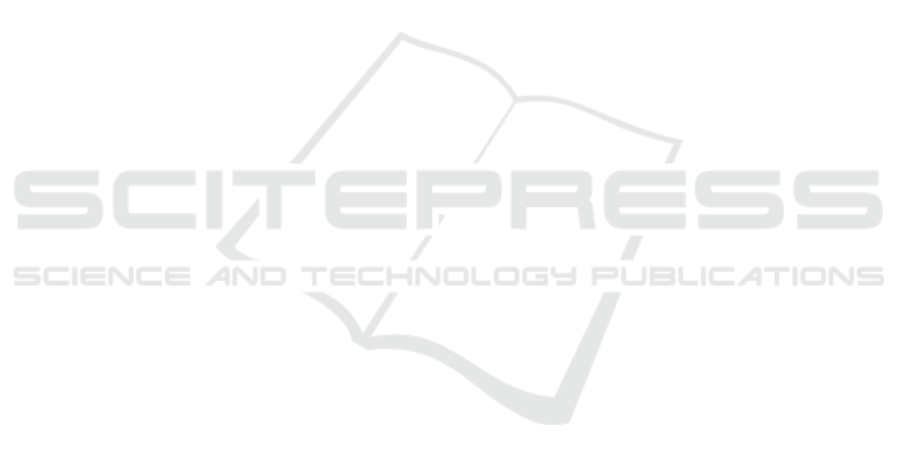
To explore the effect of LiH on the synthesis of the α-AlH
3
/LiCl composite, Figure 2 shows the
curves of dehydriding kinetics of the as-milled α-AlH
3
composite at various temperatures and
different time intervals. As can be seen in Figure 2 that the rate of dehydrogenation accelerated as the
temperature rose to 140°C. Additionally, from the curves for dehydrogenation reaction, it can be
conjectured that LiH has remarkable effect on the dehydrogenation reaction of the α-AlH
3
/LiCl nano-
composite. When the de-hydriding temperature is fixed at 80°C for 5,000 s, it can be seen from the
Figure 2(a) that the hydrogen desorption content of as-milled product reached merely 4.84 and 6.95
wt% respectively, indicating that the dehydriding reaction was still not complete under this condition.
Compared with the AlH
3
/LiCl composite without adding LiH, AlH
3
has a significant advantage on
dehydriding property with the same hydrogen content at 80 °C for 3,736 s. Although the dehydriding
curve exhibited an undesirable property, the as-milled product still have an advantage in de-hydriding
properties compared with the much lower hydrogen content of 1.9 wt% derived from the as-milled
AlH
3
which fully decomposed from room temperature to 200°C [14]. Furthermore, the value
described above, was higher than the 0.48 wt% hydrogen content of crude α-AlH
3
measured by
Graetz. et. al.[3, 6, 7]. By increasing the reaction temperature to 120°C for 3,000 s, the hydrogen
content of α-AlH
3
/LiH composite increased rapidly to 9.89 wt%, suggesting that almost all the AlH
3
decomposed, much more than at lower temperature. Even dopped with LiH, it was demonstrated by
Sandrock that only 4 wt % H
2
can be obtained from the AlH
3
/LiH composite in the the first four
hours [18]. Furthermore, the same hydrogen content could be obtained by heating the reaction
mixture at 140°C for the 1,140s, which implied that the dehydrogenation rate was clearly accelerated
by increasing the temperature. It is obvious that the AlH
3
added with LiH has a more desirable
dehydriding dynamics. Consequently, the LiH probably come into play with the decomposition
kinetics of α-AlH
3
and can accelerate the de-hydriding reaction of α-AlH
3
. Although fresh
synthesized nanoscale α-AlH
3
has an advanced dehydrogenation property, it was reported by Graetz
that fully decomposed time at 138°C can be achieved even within 1,800s [12]. Therefore, it can be
concluded that the α-AlH
3
nano-composite doped with LiH exhibits an excellent advantage in de-
hydriding property.
3.3. The de-hydriding kinetics of the ɑ-AlH
3
/LiCl nano-composite
In order to gain an deep insight into the de-hydriding process of the α-AlH
3
/LiCl/LiH nano-
composite, further supporting evidence can be obtained from the DSC curves in Figure 3. Figure 3(a)
shows DSC curves of as-milled α-AlH
3
composite added with LiH at several heating rates. It is
obvious that the desorption curves of the composite added with LiH still have a similar peaks with
that of un-doped composite. The whole DSC curves contain only one endothermic peak at a elevated
temperature of 40-240 °C. This endothermic peak derives from α-AlH
3
decomposition is consistent
with Liu report [2]. It was found that the endothermic peak between 80 and 190 °C is assigned to the
de-hydriding reaction of the α phase [2]. This indicates that no new phase was formed in the product.
Namely, α-AlH
3
can not react with LiH during the de-hydriding process. Based on the above non-
isothermal analysis, the corresponding de-hydriding temperature of α-AlH
3
is remarkably reduced
with the LiH added into the composite. Thus, it can be deduced that the LiH have some effects on the
decomposition kinetics of α-AlH
3.
To determinate the value of apparent activation energies (Ea) for
this dehydriding process, the desorption kinetics of the α-AlH
3
/LiCl nano-composite was studied by
using the Kissinger’s method. Moreover, the relationship among the activation energy (Ea), the
heating rate (c), and the peak temperature of de-hydriding (T
P
) in the DSC curve can be formulated
by following Kissinger’s equation:
Ln (c/T
) = - (E
a
/RT
p
) + A (1)
Figure 3(b) shows the activation energy of the de-hydriding reaction based on parameters
obtained from DSC measurements. The apparent activation energy for the hydrogen desorption of α-
IWMCE 2018 - International Workshop on Materials, Chemistry and Engineering
542