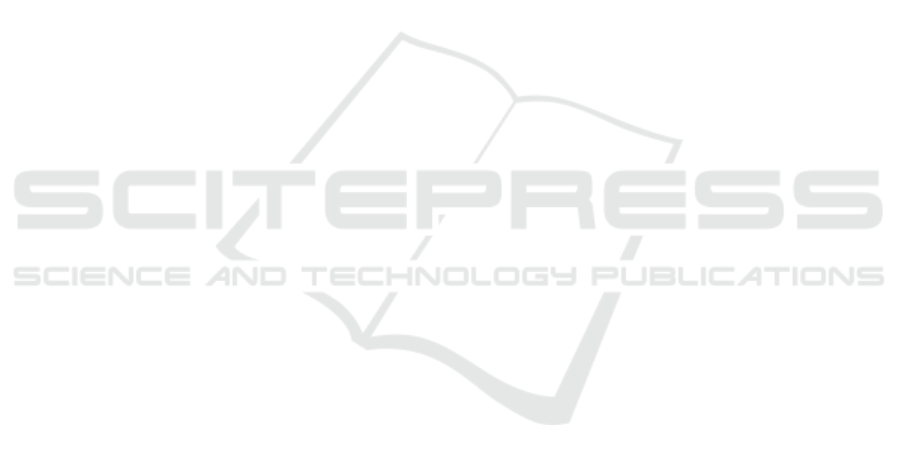
relatively cheap, easy to process, and it has a wide
range of industrial applications. Pure alumina has a
melting point of 2072ºC, therefore alumina
components are used at operating temperatures as
high as 1200 – 1300°C. Despite there are some works
dedicated to the study of the alumina behaviour when
subjected to thermal shock (Saâdaoui and Fantozzi,
1998; Hahn and Lee, 1999; Lee et al., 2002;
Dimitrijevic et al., 2013; Belghalem et al., 2014; Li et
al., 2016) we do not know any experimental work
dealing with the behaviour of alumina when subjected
to high-temperatures cycles at the surface of the test-
pieces with rapid cooling/heating conditions.
Therefore, the primary goal of this work is to evaluate
the performance of test-pieces (circular discs with 25
mm diameter and 2 mm thickness) of a commercial
grade of high-purity dense monolithic Alumina
(RAPAL
®
100) when it is exposed to rapid cycles of
temperature variation.
The creation of rapid cycles of temperature
variation at the surface of a test-piece is not easy to
achieve using the traditional heating-systems,
whatever they are: fuel or gas combustion furnaces,
electric resistance furnaces, induction furnaces, or
even microwave furnaces. However, one way to
generate rapid variations of temperature is by direct
exposure of the test-piece to concentrated solar
radiation. Some examples of the use of concentrated
solar radiation for rapid heating and thermal cycling
are available in the literature (Douale et al., 1999;
Kováčik et al., 2014; Sallaberry et al., 2015).
2 MATERIAL AND TESTS
2.1 RAPAL
®
100 Alumina Discs
The alumina produced by Rauschert company with a
purity grade of 99.7% bears the trade names of
RAPAL
®
200 or RAPAL
®
100. This type of alumina
possesses a density close to the theoretical value,
because is practically free of porosity. It presents
excellent properties, namely: very high hardness
which gives the pieces a high wear resistance; high
mechanical strength; good temperature resistance up
to 1650ºC; good/moderate thermal conductivity; it is
an electrical isolator even at high temperatures; it is
corrosion resistant in diluted acids and lyes; it allows
highly polished surfaces, which show low-friction
coefficient.
As mentioned in the Introduction, in the present
work we have used circular discs, with 25 mm
diameter and 2 mm thickness, made of commercial
high-purity dense monolithic alumina RAPAL
®
100.
According to the manufacturer (the Rauschert
company), the discs were produced through uniaxial
pressing. The starting powder mean particle size (d
50
)
is 1 micron, with a specific area of 2.11 m
2
/g (BET).
The powder compacting pressure is 100 MPa, applied
at ambient temperature. After being compacted, the
discs are sintered at 1635ºC with a holding time of
150 minutes. The following properties of RAPAL
®
100 are mentioned by the manufacturer (Rauschert
data sheet, 2018): density: > 3.85 g/cm
3
; uniaxial
flexural strength: 300 MPa; Young’s modulus: 380
GPa; Mohs hardness: 9; Vickers hardness HV
0.1
:
1700‒2300; linear thermal expansion coefficient (in
the range 20‒1000°C): 910
-6
K
-1
; thermal
conductivity: 19‒30 W m
-1
K
-1
; electrical resistivity
at 20°C: 10
14
.cm.
2.2 High Temperature Cycles
Tests with rapid heating-cooling cycles were carried
out thanks to the capabilities and characteristics of a
high-power solar furnace: the 60 kW power solar
furnace SF60 of the Plataforma Solar de Almería, in
Spain. A schematic of the solar furnace test system
for obtaining a concentrated solar beam horizontally
oriented towards the target is shown in Figure 1. In
the case of SF60, the solar direct radiation is reflected
by a 130 m
2
flat heliostat (placed outside the building)
onto a fixed parabolic concentrator (inside the
building) composed of 89 facets (curved mirrors)
which altogether make a total of 100 m
2
parabolic-
shape reflecting surface area (see Figure 2). The
parabolic concentrator reflects and concentrates the
sunlight on a focal area where the test setup is
installed. The solar flux can be controlled by
adjusting the opening of the shutter or attenuator; and
hence it is the opening percentage of the shutter that
controls the temperature in the test setup. In our
experiments, a 45º inclined mirror was placed before
the focal area so that the concentrated solar beam
becomes vertically oriented towards the target. The
45º inclined mirror is depicted in Figure 2.
The test setup placed at the focal area is depicted
in Figures 3 and 4 in order to explain the positioning
of the discs and the location of the thermocouples that
were used to measure the temperature at various
locations in the vicinity of the alumina discs. Figure
3 shows six discs of RAPAL
®
100 duly positioned on
a zirconia felt and ready to be irradiated by
concentrated sunlight. During this work, 36 identical
discs were exposed to the thermal cycles, in groups of
6 + 6 = 12 discs.
MEEP 2018 - The Second International Conference on Materials Chemistry and Environmental Protection
174