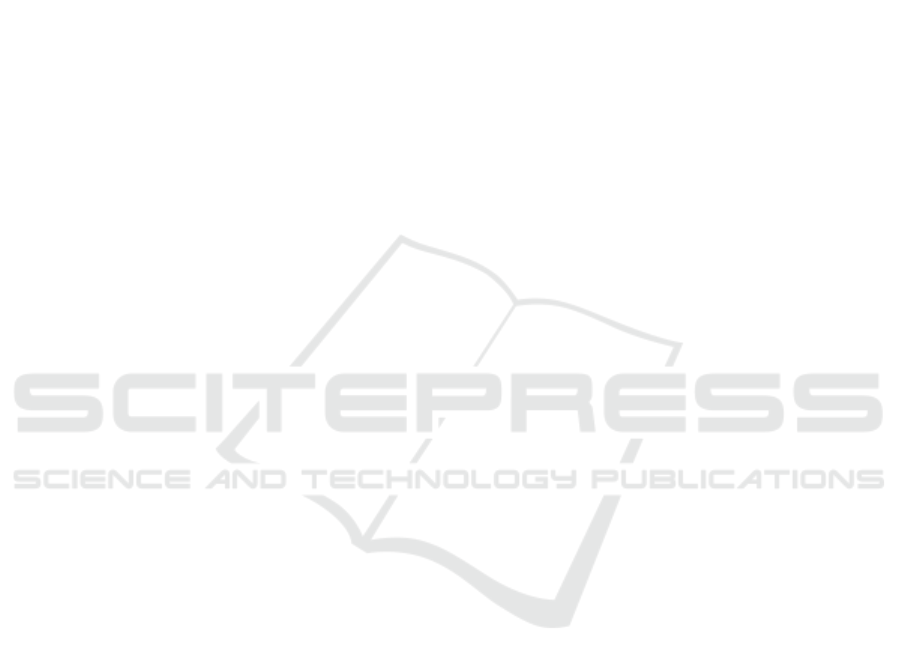
Comparison Study of Structural Strength between Longitudinal and
Transverse Modulus on The Hatch Cover using Finite Element
Method
Dony Setyawan
1
, Septia Hardy Sujiatanti
1
and Novario Pratama Adiguna
1
1
Department of Naval Architecture, Faculty of Marine Technology, Institut Teknologi Sepuluh Nopember, Surabaya,
Indonesia
Keywords: The Longitudinal Modulus, Transverse Modulus, FEM.
Abstract: Container ship carries cargo that mostly container, so cargo hold be designed with the large enough
hatchway to making easy loading and unloading container. Owners usually want to optimize space on cargo
hold. Optimizing space on cargo hold means that if cargo hold is fully loaded by the container, the owner
can still put the container above hatch cover. There are 2 construction members which influence hatch cover
strength, longitudinal & transverse. Finite element method is used to compare strength between longitudinal
& transverse of the hatch cover. The analysis was performed by changing ± 10% & ± 20% longitudinal
modulus and transverse modulus of the model hatch cover. As a result, due to increase 20% longitudinal
modulus, stress is reduced -9.903%, while adding 20% transversal modulus only reduces -5.31% stress.
Reducing 20% longitudinal modulus increase 5.47% stress, while reducing 20% transversal modulus only
increases 4.94% stress. According to the analysis result, it can be inferred that changing the longitudinal
modulus is more influential than changing transversal modulus. e
1 INTRODUCTION
The function of hatch cover on container ships
generally has the same working system and function,
which is used to cover the part of the hatch on the
container ship. However, what distinguishes
between hatch cover on cargo ships and container
ships is that container ships carry commonly called
containers, so container ship must have a wide hatch
for loading space. Owners usually want to optimize
space on cargo hold. Optimizing space on cargo hold
means that if cargo hold is fully loaded by the
container, the owner can still put the container above
hatch cover (Keith, 2001). Hatch cover must have
enough strength to hold the load from the container.
Previous study an analysis was carried out by
comparing 3 variations of hatch cover model. The
first model hatch cover is divided into 3 transverse
partitions. Second model hatch covers without
partition. The third model hatch cover is divided into
5 longitudinal partitions. From three types of hatch
cover, model hatch cover 3 transverse partition is the
most effective model (Fikri and Kurniawati, 2016).
In this comparison study between longitudinal &
transverse construction, most affect construction to
hatch cover stress will be searched with 3 transverse
partitions as a model. The analysis is performed by
changing the longitudinal modulus and transverse
modulus of the hatch cover. From the comparison of
the stress result, the construct will be obtained which
is the most influential to the hatch cover
2 LITERATURE REVIEWS
Hatch cover is a very important equipment in the
ship, which construction and mechanism must
follow Classification rules and International Load
Line Convention (ILLC) 1966. The purpose of the
hatch cover and hatch coaming are to prevent water
from entering through the opening (loading) of the
loading space on the ship deck.
One type of hatch cover is a lift-away hatch
cover (Fikri and Kurniawati, 2016). Hatch cover
using pontoon or lift away hatch cover makes it
easier for the loading and unloading system. Hatch
cover type Lift away hatch cover is good for ships
Setyawan, D., Sujiatanti, S. and Adiguna, N.
Comparison Study of Structural Strength between Longitudinal and Transverse Modulus on The Hatch Cover using Finite Element Method.
DOI: 10.5220/0008375300970100
In Proceedings of the 6th International Seminar on Ocean and Coastal Engineering, Environmental and Natural Disaster Management (ISOCEEN 2018), pages 97-100
ISBN: 978-989-758-455-8
Copyright
c
2020 by SCITEPRESS – Science and Technology Publications, Lda. All rights reserved
97