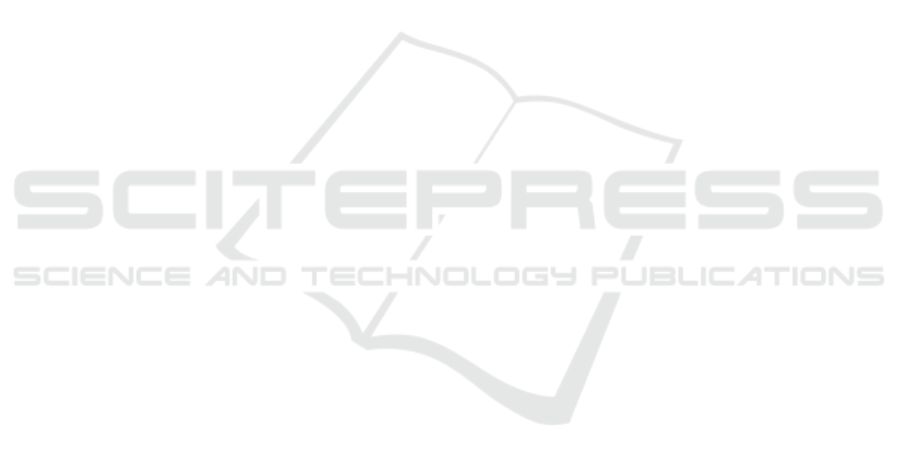
Feasibility Study of Carbon Fiber Ceramic Matrix
Composites Used in Mechanical Seal Friction Pairs
J G Wang, Z P Guo
*
and A N Zhang
School of Mechanical Engineering, Xi’an Shiyou University, Xi’an,
Shaanxi(710065), China
Corresponding author and e-mail: Z P Guo, 310625000@qq.com
Abstract. The choice of mechanical seal friction material has great influence on the sealing
performance. As a new composite material, carbon fiber ceramic matrix composites have
excellent corrosion resistance, high mechanical strength, good heat resistance and heat
transfer performance, is the good choice of mechanical seal matching material. In the paper,
the temperature field and leakage value are simulated by computer when carbon fiber ceramic
matrix composites are applied to the friction pair. And the simulation results are verified by
experiments. Studies have shown that when carbon fiber ceramic matrix composites are used
in mechanical seal friction pairs, the sealing performance is significantly improved, including
reducing temperature rise, leakage and wear.
1. Introduction
The material of the mechanical seal friction pair has a great influence on the sealing effect [1].
Carbon fiber ceramic matrix composites is a new type of composite material. It has low density, good
thermal conductivity and corrosion resistance. The good thermal conductivity significantly reduces
the temperature rise of the sealed end face, prevents the thermal damage of the sealed end face, and is
advantageous to the stability of the liquid film between the friction pairs, thereby avoiding the sealing
failure. Smaller density increasess follow-up to moving parts, and good wear resistance can extend
the life of the seal ring. In summary, there are many benefits to using this material for sealing friction
pairs. In this paper, ANSYS software is used to study the temperature field between the static and
dynamic rings of the friction face. First, the temperature field under different materials is studied;
then, the speed and pressure of the friction pair are changed respectively to obtain the corresponding
temperature field; finally, the temperature of several points is measured by a mechanical seal test
bench to verify the accuracy of the numerical simulation.
2. CFD model
This article chooses SG04U type mechanical seal structure. Figure 1 shows the structure. And the
seal area ratio is 1.2952. The seal spring specific pressure is 0.15 MPa. The axial thickness of the
moving ring is 24mm. The axial thickness of the stationary ring is 30mm. The medium is 20#
mechanical oil. The thickness of the liquid film is 4μm. And the flow state is laminar [2-3].
638
Wang, J., Guo, Z. and Zhang, A.
Feasibility Study of Carbon Fiber Ceramic Matrix Composites Used in Mechanical Seal Friction Pairs.
In Proceedings of the International Workshop on Materials, Chemistry and Engineering (IWMCE 2018), pages 638-643
ISBN: 978-989-758-346-9
Copyright © 2018 by SCITEPRESS – Science and Technology Publications, Lda. All rights reserved