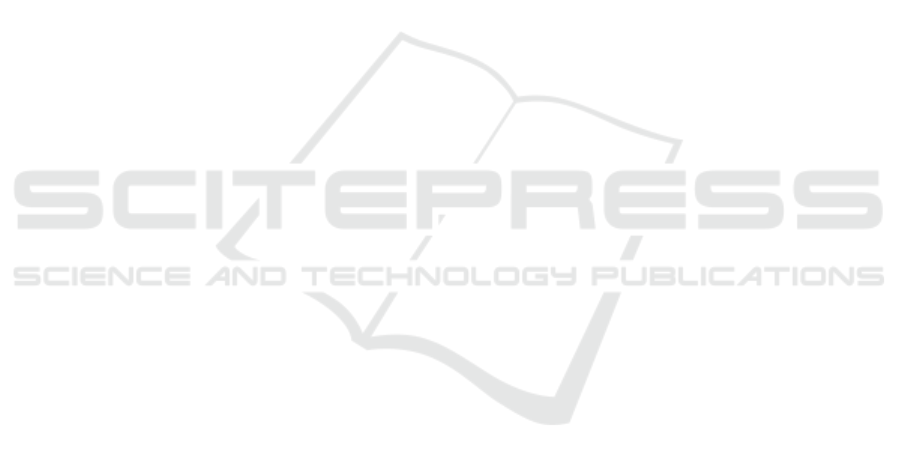
the plat c. On the other hand, smaller drag reduction
just make the air entrances the flow a bit harder and
longer chord length of the foil just make the resis-
tance appendages slightly bigger. In this research we
choose the angle of attack 20
◦
and chord length 50 mm
because they were giving the biggest amount of drag
reduction among others by 3.241% drag reduction. In
the future, we hope that the friction losses which is
occur on the foil will be in the future journal.
ACKNOWLEDGEMENTS
Authors are thanks to Department of Mechanical En-
gineering, Faculty of Engineering, Universitas In-
donesia for making facility available and also grant
PITTA No. 2561/UN2.R3.1/HKP05.00/2018.
REFERENCES
Cui, Z., Fan, J. M., and Park, A.-H. (2003). Drag coeffi-
cients for a settling sphere with microbubble drag reduc-
tion effects. Powder technology., 138(2):132.
Duncan, J. H. (1981). An Experimental Investigation of
Breaking Waves Produced by a Towed Hydrofoil. Pro-
ceedings of the Royal Society of London. Series A, Math-
ematical and Physical Sciences, 377(1770):331–348.
Gebreslassie, M., Tabor, G., and Belmont, M. (2012). Cfd
simulations for sensitivity analysis of different parame-
ters to the wake characteristics of tidal turbine. Open J.
Fluid Dyn., 2.
Kodama, Y., Kakugawa, A., Takahashi, T., and Kawashima,
H. (2000). Experimental study on microbubbles and their
applicability to ships for skin friction reduction. Inter-
national Journal of Heat and Fluid Flow International
Journal of Heat and Fluid Flow, 21(5):582–588.
Kumagai, I., Kushida, T., Oyabu, K., Tasaka, Y., and Murai,
Y. (2011). FLOW BEHAVIOR AROUND A HYDRO-
FOIL CLOSE TO A FREE SURFACE. Vis Mech Proc
Visualization of Mechanical Processes, 1(4).
Kumagai, I., Nakamura, N., Murai, Y., Tasaka, Y., and
Takeda, Y. (2010). A new power-saving device for air
bubble generation: hydrofoil air pump for ship drag re-
duction. In Proceedings of the International Conference
on Ship Drag.
Kumagai, I., Takahashi, Y., and Murai, Y. (2015). Power-
saving device for air bubble generation using a hydrofoil
to reduce ship drag: Theory, experiments, and applica-
tion to ships. Ocean Engineering, 95:183 – 194.
Mohanarangam, K., Cheung, S. C. P., Tu, J. Y., and Chen,
L. (2009). Numerical simulation of micro-bubble drag
reduction using population balance model. Ocean Engi-
neering, 36(11):863 – 872.
Muste, M., Yu, K., Fujita, I., and Ettema, R. (2009). Two-
phase flow insights into open-channel flows with sus-
pended particles of different densities. Environmental
Fluid Mechanics, 9:161–186.
Ockfen, A. E. and Matveev, K. I. (2009). Aerodynamic
characteristics of NACA 4412 airfoil section with flap in
extreme ground effect. International Journal of Naval
Architecture and Ocean Engineering, 1(1):1 – 12.
Olazabal-Loum
´
e, M., Danvin, F., Julien, M., and Aupoix,
B. (2017). Study on k-w shear stress transport model
corrections applied to rough wall turbulent hypersonic
boundary layers.
Pang, M. J., Wei, J. J., and Yu, B. (2014). Numerical study
on modulation of microbubbles on turbulence frictional
drag in a horizontal channel. Ocean Engineering, 81:58
– 68.
Series A (1779). Mathematical and Physical Science. Num-
ber 377.
Shereena, S. G., Vengadesan, S. N., Idichandy, V. G., and
Bhattacharyya, S. K. (2013). Cfd study of drag reduction
in axisymmetric underwater vehicles using air jets.
Uhlman, J. S. (1987). The Surface Singularity Method Ap-
plied to Partially Cavitating Hydrofoils. Journal of Ship
Research, 31(02):107–124.
Yanuar, Gunawan, Sunaryo, and Jamaluddin, A. (2012).
Micro-bubble drag reduction on a high speed vessel
model. Journal of Marine Science and Application,
11(3):301–304.
Zhang, J., Yang, S., and Liu, J. (2018). Numerical investi-
gation of a novel device for bubble generation to reduce
ship drag. International Journal of Naval Architecture
and Ocean Engineering, 10(5):629 – 643.
The Effect of Angle of Attack and Chord Length of the Foil on Winged Air Induction Pipe Optimization toward Drag Reduction by using
Numerical Approach
125