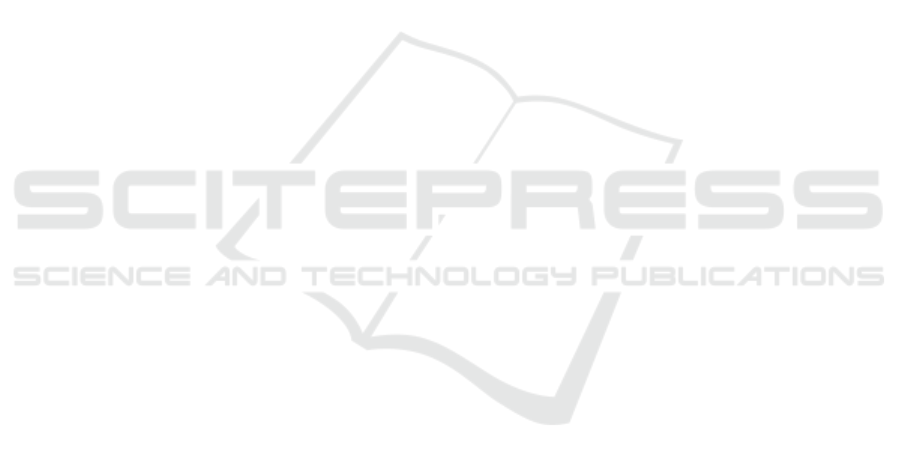
the failure of the used sealing ring is due to fatigue aging. During the process of service life, the
sealing ring structure change and properties degradation due to the applied stress, and the gas
permeation accelerates the fatigue aging process.
5. Conclusions
1) The reason of sealing ring failure is fatigue aging during the long-term service life.
2) The gas permeation leads to the destruction of the network structure, and accelerating the aging
process.
3) This type of sealing ring is not suitable for using in acidic gas fields, high-grade sealing
materials should be selected. for preventing the sealing ring failure used in theacidic gas fields, the
most important strategies is evaluations and detections before using.
Acknowledgement
The project was supported by the National Natural Science Foundation of China (Grant No.
51304236).
References
[1] Li H B, Y M L, Qi D T, Ding N, Cai X H, Zhang S H, Li Q, Zhang X M and Deng J L 2012
Failure analysis of steel wire reinforced thermoplastics composite pipe J. Engineering
Failure Analysis 20 88-96
[2] Qi D T, Yan M L, Ding N, Cai X H, Li H B and Zhang S H 2010 The 7th international MERL
Oilfield Engineering with Polymers Conference, London, UK
[3] Bai Y, Xu F and Cheng P 2012 Investigation on the Mechanical Properties of the Reinforced
Thermoplastic Pipe (RTP) Under Internal Pressure [C]. The Twenty-second International
Offshore and Polar Engineering Conference, June 17-22, Rhodes, Greece: International
Society of Offshore and Polar Engineers
[4] Drake K and Callaway R 2014 New polymeric materials development for extreme
environments [C]. OTC-25304, Offshore Technology Conference, Houston, 5-8
[5] Yamabe J and Nishimura S 2013 Failure behavior of rubber O-ring under cyclic exposure to
high-pressure hydrogen gas J. Engineering Failure Analysis 5 193-205
[6] Stevenson A 1983 A fracture mechanics study of the fatigue of rubber in compression Int. J.
Fracture 23 47-59
[7] Mars W V 2002 Cracking energy density as a predictor of fatigue life under multiaxial
conditions J. Rubber Chemistry and Technology 7 5 1-17
[8] Ayoub G, Naït-Abdelaziz M, Zaïri F, Gloaguen J M and Charrier P 2012 Fatigue life
prediction of rubber-like materials under multiaxial loading using a continuum damage
mechanics approach: effects of two-blocks loading and R ratio J. Mechanics of materials
52 87-102
[9] Le S V, Marco Y, Calloch S, Doudard S and Charrier P 2010 An energetic criterion for the
fatigue of rubbers: an approach based on a heat build-up protocol and μ-tomography
measurements J. Procedia engineering 2 949-958
[10] Poisson J L, Lacroix F, Méo S, Berton G and Ranganathan N 2011 Biaxial fatigue behavior of
a polychloroprene rubber Int. Jour. Of Fat. 3 1151-1157
[11] Bathias C, Legorju C, Chuming L, Menabeuf L 1996 Fatigue crack growth damage in
elastomeric materials[C]. In: Elastomeric materials ASTM. STP 505-13
[12] Cruanes C, Berton G, Lacroix F, Méo S and Ranganathan N 2014 Study of the fatigue
behavior of the chloroprene rubber for uniaxial tests with infrared method J. Elastomery 18
3-9
Failure Analysis of the Fluorine Rubber Sealing Ring Used in Acidic Gas Fields
657