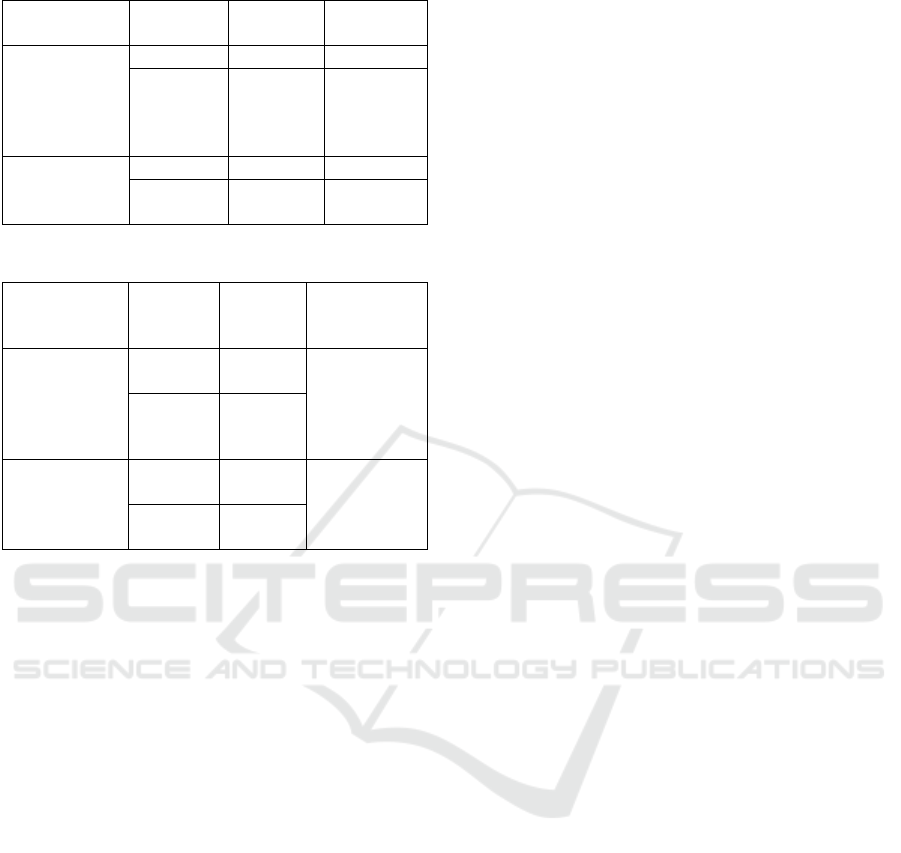
Table 7. Damage and Fatigue Life
Bottom
(Rohmadhana
and
Kurniawati,
2016)
Table 8: Combination Fatigue Life
Combination
fatigue life
(year)
Bottom
(Rohmadhana
and
Kurniawati,
2016)
Based on Table 8 it can be seen that the shortest
fatigue life of the structure is on the deck with the
fatigue life 22 years while at the bottom is 28 years.
It is caused by the deck is the farthest distance from
the neutral axis of the ship.
5 CONCLUSION
According to the analysis and results, this research
can be concluded into:
1. Fatigue life of each case at the bottom is 20
years and 31 years for full cargo and empty
cargo respectively where each load cases are
acceptable according to ABS (20 years).
2. Fatigue life of deck structure has the shortest life
approximately 16 years and 24 years for full
cargo and empty cargo respectively where full
cargo condition is not acceptable according to
ABS (20 years).
3. Both fatigue life of combinations of load cases
at the bottom and at deck are 28 years and 22
years respectively where it is acceptable
according to ABS (20 years) with factor 0.85
represented as the service life of the ship.
REFERENCES
A. Yustiawan, & K. Suastika, Fatigue Life Prediction
of Keel Buoy Tsunami Structure with Spectral
Fatigue Analysis Method, Jurnal Teknik ITS Vol.
1 No. 1 ISSN:2337-3539, Surabaya: Institut
Teknologi Sepuluh Nopember, (2012).
American Bureau of Shipping (ABS), Spectral-Based
Fatigue Analysis for Vessels, Houston: American
Bureau of Shipping (2016).
Ardianus, S.H. Sujiatanti, & D. Setyawan, Analisa
Kekuatan Konstruksi Sekat Melintang Kapal
Tanker dengan Metode Elemen Hingga. Jurnal
Teknik ITS 6 (2), G183-G188, ISSN: 2337-3539,
Surabaya: Institut Teknologi Sepuluh Nopember.
B. Santosa, & D. Setyawan, Lecture Handout, Ship
Structure and Strength, Surabaya: Institut
Teknologi Sepuluh Nopember (ITS), (2013).
D. Septiana, Soeweify, A Imron, Estimated Fatigue
Life on the Tanker Ship Bracket Based on
Common Structural Rules, Jurnal Teknik ITS
Vol. 1 No. 1 ISSN:2337-3539, Surabaya: Institut
Teknologi Sepuluh Nopember, (2012).
F. Rohmadhana, & H.A. Kurniawati., Technical and
Economic Analysis of Conversion of Landing
Craft Tanks (LCT) to Crossing Motorboats
(KMP) Type Ro-ro for Ketapang Routes
(Banyuwangi Regency) - Gilimanuk (Jembrana
Regency), Jurnal Teknik ITS Vol. 5 No. 2
ISSN:2337-3539, Surabaya: Institut Teknologi
Sepuluh Nopember, (2016).
M. Huda, & B. Santosa, Analysis of Estimated Age
of Structure on the 10 GT Catamaran Fish Ship
Using Finite Element Method, Jurnal Teknik ITS
Vol. 1 No. 1 ISSN:2337-3539, Surabaya: Institut
Teknologi Sepuluh Nopember, (2012).
M. N. Misbah, D. Setyawan, & W. Murti Dananjaya.,
Construction Strength Analysis of Landing Craft
Tank Conversion To Passenger Ship Using Finite
Element Method, Journal of Physics: Conference
Series. 974. 012054. 10.1088/1742-
6596/974/1/012054, (2018).
M. Rusdi., M. N. Misbah., T. Yulianto., Analysis of
Fatigue Life on Oil Tanker Bracket with Sloshing
Load, Jurnal Teknik ITS Vol. 7 No. 1 ISSN:2337-
3539, Surabaya: Institut Teknologi Sepuluh
Nopember, (2018).
R. Bhattacharyya, Dynamic of Marine Vehicle, U.S.
Naval Academy, Annapolis: Marryland. (1978).
S. Chakrabarti, Hydrodynamic of Offshore
Structures, Boston, USA: Computational
Mechanics Publications Southampton (1987).
W. Weibull, Fatigue Testing and Analysis of Results,
Oxford: Pergamon Press, (1961).
ISOCEEN 2018 - 6th International Seminar on Ocean and Coastal Engineering, Environmental and Natural Disaster Management
96