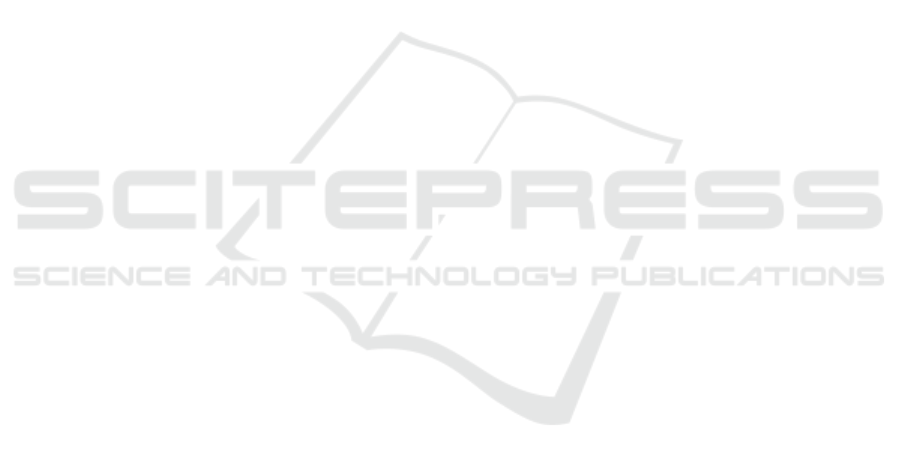
researchers home and abroad previously focused
their studies on alkaline flooding, polymer flooding,
surfactant flooding and combination flooding etc.
Their theoretical research has some merits (Liao and
Tang, 2018; Qu, 2013; Tang et al., 2012; Zhou, 2017;
Chen, 2013; Jin et al., 2005), besides some
technologies proposed were put into field tests. In
No.3 oil production plant of Dagang oilfield in China,
a small-scale field test using viscosity reducer was
implemented. Due to the failure for the small
molecule viscosity reducers to form stable O/W
emulsions under low in-situ shear rate, incremental
oil production was found to be nominal.
Studies show that the key to improving water
drive recovery factor in heavy oil reservoirs is to
enlarge swept volume. Reducing viscosity of heavy
oil and raising viscosity of displacement phase are
effective ways to achieve this. Now that there is no
research conducted home or abroad on heavy oil
water flooding EOR technologies that could reduce
heavy oil viscosity meanwhile raising displacement
phase viscosity under low in-situ shear stress. This
could possibly be achieved by macromolecular
viscosity reducers according to the theory of
molecular design. The synergism could greatly
improve the recovery factor of water flooding in
heavy oil reservoirs. Therefore, macromolecular
viscosity reducer is one of the key technologies to
replace water flooding in the near future. It is of great
significance to water flooding EOR of heavy oil and
has a promising prospect and range of applications.
5 CONCLUSIONS AND
PROPOSALS
Flow improver which has good pour
point-depressing and viscosity-reducing effects for
the waxy crude oil, had been used in Luning,
Zhongluo and Pulin, et al. pipelines and improved
safety and adaptability in operations.
Oil-based viscosity reducer which has good
viscosity reducing effect for heavy oil with low
viscosity, had used to wellbore lifting of low
viscosity heavy oil. While water-based viscosity
reducer which has good viscosity reducing effect on
heavy oil with high viscosity, had used to wellbore
lifting of extra heavy oil.
More research needs to be diverted to and focused
on viscosity reducers for formation drive, including
studies of viscosity reducing mechanisms, evaluation
system and molecular structure design.
REFERENCES
Ahmed, N. S., Nassar, A. M., Nasser, R. M., et al., 2014.
Novel terpolymers as pour point depressants and
viscosity modifiers for Lube oil. Petroleum Science
and Technology, 32(6): 680-687.
Bai, W. H., Zhang, X. Q., Gu, H., et al., 2016. Selection
and pilot test of an oil based viscosity reducer .
Advances in Fine Petrochemicals, 17(6): 32-34.
Barasha, D., Rohit, S., Arnab, M., et al., 2018. Synthesis
and evaluation of oleic acid based polymeric additive
as pour point depressant to improve flow properties of
Indian waxy crude oil. Journal of Petroleum Science
and Engineering, 170: 105-111.
Bi, M. H., 1992. Development and application of CE crude
pour point depressant. Oil-Gas Field Surface
Engineering, 11(4): 44-46.
Cao, D. F., Li, Q. P., 2004. The Application of new flow
improver in Hongjing oil pipeline. Oil & Gas Storage
and Transportation, 23(3): 28-32.
Chen, J. J., 2013. Improving the development effectiveness
of water flooding in heavy oil reservoir. Complex
Hydrocarbon Reservoirs, 7(1): 38-40, 57.
Dang, J. P., Shen, J. J., Zhang, J. F., 1996. The synthesis
and application of GY-2 oil depressant. Oil & Gas
Storage and Transportation, 15(12): 12-15.
Deshmukh, S., Bharambe, D., 2009. Evaluation of effect of
polymeric pour point depressant additives on Indian
waxy crude oil. Petroleum Science and Technology,
27(18): 2097-2108.
Du, T., Wang, S., Liu, H. et al., 2012. The Synthesis and
characterization of methacrylic acid ester-maleic
anhydride copolymer as a Lube oil pour point
depressant. Petroleum Science and Technology, 30(2):
212-221.
Hafiz, A.A., Khidr, T.T., 2007. Hexa-triethanolamine
oleate esters as pour point depressant for waxy crude
oils. Journal of Petroleum Science and Engineering,
56(4): 296-302.
Jiang, K., Hou, J. R., Liu, B. X., et al., 2013. Experimental
study on viscosity reduction by emulsification of Fuyu
heavy oil. Oilfield Chemistry, 30(2): 259-262.
Jin, F. Y., Pu, W. F., Ren, Z. G., et al., 2005. Experimental
study of viscosity reduction by water flooding for
heavy oil. Special Oil and Gas Reservoirs, 12(6):
95-97.
Khidr, T. T., 2011. Pour Point Depressant Additives for
Waxy Gas Oil. Petroleum Science and Technology, 29:
19-28.
Li, J. M., 2010. Huage mixing conveying oil thixotropy
petroleu and natural gas. Xi'an: Xi'an Shiyou
University.
Li, J., Zhang, F., Zhang, Y. L., 1989. Experiment on
transporting crude oil by Maling-Huianbao-Zhongning
pipeline using flow improving chemicals. Oilfield
Chemistry, 6(1): 50-57.
Li, P. J., Zhang, S., He, Y. T., 1990. Classification of crude
oil. Oil & Gas Storage and Transportation, 9(1):74-77.
Liao, H., Tang, S. F., 2018. Experimental research on
emulsification and viscosity reducing of deep
Application and Challenge of Flow Improver for the Development of Heavy Oil and Waxy Crude
81