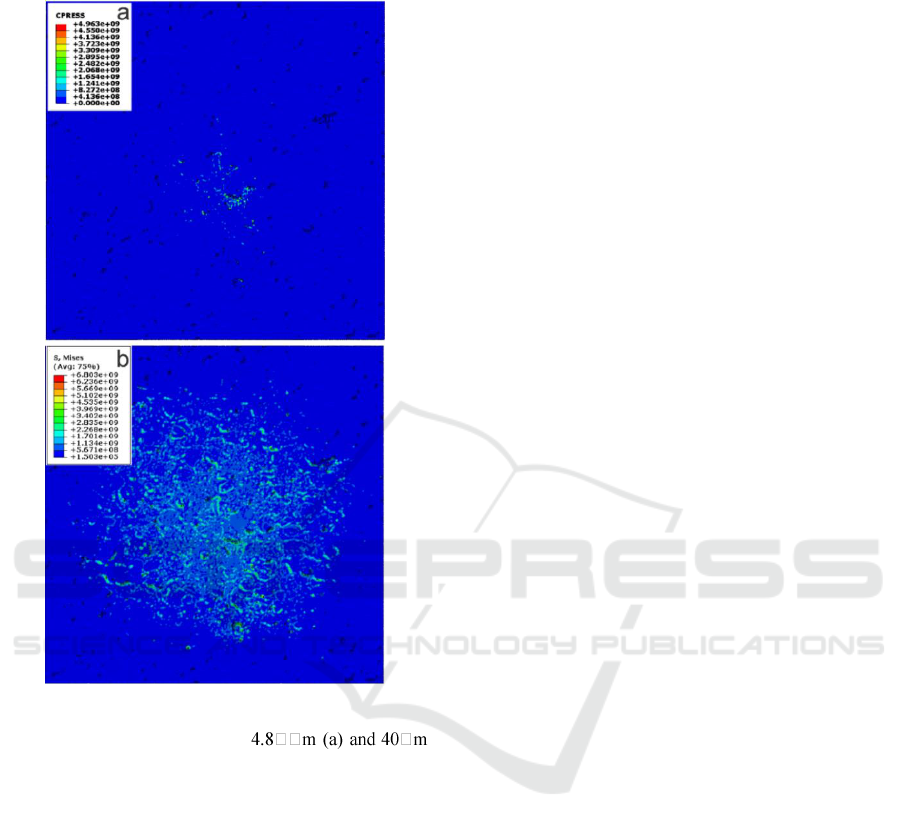
in the present simulations but can be incorporated
into future experiments and models.
Figure 4: Contact pressure distribution as predicted by the
model at an indentation depth of
(b).
4 CONCLUSIONS
Spark erosion can generate randomly rough surfaces
with controlled roughness and a high fractal
dimensions. Combining standard equipment for
instrumented indentation with an optical surface
profiler mounted on the same console, precise
measurements of contact load-displacement curves
can be combined with a detailed analysis of the
surface topography before and after testing.
Using purposely developed software, the
measured surface can be superposed on a pre-existing
finite element mesh. The measured geometry and the
finite element geometry are the same, the only
limitation is the spatial resolution of the
measurement. This is a significant innovation and can
be used in future, more extensive studies in which the
surface roughness will be varied through systematic
analysis of the electric discharge parameters.
ACKNOWLEDGEMENTS
Financial support from DGAPA projects PAPIIT
IN114718 and PAPIME PE111018 is acknowledged.
MA Ramírez and CG Figueroa thank DGAPA for
their post-doctoral fellowships. HA Juárez thanks
CONACYT for her master’s scholarship.
REFERENCES
Bennett, A.I., Harris, K.L., Schulze K.D., Urueña, J.M.
McGhee A.J., Pitenis A.A., Müser M.H., Angelini,
T.E., Sawyer,W.G., 2017. Contact measurements of
randomly rough surfaces. Tribology Letters 65, 134.
Deltombe, R., Kubiak, K. J., Bigerelle, M., 2014. How to
select the most relevant 3D roughness parameters of a
surface. Scanning: The Journal of Scanning
Microscopies, 36, 150.
Greenwood, J.A., Williamson, J.B.P., 1966. Contact of
nominally flat surfaces. Proceedings of the Royal
Society of London A, 295, 300.
Majumdar, A., Bhushan, B., 1990. Role of fractal geometry
in roughness characterization and contact mechanics of
surfaces. Journal of Tribology, 112, 205.
Majumdar, A., Bhushan, B., 1991. Fractal model of
elastic-plastic contact between rough surfaces. Journal
of Tribology, 113, 1.
Müser M.H., Dapp W.B., Bugnicourt R., Sainsot P.,
Lesaffre N., Lubrecht T.A., Persson B.N., Harris K.,
Bennett A. et al., 2017. Meeting the contact-mechanics
challenge. Tribology Letters. 65, 118.
Nayak, P.R. 1971. Random process model of rough
surfaces. Journal of Lubrication Technology, 93, 398.
Schouwenaars, R., Jacobo V.H., Ortiz A., 2017. The effect
of vertical scaling on the estimation of the fractal
dimension of randomly rough surfaces. Applied
Surface Science. 425, 838.
Singh, S., Maheshwari, S., Pandey, P.C., 2004. Some
investigations into the electric discharge machining of
tool steel using different electrode materials. Journal of
materials processing technology, 149, 272.
Wen Y, Tang J, Zhou, W., Zhu, C., 2018. An improved
simplified model of rough surface profile. Tribology
International 125 75.
Whitehouse, D.J., Archard, J.F., 1970. The properties of
random surfaces of significance in their contact.
Proceedings of the Royal Society of London. A. 316,
97.
Yuan Y, Cheng Y, Liu, K., Gan, L., 2017. A revised
Majumdar and Bushan model of elastoplastic contact
between rough surfaces. Applied Surface Science. 425,
1138.
Physical and Numerical Simulation of Contact Mechanics of Spark-eroded Tool Steel with Controlled Roughness
183