of
nanoparticles, and link with each others to form the reticular skeleton structure.
All equilibrated systems are amorphous structures.The solid skeletons gradually become thicker
and the size of nanometer holes decrease with increasing density. The simulation results of
mechanical properties and experimental values are in the same order of magnitude. The elastic
modulus increase from 85.39 to 213.94MPa as density changes from 0.236 to 0.521 g/cm
3
.
References
[1] Aegerter M A, Leventis N and Koebel M M Aerogels Handbook
[2] Yang H L, Cao E X, Wu C C and et al. 2011 Advances in Studies on Polymer Modified Silica
Aerogels Materials Review 25(21) 13-18
[3] Zhang G, Dass A, Rawashdeh A M M and et al. 2004 Isocyanate-crosslinked silica aerogel
monoliths: preparation and characterization Journal of Non-Crystalline Solids 350(8) 152-
164
[4] Xiong G, Chen X H, Wu W J and et al. 2010 Research Progress of Flexible Silica Aerogels
Bulletin of the Chinese Ceramic Society 29(5) 1079-1085
[5] Kieffer J and Angell C A 1988 Generation of fractal structures by negative pressure rupturing
of SiO2, glass Journal of Non-Crystalline Solids 106(1–3) 336-342
[6] Bhattacharya S and Kieffer J 2008 Molecular Dynamics Simulation Study of Growth
Regimes during Polycondensation of Silicic Acid: from Silica Nanoparticles to Porous
Gels Journal of Physical Chemistry C 112(6) 1764-1771
[7] Murillo J S R, Bachlechner M E, Campo F A and et al. 2010 Structure and mechanical
propertiesof silica aerogels and xerogels modeled by molecular dynamics simulation
Journal of Non-Crystalline Solids 356(25–27) 1325-1331
[8] Liu Q, Lu Z X, Yang Z Y and et al. 2014 Multi-Scale Simulation on Mechanical Properties of
Silica Aerogel Powder Aerospace Materials & Technology 01:33-36
[9] Yang J and Li S K 2009 Research on the dynamic mechanical property and failure mechanism
of glass fiber reinforced aerogel Chinese Journal of Materials Research 23(5) 524-528
[10] Yan P, Zhou B and et al. 2014 Mechanical Property of Silica Aerogels Reinforced with
Isocyanate Atomic Energy Science and Technology 48(06) 1100-1105
[11] Tang H Y, Shen J, Yan P and et al. 2014 Mechanical properties strengthening of silica aerogels
New Chemical Materials 42(03) 88-91
[12] Katti Atul, Shimpi N, Roy S and et al. 2006 Chemical, Physical, and Mechanical
Characterization of Isocyanate Cross-linked Amine-Modified Silica Aerogels Chemistry of
Materials 18(2)
IWMCE 2018 - International Workshop on Materials, Chemistry and Engineering
290