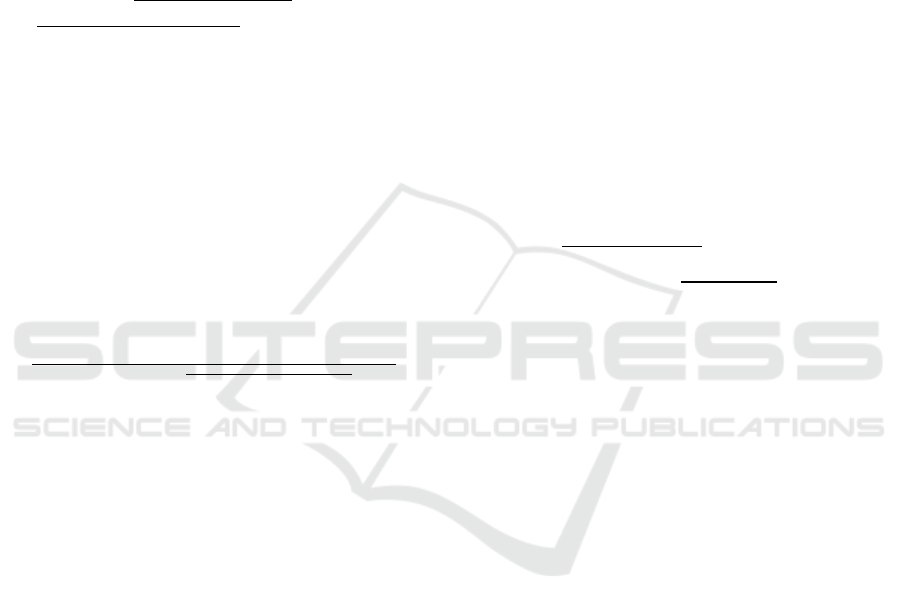
After simplifying, the relation:
(1)
2. Limit point interference constraint
In the process of frame folding, there should be
no interference between the hinge point A of lifting
bar and the limit position point F of auxiliary frame,
and the length of lifting bar should be longer than
the length from point O to point F. The dimension
constraint relation:
(2)
3. Frame interference constraint
After folding, the front and rear frames should
not interfere. As the point K is not the limit position
of the front frame, when the frame reaches the limit
position, the clearance between the point K and the
rear frame is reserved for 120mm.The dimension
constraint relation:
After simplifying, the relation:
(3)
4. The battery interference constraint
Due to the use of hub motor drive technology,
the space of the front and rear frame is mainly
occupied by the battery pack, so the interference of
the battery pack should be considered in the design
of the frame.
The equation of the straight line EF can be get
from the point E(-
,
)and point
F(
,
).
The liner equation:
To ensure that the limit position point P (-520
,180)of the battery pack does not interfere with
the ramp of the auxiliary frame, point P should be
below the right of the linear EF in the coordinate.
The constraint relation can be obtained from the
position relation:
(4)
5. Front and rear frame size constraint
Considering the size of battery pack and folding
mechanism of vehicle size, the outer profile height
of auxiliary frame is preliminarily determined to be
300-500mm. Constraint relation:
and
(5)
The length of the front and rear frame is 400-
600mm.And the constraint relation:
and
(6)
6. Constraint of the lifting bar inclination
Rotation of the rocker plays a major role in
frame folding. In order to ensure that the pressure
angle of the rocker is not too large, its inclination
angle relative to the X-axis of the coordinate system
is set within 10-30°. The constraint relation:
°
and °
(7)
3. MATLAB OPTIMIZE DESIGN
AND MODELING SIMULATION
3.1 Multivariable Optimization
The mathematical model of frame folding
optimization belongs to the problem of single
objective multivariable optimization.
The normalized form[4]:
min F(X)
s.t
AX ≤b
AeqX = beq
C(x) ≤ 0
Ceq(X) = 0
lb≤ X ≤ub
The function fmincon is invoked to solve the
problem. The basic format of the function command
:
[x,fval,exitflag,output]=fmincon(@objfun,x0,A,b
,Aeq,beq,lb,ub,@confun)
By writing the M file of the objective function
and the constraint function, the optimization results
can be obtained by establishing the main program
solution: