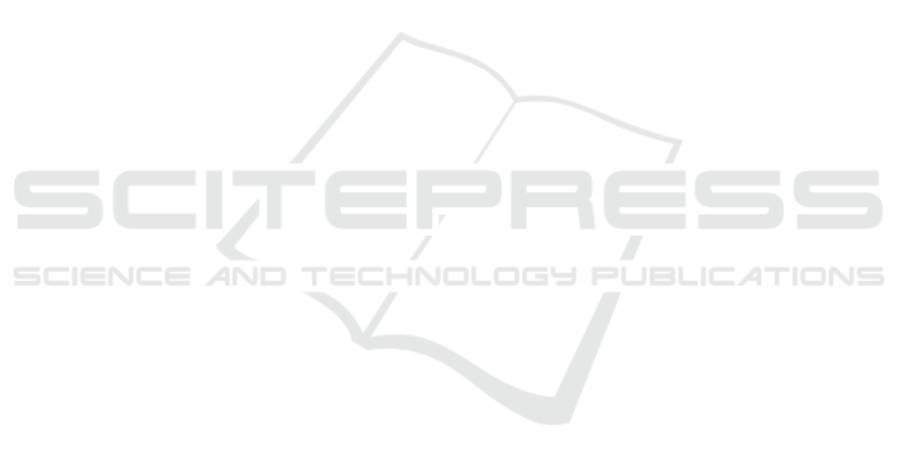
Reviews. Elsevier B.V., 161, pp. 16–129. doi:
10.1016/j.earscirev.2016.07.003.
Hossein-zadeh, M. & Razavi, M., 2013. ‘Charac-
terization of properties of Al – Al 2 O 3 nano-
composite synthesized via milling and
subsequent casting’, Journal of King Saud
University - Engineering Sciences. King Saud
University, 25(1), pp. 75–80. doi:
10.1016/j.jksues.2012.03.001.
Hubadillah, S. K., Harun, Z., Othman, M. H. D.,
Ismail, A. F. & Gani, P., 2016. ‘Effect of kaolin
particle size and loading on the characteristics of
kaolin ceramic support prepared via phase
inversion technique’, Journal of Asian Ceramic
Societies. Taibah University, 4(2), pp. 164–177.
doi: 10.1016/j.jascer.2016.02.002.
Leonel, E. C., Nassar, E. J., Ciuffi, K. J., Reis, M. J.
dos & Calefi, P. S., 2014. ‘Effect of high-energy
ball milling in the structural and textural
properties of kaolinite’, Cerâmica, 60(354), pp.
267–272. doi: 10.1590/S0366-691320140002000
16.
Matusik, J. & Bajda, T., 2013. ‘Journal of Colloid
and Interface Science Immobilization and
reduction of hexavalent chromium in the
interlayer space of positively charged kaolinites’,
Journal of Colloid And Interface Science.
Elsevier Inc., 398, pp. 74–81. doi:
10.1016/j.jcis.2013.02.015.
Matusik, J. & Matykowska, L., 2014. ‘Behaviour of
kaolinite intercalation compounds with selected
ammonium salts in aqueous chromate and
arsenate solutions’, JOURNAL OF
MOLECULAR STRUCTURE. Elsevier B.V. doi:
10.1016/j.molstruc.2014.04.063.
Mobasherpour, I., To, A. A. & Ebrahimi, M., 2013.
‘Effect of nano-size Al 2 O 3 reinforcement on
the mechanical behavior of synthesis 7075
aluminum alloy composites by mechanical
alloying’, 138. doi: 10.1016/j.matc
hemphys.2012.12.015.
Prasad, M. S., Reid, K. J. & Murray, H. H., 1991.
‘Kaolin : processing , properties and appli
cations’, 6, pp. 87–119.
Takeda, H., Hashimoto, S., Yokoyama, H., Honda,
S. & Iwamoto, Y., 2013. ‘Characterization of
zeolite in zeolite-geopolymer hybrid bulk
materials derived from kaolinitic clays’,
Materials, 6(5), pp. 1767–1778. doi:
10.3390/ma6051767.
Taylor, P., Meyersm, M. A. & Ashworth, E., 2007.
‘A model for the effect of grain size on the yield
stress of metals’, (March 2015), pp. 37–41. doi:
10.1080/01418618208236928.
Toozandehjani, M., Matori, K., Ostovan, F., Abdul
Aziz, S. & Mamat, M., 2017. ‘Effect of Milling
Time on the Microstructure, Physical and
Mechanical Properties of Al-Al2O3 Nano-
composite Synthesized by Ball Milling and
Powder Metallurgy’, Materials, 10(11), p. 1232.
doi: 10.3390/ma10111232.
Zsirka, B., Horváth, E., Makó, É., Kurdi, R. &
Kristóf, J. , 2015. ‘Preparation and charac-
terization of kaolinite nanostructures: reaction
pathways, morphology and structural order’,
Clay Minerals, 50(3), pp. 329–340. doi:
10.1180/claymin.2015.050.3.06.
Microstructure and Physical of Al2O3 2SiO4 2H2O Kaolinite Particle Analysis by Shacking Time and Powder Metallurgy
53