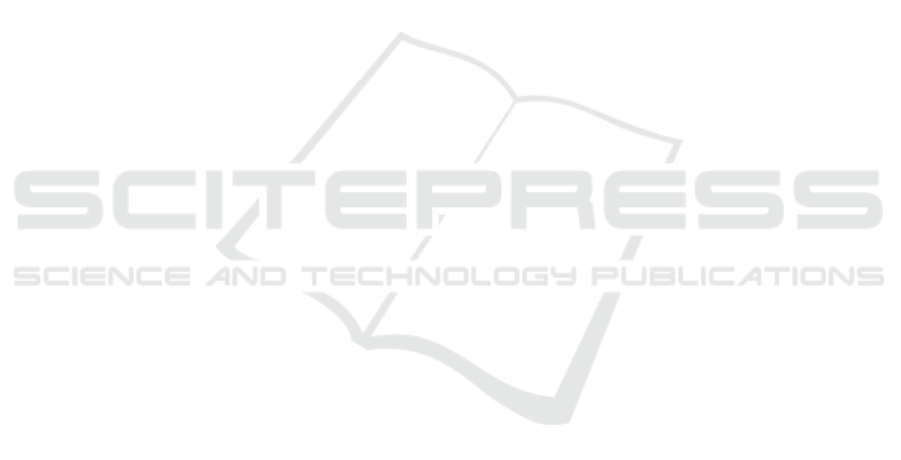
Preparation of Co-conjugate Microporous Polymer Magnetic
Tubular Composites and Application in Removal of
Phosphate Ions
S Li, Z L Hu, Z Q Zhu, H X Sun and A Li
*
College of Petrochemical Engineering, Lanzhou University of Technology, Lanzhou,
China
Corresponding author and e-mail: A Li, lian2010@lut.cn
Abstract. On the basis of synthesizing tubular conjugated microporous polymer, Co
nanoparticles were synthesized in situ on the surface and inside of the tube for the removal of
phosphate ions in water. Under the conditions of 24 hours of adsorption, the removal rate of
an aqueous solution containing 100 mg L
-1
of phosphate ion can reach 82.77%, and the
requirement for separating contaminants can be achieved by applying a magnetic field. It is
proved that the composite material has a good effect of purifying phosphorus-contaminated
water sources.
1. Introduction
Since the beginning of the 21st century, with the advancement of science and technology, the
pollution of water by many organic pollutants has gradually increased, such as the presence of
phosphorus in pesticides, the pollution of aromatic raw materials in industrial production, and so on.
Due to the richness of phosphorus, the enrichment of water bodies and lakes is still called an
important environmental issue [1-4]. The reduction of phosphorus emissions and the reduction of the
impact of these pollutions on water have also become a hot research direction for scientists today.
People have proposed numerous solutions to the above problems. Among the numerous solutions,
the adsorption method is widely used due to its unique mechanism [5-6]. In addition, the adsorption
method has many advantages such as high efficiency, safety, economy, and simple operation. Finding
stable and efficient adsorbents becomes the key to the application of adsorption methods. The
characteristics of the adsorption method determine that the adsorbent should have a high specific
surface area, excellent stability, and can be recycled and used. The porous material has a large
specific surface area, and its unique pore structure makes it widely used in the field of adsorption
[7-10].
Organic porous materials have a series of advantages. Due to its unique pore structure, high
specific surface area, π-π-conjugated chemical structure, ultra-high thermal and chemical stability,
and simple synthesis methods, conjugated microporous polymers are A series of adsorption
experiments have been greatly developed [11-13]. In 2015, our project was combined into a unique
tubular and porous structure of conjugated microporous polymer [14]. Based on this, this chapter
uses tubular conjugated microporous polymer as the carrier to load Co nanoparticles into it. In the
302
Li, S., Hu, Z., Zhu, Z., Sun, H. and Li, A.
Preparation of Co-conjugate Microporous Polymer Magnetic Tubular Composites and Application in Removal of Phosphate Ions.
In Proceedings of the International Workshop on Materials, Chemistry and Engineering (IWMCE 2018), pages 302-306
ISBN: 978-989-758-346-9
Copyright © 2018 by SCITEPRESS – Science and Technology Publications, Lda. All rights reserved