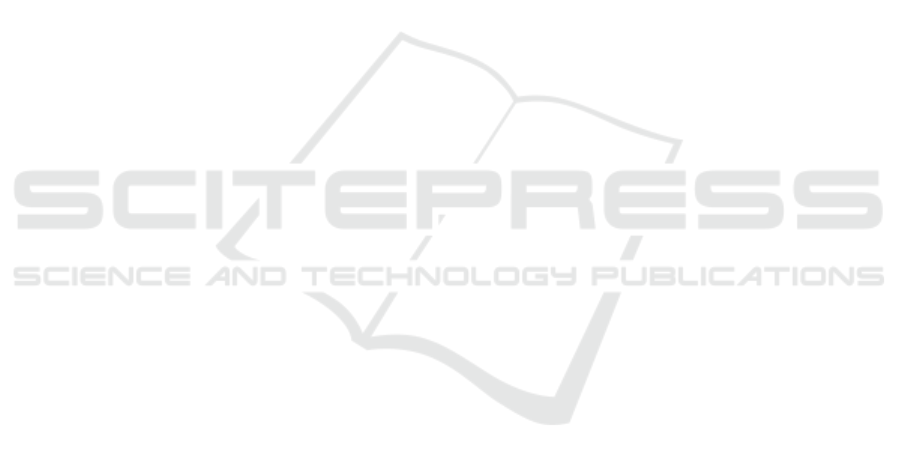
discrete layering and layer by layer addition, which can avoid the waste of materials in the "material
reduction" process, and do not need a die, so it can realize the rapid and full dense forming of high
performance complex components [3].
The composition, phases and the phase transition of alloy steels are complex, and the temperature
changing cycle in the process of laser direct deposition was restricted. It is necessary to study the
post-heat treatment for the LDD alloy steels to further regulate stress and microstructure to obtain
high-performance components. The study on the hot isostatic pressing (HIP) and post heat treatment
of LDD titanium alloys and superalloys showed that HIP with the heat treatment afterwards process
was superior to the direct heat treatment process by obtaining the same microstructure [4-5].G.A.
Ravi et.al. HIPped the LDD SC420 stainless steel also increased elongation from 2-3% for the
as-deposited condition to 9% for the HIPped specimen [6]. Xx He et. al. studied the effects of HIP
and HT post-process of IN718 superalloys in which the UTS increased 60-210MPa compared with
direct heat treatment without HIP, and the elongation increased 60%[7]. The specific influencing
factors for the improvement in elongation are not completely clear. In this paper, the effects of HIP
and related heat treatments afterwards on the microstructure and properties of LDD 12CrNi2 alloy
steels for emergency diesel generator crankshaft were studied.
2. Experimental procedure
Gas-atomized 12CrNi2 alloy steel powder was used in this study with the particles size varied from
50-150μm.The composition of the as-received 12CrNi2 powder was shown in Table 1. Laserline
LDF3000-60 system with Ar gas protecting box was used to fabricate the specimens
(100mm×30mm×20mm). The as-deposited 12CrNi2 samples were treated using hot isostatic press
(ABB company QIH-15 HIP tester in Southwest Jiaotong Univ.) under argon gas at 820-880°C and a
pressure of 120MPa for 2-4h with cooling rate 15°C /min. The Heat Treatment(HT) afterward was
860°C solution treatment for 10min and Oil Quenching(OQ) +300°C tempering for 10min and Air
Cooling(AC) (sample size 90mm×9mm×1mm). The samples for microstructure observation were
etched using 4% Nital solution. A Shimadzu-SSX-550 SEM was used to examine the microstructure
evolution of as-deposited and of HIPped and with HT afterwards specimens and the fracture surface
of the tensile test samples. TEM samples were examined a TECNAI G220 transmission electron
microscope. SAD pattern was recorded to identify the phases present in the microstructure. XRD
study was also performed for all the conditions using an X 'Pert Pro MPD-PW3040/60 X
diffractometer with Cu Kαradiation at 40kV and 40mA. Microhardness was tested on a Wilson
Wolpert 401MVD tester with the load of 200g and loading time 10s.Tensile tests were performed on
sample prepared as the standard (gauge length of 15±1mm, total length of 90mm and thickness of
1.0±0.1mm).The tests were carried out in a Shimadzu AG-X100KN at a strain rate 6.7×10-4/s.
3. Results and discussion
3.1. X-ray diffraction analysis and microstructure
Figure 1 shows the results of XRD analysis of the as-deposited, HIPped and HIPped with post HT
samples. The alpha phase was identified without orientation. Figure 2 shows the optical and SEM
micrographs of the as-deposited and of HIPped and HIPped with post HT samples of 12CrNi2.
According to the XRD phase analysis above and microstructure observation below, it can be seen
that the optical morphology of the as-deposited sample contained mainly ferrite (white) and granular
bainite (see Figure 2a) [8-9]. The average size of the ferrite in the microstructure of as-deposited
sample was about 3μm-5μm. Carbon concentrated was observed alone grain boundary of a few
ferrite (see Figure 2g). In some as-deposited samples a few pores with size of 300μm-400μm was
found which lead to lower relative density of 98.3% compared with the wrought with density of 7.85
g/cm3. HIPping was performed at 860°C which higher than the measured AC3 of LDD 12CrNi2 and
IWMCE 2018 - International Workshop on Materials, Chemistry and Engineering
346