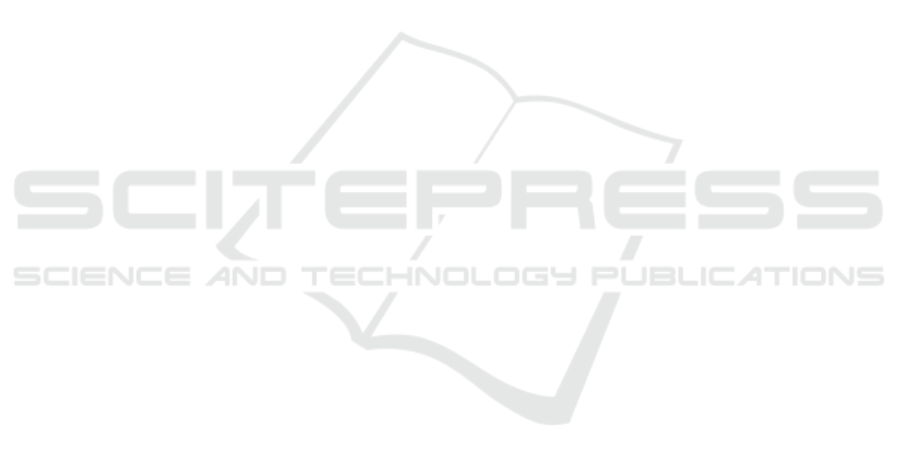
22
1
G
r SO F SO
(7)
(8)
2.4. Discussion
In the field environment, there are interactive effects between different environmental factors. For
example, it is showed that the zinc corrosion rate did not show dependence on temperature in the
presence of carbon dioxide [28]. Similar results were also reported for copper corrosion in the
presence of nitric acid [2]. Moreover, the nitrogen oxides (NO
x
) are also important factors that can
promote the atmospheric corrosion. J. G. Castano [29] summarizes the effect of NO
x
on atmospheric
corrosion of different metals (copper, aluminum, nickel, carbon steel and zinc), but no coincident
conclusion is drawn. Some authors believe to be of little influence [30, 31], some detected it an
inhibitive effect [32, 33], while others consider the effect is dependent on other factors such as
humidity [34, 35], the type of the metal [29], and SO
2
concentrations [20, 29]. With such complex
mechanisms, the interactive effect between different factors is hard to be fully quantified. In this
paper, the effect of SO
2
is included and the interactions between different pollutants are not
considered.
Except from the environmental factors discussed above, carbon dioxide, ozone, solar radiation,
wind, and rain are also important for different materials. For example, carbonation is the major cause
for the failure of concrete structure due to the erosion of carbon dioxide [15]. The corrosion of silver
can be accelerated by the presence of ozone and ultraviolet [36]. Solar radiation, wind, and rain can
influence the deposition rate of chloride and the time of wetness [4]. When materials are subject to
more complex ambient environmental conditions with multiple atmospheric corrosive factors,
interactive effect occurs and the effect of each factor should be analyzed carefully.
3. Effects of environmental factors on marine corrosion
Marine environment contains plenty of corrosive media like seawater temperature, dissolved oxygen,
water velocity, pH, oxidation reduction potential (ORP) and various dissolved salts, so the influence
of marine environment on corrosion is more complex than atmosphere. When components and
structures operate in such a complex marine environment, all kinds of corrosion forms are inevitable.
Marine corrosion can take different forms, for example: general corrosion, pitting corrosion, stress
corrosion cracking, weld corrosion, bimetallic corrosion, filiform corrosion, corrosion fatigue,
fretting corrosion and bacterial corrosion [37-39, 51]. In general marine corrosion, which is the most
common form of corrosion, the wastage is spread over the surface of the materials [40]. Through the
different forms of corrosion, the uniform general corrosion is the type that is considered here.
3.1. Salinity
Seawater is extremely corrosive due to its high salt content. The salinity of seawater generally is 35
ppt and far higher than river water which is only 0.02 ppt. Thus, marine corrosion occurs easily and
accelerates the corrosion rates. But the corrosion rates do not rise all the time with the salinity rising.
Test shows that corrosion rates reach the maximum when the salinity is 32 to 35 ppt, namely the
salinity of natural seawater [45, 49].
This is due to the effect of salinity on the corrosion reaction. On one hand, the transfer speed of
the charge is accelerated with the increase of the salinity of the seawater. So, the corrosion rates
accelerate obviously. On the other side, with the salt concentration increasing, the solubility of
oxygen in the seawater is decreasing so that the corrosion rate will be reduced. When the salinity is
less than the natural sea, the influence of electrical conductivity is dominated. When the salinity
exceeds the natural sea water salinity, the increase of salinity causes the decrease of oxygen content
Atmospheric and Marine Corrosion: Influential Environmental Factors and Models
181