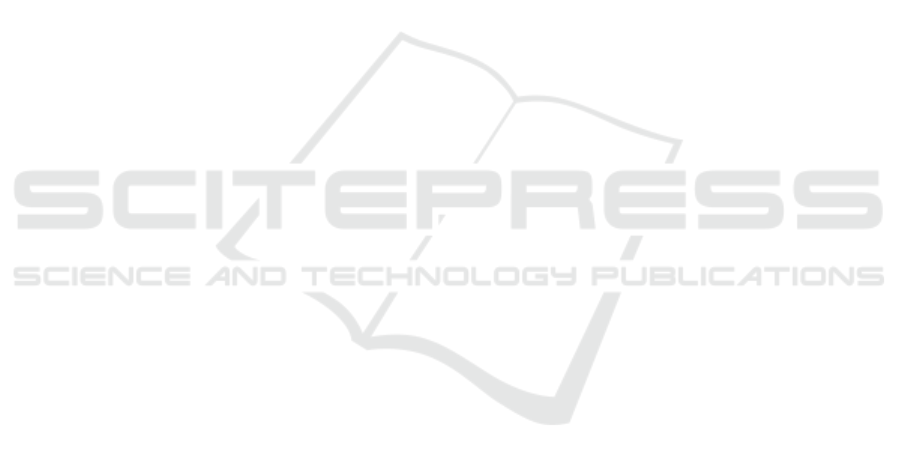
inert anti- caking agent and its amount should be selected appropriately, so as to optimize the PCM
thermal storage properties.
KAl (SO
4
)
2
12H
2
O-MgSO
4
7H
2
O mixed hydrated inorganic salt system is a group of thermal
storage material with advantages of high energy density, cheap and easily to conduct preparation. As
to the mass ratio of KAl(SO
4
)
2
12H
2
O to MgSO
4
7H
2
O being 2 to 8, it has the characteristics of high
latent heat of phase change, good thermal conductivity, low degree of super-cooling (about 1 °C ),
and no segregation [6]. The phase change temperature of the material is stable at about 48 °C after
several cycles of cooling and heating, which is a good hydrated salt phase change heat storage
material suitable for low temperature solar air - drying system. However, this material suffers from
agglomerate when circulated to about 20 times, and the dense agglomeration increases gradually with
the cyclic number.
The aim of the present paper is to prevent the material with the mass ratio of KAl(SO
4
)
2
12H
2
O to
MgSO
4
7H
2
O being 2 to 8 from agglomeration, alumina powder is added as an anti- caking agent to
perform the work.
2. Preparation and basic test
2.1. Experimental material
The main chemicals are: KAl (SO
4
)
2
12H
2
O, Zhengzhou Paiey Chemical Reagent, Zhengzhou, purity
of 99.5%; MgSO
4
7H
2
O, Tianli Chemical Reagent Co. Ltd., Tianjin, purity of 99%; Al
2
O
3
powder,
Xi’an Chemical Reagent, Xi’an, purity of 99.5%.
2.2. Laboratory equipment
The experimental equipments include: HCT-1 differential scanning calorimetry balance, DZF-6030
vacuum oven; DF-101S constant temperature heater with magnetic stirrer; a thermometer (apuhua
TM-902C, -50 °C ~ 1300 °C , accuracy 0.1 °C ); JJ124BC electronic balance (Max = 120g, Min = 20d,
d = 0.1mg).
2.3. Characteristics of thermal properties of MgSO
4
7H
2
O and KAl (SO
4
)
2
12H
2
O components
The experimental procedure for DTA and step-cooling curve tests are described as those in [6].
As to step-cooling curve, temperature data is recorded every 10s for once; step cooling curve is
drawn after the cooling temperature tests. While for DTA test, the temperature ranges from room
temperature to 150°C with heating rate of 1 °C / min.
While the DTA curve and the step cooling curve of KAl (SO
4
)
2
12H
2
O are shown in [6]. The
DTA curve shows a single endothermic peak at 75.7 °C , which exhibits a large latent heat of
882.58kJ/kg.
The step cooling curve of KAl (SO
4
)
2
12H
2
O represents that the crystallization of the molten of
KAl (SO
4
)
2
12H
2
O begins at 63.0°C followed by a temperature rising to 73.4°C , which is because of
the releasing of latent heat as well, and implies a relative bigger super-cooling of 10.4°C .
The experimental DTA curve and step cooling curve for MgSO
4
7H
2
O are shown in [7]
respectively.
From DTA curve of MgSO
4
7H
2
O, it can be seen that MgSO
4
7H
2
O exhibits three endothermic
peaks during heating process at 46.1 °C , 81.4°C and 106.4 °C , respectively. The total phase change
latent heat is 811.97kJ/kg, which is phase change material with high latent heat.
The step cooling curve of MgSO
4
7H
2
O shows that the molten MgSO
4
7H
2
O begins to crystallize
at 51.8 °C followed by a temperature rising to 60.4°C , which is owing to the releasing of latent heat,
and indicates a super-cooling of 8.6 °C .
IWMCE 2018 - International Workshop on Materials, Chemistry and Engineering
404