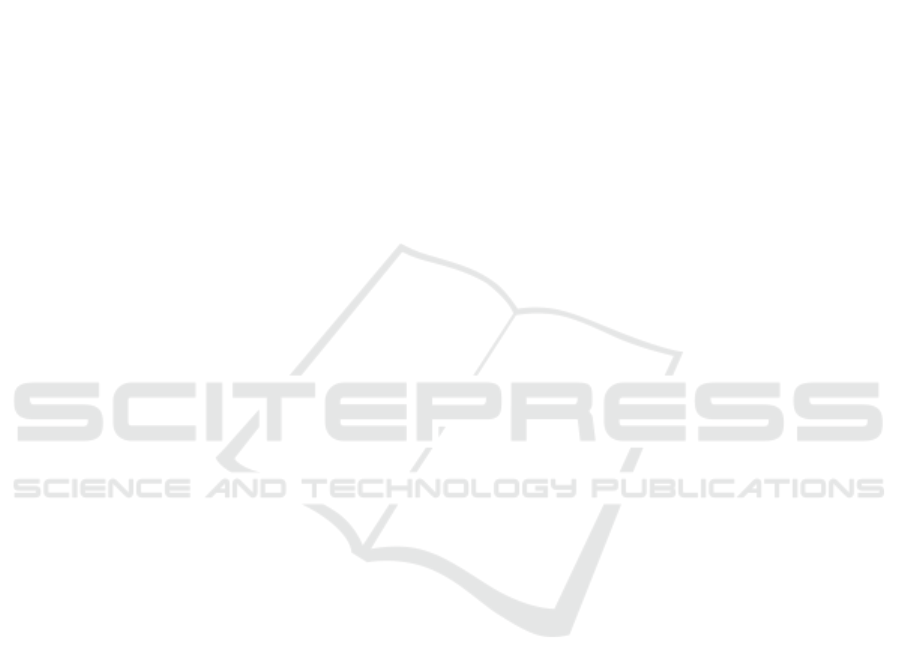
Aerodynamic Performance Analysis of Vertical Axis Wind Turbine
(VAWT) Darrieus Type H-Rotor using Computational Fluid Dynamics
(CFD) Approach
Wisnu Wardhana
1
, and Elyas Nur Fridayana
1
1
Department of Ocean Engineering, Faculty of Marine Technology, Institut Teknologi Sepuluh Nopember (ITS), Surabaya
Keywords:
Aerodynamics, Airfoil, Darrieus, CFD Simulation, Wind Turbine
Abstract:
The recent renewable energy grows significantly concerning on people awareness of the negative effect to-
ward environment. Based on the advantages that should be offer by Vertical Axis Wind Turbine (VAWT)
becomes an interested object to be observed. Especially VAWT Darrieus, H-Rotor type. Not only known has
simple structure but also has higher efficiency than Savonius. Airfoil Profile becomes substantial because its
aerodynamic effects which run on the Darigus turbine. Numerous previous studies observed that the use of
asymmetric airfoil gives advantage toward Darrieus turbine efficiency. In this case, this research focuses on
the influence of cambered airfoil toward the maximum position to the turbine performance. The Investigation
is observed using Computational Fluid Dynamic (CFD) which is two dimensions Darrieus turbine type H-
Rotor turbine model is simulated in transients current condition. In result, the simulation as power coefficient
presented the best turbine performance is conducted by airfoil with the maximum camber position close to the
trailing edge. While the variation on the chord length gives a solidity ratio of 0.6 as the best value between the
above and below.
1 INTRODUCTION
Globalisation now days demanded by hygienic avail-
ability and low-cost resource. Therefore, regarding
human awareness about the negative impact of con-
servative energy resource caused renewable technol-
ogy conversion become vital. In this case, Wind En-
ergy Conversion System (WECS) is the most built
and developed. The furthermost WECS technology is
Horizontal Axis Wind Turbine (HAWT). It has higher
efficiency than the other kind of Vertical Axis Wind
Turbine (VAWT). Even though, it offer another ad-
vantage such as the simplest structure. Moreover,
VAWT able to run at any course of the wind and to
provide another benefit such a minimum noise, stable
in wind turbulence condition, integrate with another
building and give easiness in its generator, gearbox
and bearing application (Ahmadi-Baloutaki, 2015).
There are two differences major in VAWT imple-
mentation, those are: Saviours which is the interac-
tion of the wind turbine utilizing drag force and Dar-
rieus which is using lift force of aerodynamic effect,
the second VAWT is the common one to use as wind
turbine electricity (Manwell et al., 2010). Which is in
this case blade design is important to gain the effect
of aerodynamic due to airfoil design. Airfoil is par-
ticular form of geometry design to gain lift force and
to minimize increasing drag force.
In fluid currency, airfoil lift force is occurred be-
cause the differences of upper and lower surface pres-
sure. It caused by angle of attack and camber (?).
Airfoil symmetry often used in darrieus turbine to
minimize the negative torque during single rotor ro-
tation. The other hand, airfoil with camber increasing
the lift force at the zero attack angle and functioning
at higher maximum torque, but at the second half of
rotation it always occurred negative torque. Accord-
ing to the study by Sengupta et al. (2016), Bausas and
Danao (2015), asymmetrical airfoil is giving the im-
provement to the whole of rotor performance. Qamar
and Janajreh (2017) researched the rotor performance
with NACA 4512 and NACA 7512 asymmetrical air-
foil. The result is airfoil with moderate camber has
better performance.
The purpose of this research is to identify the in-
fluence of maximum camber at 4 digit NACA con-
ventional airfoil. The chosen type of airfoil is NACA
4312, 4512 dan 4712 which is the second digit of vari-
Wardhana, W. and Fridayana, E.
Aerodynamic Performance Analysis of Vertical Axis Wind Turbine (VAWT) Darrieus Type H-Rotor using Computational Fluid Dynamics (CFD) Approach.
DOI: 10.5220/0008542700050011
In Proceedings of the 3rd International Conference on Marine Technology (SENTA 2018), pages 5-11
ISBN: 978-989-758-436-7
Copyright
c
2020 by SCITEPRESS – Science and Technology Publications, Lda. All rights reserved
5