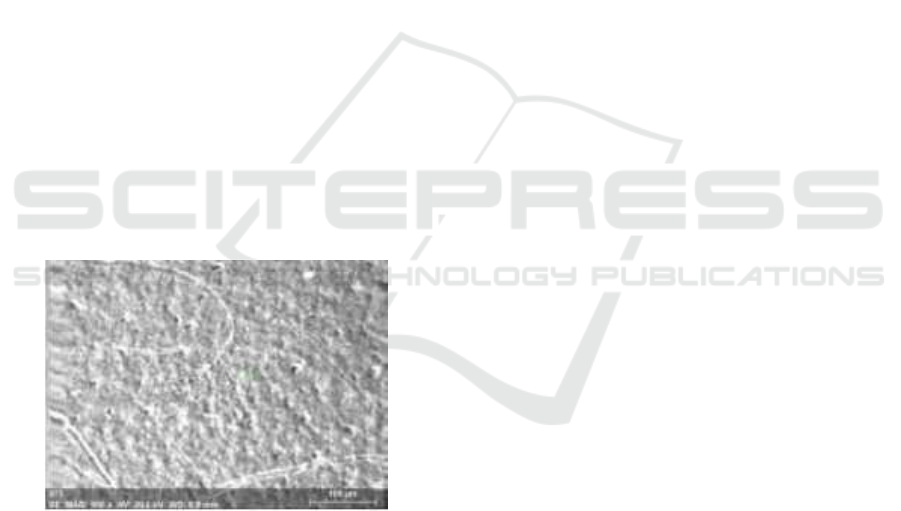
drying process of the cracked composite membrane.
This indicates that the increase in concentration does
not guarantee an increase in the value of tensile
strength.
Generally, the results show the greater filler to the
membrane and stirring time. They give higher
tensile strength results. Previous research on the
manufacture of composite membranes from chitosan
showed similar results where the tensile strength
value obtained was greater by increasing the
addition of silica, it is. due to its dense structure
which causes the distance between the molecules in
the membrane to be denser so as to have a large
tensile strength (Thermo, 2001).
3.4 Characteristic of Scanning Electron
Microscopy (SEM) Chitosan
Composite Membrane with Silica
Gel
An analysis of SEM was performed to determine
membrane pores. The test was performed at 0.6
gram silica fused chitosan membrane with 8 hours of
stirring time and composite membrane with silica
addition of 1.2 grams of silica with a stirring time of
16 hours. Because the composite membrane with 0.6
gram of silica filler has a low flux value, while 1.2
grams of silica has a high flux value.
Figure 4: Characteristic of Scanning Electron Microscopy
(SEM) Chitosan Composite Membrane with Silica Gel.
Figure 4 shows the result analysis SEM of the
membrane product with the addition of 1.2 grams of
silica and 16 hours of stirring time has a relatively
more dense morphology, which indicated that silica
was evenly mixed in the resulting membrane. The
addition of silica causes a dense chitosan membrane
to be hollow because the negative charge of the
chitosan OH-reacts with the silica so that it will
attract and form a small cavity (Siniwi, 2014). Based
on Figure 4 it can be seen that the pore size of the
membrane composites with 1.2 g silica added with
16 hours of stirring time was homogeneous. It’s due
to the addition of silica which made the membrane
structure hollowed with longer stirring time, so the
membrane becomes more homogeneous and can be
applied for filtration.
4 CONCLUSIONS
The addition of silica too much and string of time
too long causes the composite membrane to overlap
until homogeneous so that the tensile strength
increases, acetic acid is a good solvent use in
dissolving chitosan and silica, addition of the filler
on making composite membrane cause the greater
pore in membrane.
ACKNOWLEDGEMENTS
The authors gratefully acknowledge that the present
research is supported by Ministry of Research and
Technology and Higher Education Republic of
Indonesia. The support is under the research grant
BP-PTN USU of Year 2016 Contract Number
XXX/XXX.
REFERENCES
D.R. Uhlmann, and N. J. Kreidhl., 1980. “Glass Sciences
and Technology”. Academy Press.
Karlina, Yhuni. 2016. Peran Abu Vulkanik sebagai Filler
Pada Sintesis Polymer Electrolyte Membrane (PEM)
Terbuat dari Chitosan. Fakultas Matematika dan Sains.
Universitas Negeri Semarang.
Maulida, G. Melva., W, Herlinawati., 2017. Extraction
Volcanic Ash of Sinabung Mount Silica to Production
Silica Gel. J. Teknik Kimia USU.
Maulida, Harahap, Mara Bangun., Alfarodo, Anita
Manulang and Ginting, M.H.S., 2018. Utilization of
Jackfruit Seeds (Artocarpus Heterophyllus) in The
Preparing of Bioplastics by Plasticizer Ethylene Glycol
and Chitosan Filler. Journal of Engineering and
Applied Sciences. Asian Research Publishing Network.
Nakada,S and M. Yoshimoto., 2014. Earthquake Research
Institute, University of Tokyo http://www.eri.u-
tokyo.ac.jp/en/2014/02/04/eruptive-activity-of-
sinabung-volcano-in-2013-and-2014.
Neburchilov, V., J. Martin, H. Wang and J. Zhang., 2007.
Polymer Electrolyte Membranes for Direct Methanol
Fuel Cell, Journal of Power Sources.
Widhi Mahatmanti, F., 2014. Physical Characteristics of
Chitosan Based Film Modified With Silica and
ICMR 2018 - International Conference on Multidisciplinary Research
60