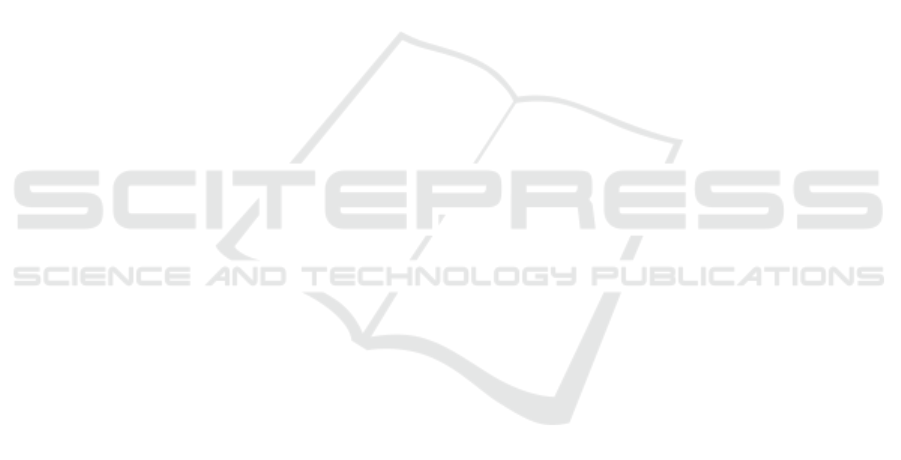
during cladding, the clad material undergoes consecutive thermal cycles which could contribute to
progressive modification of its microstructure and properties [2].
Moreover, LC is now being a viable alternative to improve the quality of surface properties of
outlayer of rolls. There are considerable investigations on laser surface modification technique used
in HSS processing. Zhang et al. [3] reported that M2 HSS samples were fabricated by laser additive
manufacturing (LAM) and the microstructures of deposited samples were composed of
supersaturated martensite, retained austenite and M
2
C-type carbides. Wear resistances of all LAM
samples showed an adhesive wear mechanism, and M2 HSS had a lower friction coefficient and a
larger wear volume loss. Investigation of Liu and Leong [4] showed the microstructure
characteristics of M2 HSS parts produced by selective laser melting (LSM). The observed
microstructure from SEM and FIB was characterised by a continuous and homogeneous network of
dendrites within two different phases. The research results gave a thorough insights on the rapid
solidification phenomenon in SLM. Colaco et al. [5] showed that laser surface melting almost
completely eliminated the residual porosity and dissolved large brittle carbides that are present in the
as-sintered AISI M42 HSS samples, leading to an extremely fine and homogeneous microstructure.
Candel et al. [6] showed that AISI M2 tool steel coatings on medium carbon AISI 1045 steel
substrate have been manufactured and after Laser Cladding (LC) processing it has been applied a
tempering heat treatment to reduce the amount of retained austenite and to precipitate secondary
carbides. They found the microstructure is extremely fine and complex, with eutectic transformations
and MC, M2C and M6C precipitation. Therefore, after the laser coating is necessary to use post heat
treatments.
However, the above mentioned research is surface modification on conventionally fabricated HSS
steels and surface deposition on structure steels. To the best of our knowledge, there are many kinds
of material for core part of rolls used in steel making process. A preliminary investigation on
fabricating HSS on core materials of hot roll using LC technique is essential for promoting it to be
used in hot roll manufacturing. In the present study, LC treatment on nodular cast iron was carried to
investigate the effect of LC parameters. Microstructure, phases, and microhardness of all the LC
specimens were analyzed. Dry sliding wear were carried out on them and wear mechanisms were
studied.
2. Experimental procedure
Nominal chemical composition of gas atomized M2 HSS powder (−200/+325 mesh), manufactured
by AVIC Beijing Institute of aeronautical materials, is 0.996C- 6.32W- 5.03Mo- 3.93Cr- 1.78V-
0.193Mn- 0.312Si- 0.30Co- 0.330Ni- 0.252Cu- 0.020S- 0.031P (wt %). As-received nodular cast iron
substrate was cut into size of 20mm×15mm×10mm. Surface of the specimen was machined and
polished to remove the oxide scales, and then rinsed with acetone and deionized water.
LC treatment was performed using a 400W pulse Nd:YAG laser with a wavelength of 1064nm
(manufactured by Wuhan Tuanjie Laser Technology Co., LTD., Wuhan, Hubei, China). During the
treatment, a layer of powder with a controllable thickness between 20-100 μm was pre-placed. Argon
shielding gas was used during LC processing to avoid oxidation and contamination. A NUM 1060
CNC system was used to control the movement of a table to fabricate the desired specimen,
according to the sliced CAD data.
Extensive single-track laser cladding process was conducted to get optimized laser processing
parameters. Laser cladding conditions were laser power 18-44 W, scanning speed 2, 2.5 and 3 mm/s,
and beam diameter 0.32, 0.40 and 0.48 mm. Multi-track and multi-layer processing parameters were
as follows: laser power 23.5W, scanning speed 2.5mm/s, the amount of distance out of laser spot +14
mm, diameter of laser beam 0.48 mm, the thickness of coating 0.2 mm, and overlap ratio 50%.
After laser cladding treatment, specimens were sectioned, mounted, ground, polished and etched
with aqua regia. The cross-sectioned microstructure of the specimens were examined using an optical
The Microstructure Evolution and Wear Resistance of Laser Cladding M2 High Speed Steel on Nodular Cast Iron
585