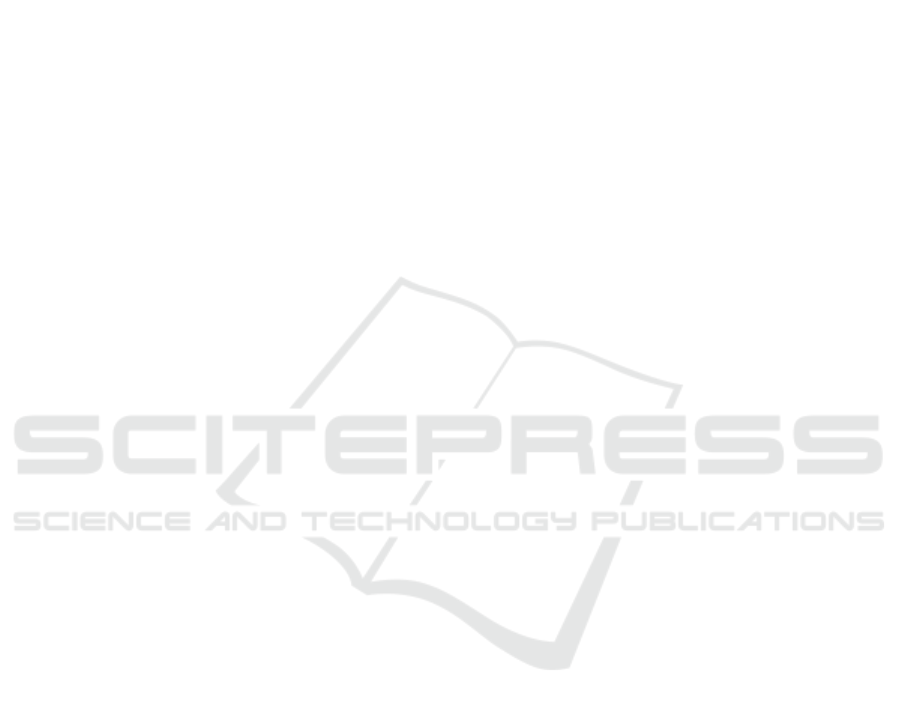
Influence of the Cut-out Shape on the Fatigue Ship Structural Detail
Septia Hardy Sujiatanti
1
, Totok Yulianto
1
, Wing Hendroprasetyo Akbar Putra
1
and Rizky Chandra
Ariesta
1
1
Department of Naval Architecture, Faculty of Marine Technology, Institut Teknologi Sepuluh Nopember, Surabaya,
Indonesia
Keywords: Cut-out Shape, Fatigue, Ship.
Abstract: Damage structured mostly occurred caused by the crash. One of the causes of the accident is the fatigue of
the hull side of the ship. The composition of the side hull structure comprises a detailed structure that often
experiences a wave pressure load failure. In this study, the load given is the dynamic load of the wave. The
structural pressures generate the stress used to evaluate the strength and determine the fatigue life of the
structure. This study involves modelling details structured with 3 variations of the model. The modelling is
conducted using Finite Elements Analysis software by calculating the pressure load that adjusts the location
of the model. The model of each cut-out is created variations. These variations resulted in the estimate fatigue
life. The fatigue life calculation used several approaches i.e. Simplified Fatigue Analysis and Fracture
Mechanics.
1 INTRODUCTION
Generally, the ship structure may be longitudinally
stiffened or transversely stiffened with stiffeners and
bulkheads. In its entire life is complex structure will
be accepted to distinguished load conditions
beginning with the ship launching and continuing
with each sailing and interval; docking for survey and
repair (Joem, 2010). Although a ship may be designed
to withstand the ultimate imposed by a wave, failure
can occur due to apparently low stresses generated by
the continuous load (Mathews, 2013).
Fatigue of structural components in ships is a long
known problem and has been investigated in depth
owing to its relevance in design. Fatigue design
became an important subject due to use of higher
strength materials, serve environmental conditions
and optimized structural dimensions (Hughes, 2010).
The factors with contributing to the fatigue of ship
structure are the local configuration and geometry of
details structured (DNV, 2010). In ship structure, a
major fraction of the total number of fatigue damages
occurs in panel stiffeners on the ship side and bottom
on the boundaries of ballast and cargo tanks. In
tankers, cracks occur mostly on the side longitudinals
at the connections to transverse webs (CSR, 2012).
The aim of this paper is to evaluate fatigue life
using three geometry shape of slot design. Analyze
from the model using finite element analysis. The
goal of the Finite Element model was to successfully
predict the stress value with various of geometry
shape. The best of geometry shape can be assumed
based on the age resulted from the calculation
process.
2 LITERATURE REVIEWS
In general, the design of a construction must be able
to withstand loads and other factors that cause failure
in the structure itself. At sufficient loads, secondary
construction in particular, on construction details can
be made simple and save production but still meet the
required strength requirements. Based on several
construction designs in this research, an evaluation of
the strength and age of the cut-out design was carried
out. cut out is a structure on a ship classified as a small
construction on a ship or commonly called structural
intersection. Cut out itself has an important role as a
constituent of construction.
Cut out is a part of the construction that serves to
blow reinforcement to another structure or support,
for example, which is located in a non-impermeable
bulkhead in addition to providing strength to the
construction ring which is circular in a transverse
position. Cut out is located on the web frame or side
Sujiatanti, S., Yulianto, T., Putra, W. and Ariesta, R.
Influence of the Cut-out Shape on the Fatigue Ship Structural Detail.
DOI: 10.5220/0008375601110115
In Proceedings of the 6th International Seminar on Ocean and Coastal Engineering, Environmental and Natural Disaster Management (ISOCEEN 2018), pages 111-115
ISBN: 978-989-758-455-8
Copyright
c
2020 by SCITEPRESS – Science and Technology Publications, Lda. All rights reserved
111