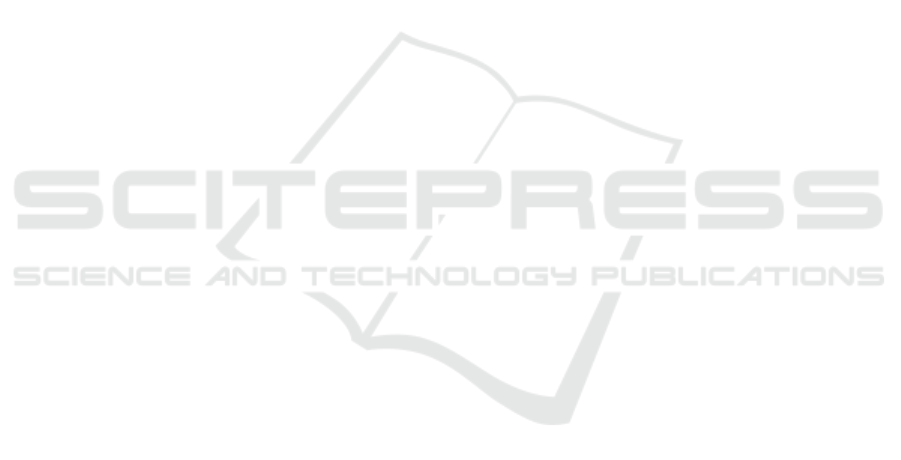
Huang S., 1998. Continuous Arbitrary Strain Profile
Measurements with Fiber Bragg Gratings [J]. Smart
Materials & Structures, 7(2):248.
Lo Y. L., Xiao F. Y., 1998. Measurement of corrosion and
temperature using a single-pitch Bragg grating fiber
sensor [J]. Journal of Intelligent Material Systems &
Structures, 9(10):800-807.
Majumder M., Gangopadhyay T. K., Chakraborty A. K. et
al., 2008. Fibre Bragg gratings in structural health
monitoring—Present status and applications [J].
Sensors & Actuators A Physical, 147(1):150-164.
Miao H. Y., Demers D., Larose S., et al., 2010.
Experimental study of shot peening and stress peen
forming [J]. Journal of Materials Processing Tech,
210(15):2089-2102.
Moussavi-Torshizi S. E., Dariushi S., Sadighi M., et al.,
2010. A study on tensile properties of a novel
fiber/metal laminates [J]. Materials Science &
Engineering A, 527(18-19):4920-4925.
Oken S., June R., R., 1895. Analytical and Experimental
Investigation of Aircraft Metal Structures Reinforced
with Filamentary Composites. Phase 1. Concept
Development and Feasibility. [M]. NASA CR, 1977.
Pan L., Yapici U. A., 2015. Comparative study on
mechanical properties of carbon fiber/PEEK
composites [J]. Advanced Composite Materials,
25(4):359-374.
Qiu W., Cheng X., Luo Y., et al., 2013. Simultaneous
Measurement of Temperature and Strain Using a
Single Bragg Grating in a Few-Mode Polymer Optical
Fiber [J]. Journal of Lightwave Technology,
31(14):2419-2425.
Rubiogonzález C., Josétrujillo E., Chávez F., et al., 2016.
Low velocity impact response of composites and fiber
metal laminates with open holes [J]. Journal of
Composite Materials, 51(6).
Schapery R. A., 1968. Thermal Expansion Coefficients of
Composite Materials Based on Energy Principles [J].
Composite Materials, 2(3):380-404.
Sexton A., Cantwell W. and Kalyanasundaram S., 2012.
Stretch forming studies on a fibre metal laminate
based on a self-reinforcing polypropylene
composite[J]. Composite Structures, 94(2):431-437.
Sinmazçelik T., Avcu E., Bora M. Ö. et al., 2011. A
review: Fibre metal laminates, background, bonding
types and applied test methods [J]. Materials &
Design, 32(7): 3671-3685.
Tsartsaris N., Meo M., Dolce F., et al., 2011. Low-velocity
impact behavior of fiber metal laminates [J]. Journal
of Composite Materials, 45(7):803-814.
Vlot A. and Gunnink J. W., 2001. Fibre Metal Laminates
[M]. Springer Netherlands.
Vlot A., 1996. Impact loading on fibre metal laminates [J].
International Journal of Impact Engineering,
18(3):291-307.
Vlot A., 2001. Glare: history of the development of a new
aircraft material [J]. Springer Netherlands.
Vo T. P., Guan Z. W., Cantwell W. J. et al., 2013.
Modelling of the low-impulse blast behavior of fibre–
metal laminates based on different aluminum alloys
[J]. Composites Part B Engineering, 44(1):141-151.
Vogelesang L. B., Vlot A., 2000. Development of fibre
metal laminates for advanced aerospace structures [J].
Journal of Materials Processing Technology,
103(1):1-5.
Zhang H., Zhang Z., Friedrich K., et al., 2006. Property
improvements of in situ epoxy nanocomposites with
reduced interparticle distance at high nanosilica
content [J]. Acta Materialia, 54(7):1833-1842.
Zhu S., Wang Y., Tong M., et al., 2014. Numerical
simulation of bird impact on fibre metal laminates [J].
Polymers & Polymer Composites, 22(2):147-156.
Study on Monitoring of Stress and Strain during Curing Process of Fiber Metal Laminates
109