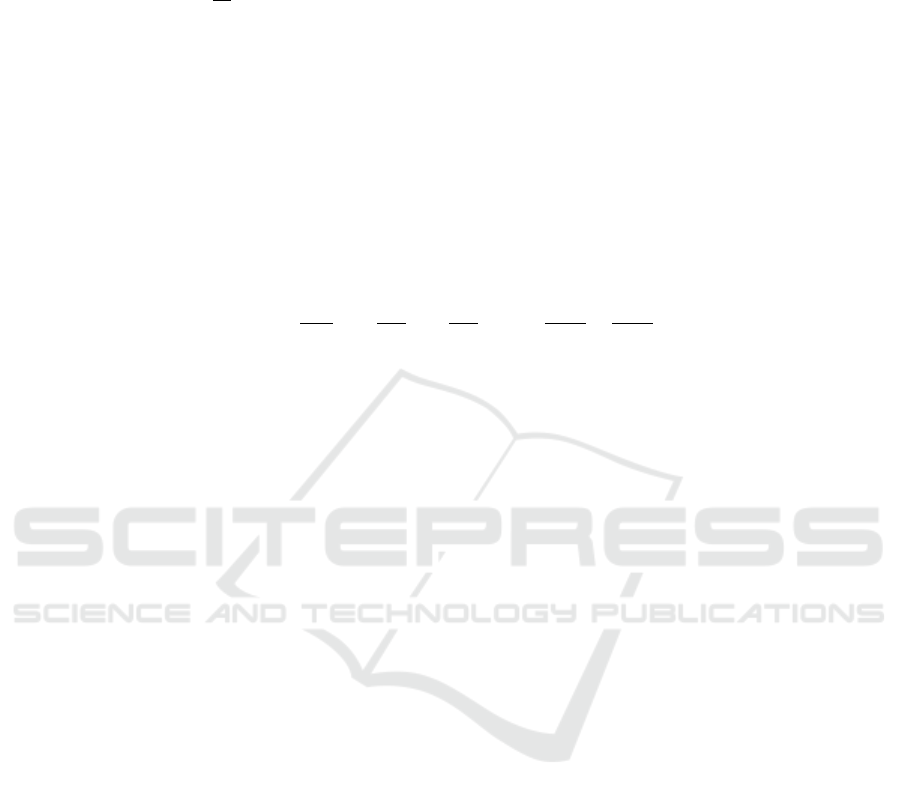
2.2. Mathematical equations
The energy equation is referred to formula (2) by using fluent software[11].
( ) ( E+ ) [ ( )]
t
eff
eff j j h
E v T h J v S
(2)
In the formula: t is time, s; Rho is density, kg/m
3
; E is energy, J; V is fluid velocity, m/s; P is
pressure, Pa; Lambda eff is the effective thermal conductivity coefficient, W/(m•K); T is temperature,
K; H
j
is the enthalpy of component j, j; the diffusion flux is j, mol/(m
2
•s), the effective viscous
dissipation coefficient, and the stress tension, Pa. The right side of the equation represents the energy
transfer caused by heat conduction, component diffusion and viscous dissipation. Sh contains the
chemical reaction (absorption) heat and other forms of defined volume heat sources. In this
experiment for cylindrical reactor, the axisymmetric physical parameters according to the center, so
can choose 2 d cylindrical coordinate to establish mathematical model of the reactor, the heat in the
form of differential equations can be written which referred to formula (3).
22
22
( ) ( )
h
t t t t t
c u v S
x y x y
(3)
In the formula: ρ is density, kg/m
3
; C is the specific heat capacity, J·kg/K; T is temperature, K; τ is
time, s; x and y are two directions of two dimensional space; U is moving in the x direction, m/s; V is
the velocity of the material in the y direction, m/s; λ is the thermal conductivity, W/(m•K),S
h
is the
heat source generated by the chemical reaction. In this paper, the position of the heat source is the
liquid surface, and its energy is characterized by the heat flux density generated by the chemical
reaction.
2.3. Basic physical parameters
In this experiment, the basic physical parameters of mixed liquid in the reactor are simplified[12].
Density and viscosity are calculated by simple rule of mixtures, this is shown in the following
formula (4).
11
;
nn
i i i i
ii
mm
(4)
In the formula: mi is the mass fraction of the liquid of each component, ρi is the density of
Components of the i, and ρ is the density of mixing liquid, kg /m3; Ui is the viscosity of component I,
u is the viscosity of the mixed liquid, Pa•s.
In the reduction reactor, the main component of liquid is the raw material of liquid magnesium,
magnesium chloride and titanium particles produced by the reduction reaction, under the condition of
high temperature, the thermal conductivity of magnesium chloride (5W/(m•K)) and the thermal
conductivity of the titanium particles(8W/(m•K) ) are obviously lower than the thermal conductivity
of the liquid magnesium(97.33W/(m•K)). Therefore, the thermal conductivity of liquid magnesium is
used to represent the thermal conductivity of the liquid in the reactor.
3. Setting of heat source
3.1. Heat dissipation mechanism
Reactor cooling is mainly through the wall of the gas convection and radiation heat dissipation of the
reaction exhaust[13]. Therefore, the unit wall heat dissipation unit time is the sum of convective heat
transfer and radiation heat transfer power, the relationship is referred to formula (5).
Simulation of Temperature Field of Sponge Titanium Prepared by Magnesium Thermal Reduction Process
393