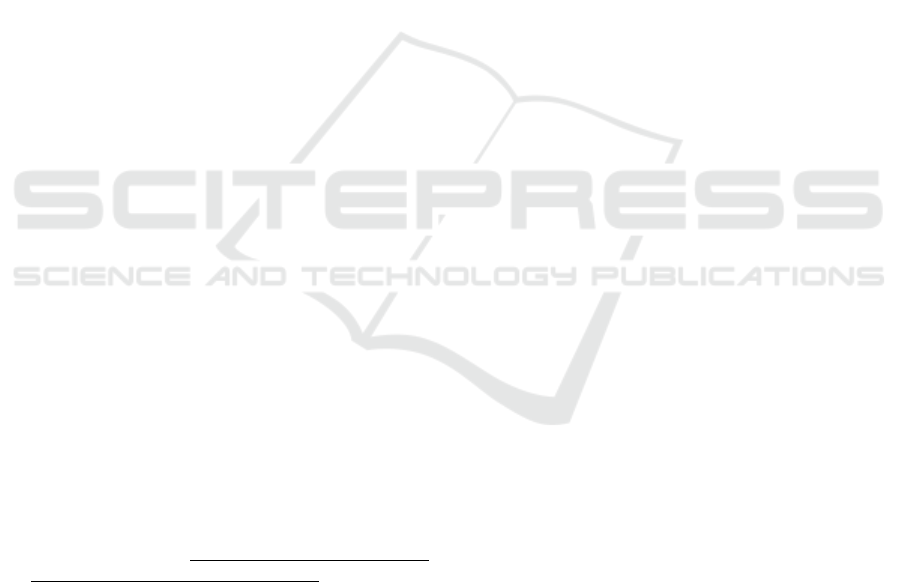
8 CONCLUSIONS
This paper presents a stage in the development of AT-
OWEC research, which involves the preparation of
physical test models at the Laboratory of Ocean
Structure Hydrodynamics, DOE - ITS. A number of
important aspects that have been explained can
further be summarized as follows:
• The AT-OWEC physical model measures 1 : 10
to the full scale, sized Dh = 400 mm and Hh =
550 mm, made of aluminum material, and has
been designed to meet geometric, kinematic and
dynamic similarities;
• The pitch motion measurement will be carried
out utilizing the gyroscope as primary
instrument, assisted by checking the target
visual tracing recorded through a digital
camera;
• Data acquisition system has been prepared with
appropriate tools to produce outputs that take
into account the appropriate calibration factors;
The results of numerical modelling of pitch moti-
ons have been prepared as data for comparative
studies with the results of the test model, which will
be implemented in the near future.
ACKNOWLEDGEMENTS
The authors are deeply grateful to the Ministry of
Research Technology and Higher Education,
Republic of Indonesia, for providing the research
grant to AT-OWEC establishment through the
Higher Education Primary Basic Research (PDUPT)
scheme in the fiscal year of 2018.
REFERENCES
Atkins, 2017. Chrysaor Solan Development, North Sea
(West of Shetland), WS Atkins Plc.. [Online]
Available at: http://www.atkinsglobal.com/zh-
cn/projects/solan-offshore-development
[Accessed 22 2 2017].
Bar-Avi, P. & Benaroya, H., 1996. Planar motion of an
articulated tower. J. of Sound and Vibration, 198(1), pp.
27-50.
Bar-Avi, P. & Benaroya, H., 1996. Response of a two
degrees of freedom articulated tower to different
environmental conditions. Int. J. of Non-Linear
Mechanics, 31(5), pp. 717-741.
Budiman, A. et al., 2014. Sepuluh Gagasan untuk
Menguatkan Kembali Sektor Energi Terbarukan.
s.l.:Global Energy & Materials, McKInsey &
Company.
Chakrabarti, S., 2001. Stability analysis of interaction of an
articulated tower with waves. WIT Trans. on the Built
Env., Volume 56, pp. 1-10.
Chakrabarti, S. K., 1998. Physical model testing of floating
offshore structures. Huston, Texas, USA, Dynamic
Positioning Conf., Marine Technology Society.
Chakrabarti, S. K. & Cotter, D. C., 1980. Transverse motion
of articulated tower. J. of Waterways, Port, Coastal and
Ocean Division, ASCE, p. 107.
Chanson, H., 2008. Physical modelling, scale effects and
self¬similarity of stepped spillway flows. Honolulu,
Hawai, USA, World Environmental and Water
Resources Congress 2008, ASCE.
Choy, L. T., 2012. Blue Energy - Ocean Power (Piston
Pump & Racks). s.l. Patent No. International Patent
Application No. PCT/SG2011/000232.
Direktur AEBET, 2013. Kebijakan pengembangan dan
peman¬faatan sumber energi terbarukan. Yogyakarta:
Lokakarya Nasional VI: Manajemen Penelitian dan
Pengabdian Kepada Masyarakat di Perguruan Tinggi.
Djatmiko, E. B., 1987. Experimental investigation into
SWATH ship motions and loadings. M.Sc. Thesis ed.
Dept. NAOE, Univ. of Glasgow, UK.
Djatmiko, E. B. et al., 2017. Concept Development of
Articulated Tower – Ocean Energy Converter (AT-
OWEC). Int. Conf. on Marine Tech. SENTA 2017,
Surabaya.
Djtamiko, E. B., Syahroni, N. & Sujantoko, 2017.
Perancangan dan analisis sistem konversi energi
gelombang laut berkonfigurasi articulated tower.
Laporan Akhir Program Penelitian Laboratorium, Dana
Lokal ITS, Surabaya.
Grinius, V. G., 2006. Physical model testing of floating
struc¬tures innovations and challenges. US/EU Baltic
Int. Sympo, Klaipeda, Lithuania.
Helvacioglu, I. H. & Incecik, A., 1988. Dynamic analysis
of coup¬led articulated tower and floating production
sys¬tems. Huston, Proc. of the 7th Int. Conf. on
Offshore Mechanics and Arctic Engineering, ASME.
Munson, B. R., 2013. Fundamentals of Fluid Mechanics.
7th ed. New York: WileyPLus.
Murtedjo, M., Djatmiko, E. B. & Sudjianto, H., 2005. The
influence of buoyancy parameters on the dynamic
behavior of articulated tower. J. Mekanikal, UTM,
Volume 19, pp. 32-47.
Srikanth, N., 2014. Barriers to ocean energy technology
adop¬tion and role of policies & institutional system to
promote in Asia, Presentation Energy Research
Institute, Nanyang Technological University,
Singapore.
The Design of Physical Model and Preparation of Experimental Study on Articulated Tower – Ocean Wave Energy Converter (AT-OWEC)
19