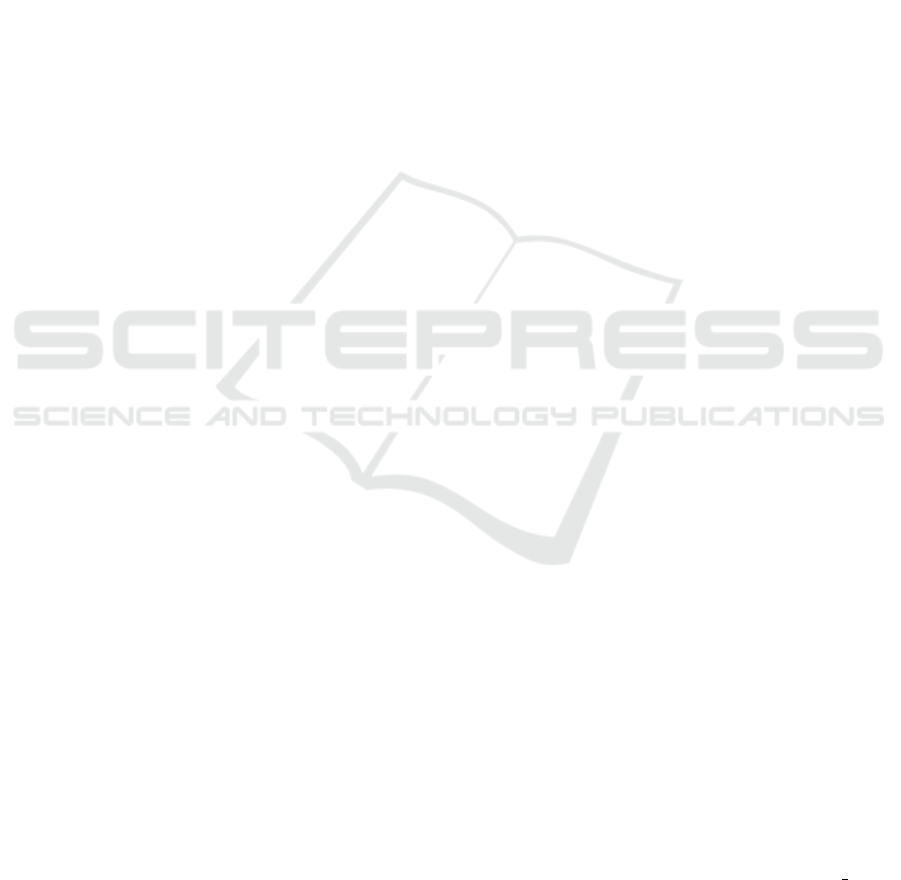
Computational Fluid Dynamic Simulation of Clearance Effect and
Velocity in Liquid Mixing System
Bayu Triwibowo
1
, Astrilia Damayanti
1
, Anwaruddin Hisyam
2
,
Dessy Ratna Puspita
1
, Dwiana Asmara
Putri
1
1
Department of Chemical Engineering,Universitas Negeri Semarang,Semarang, Indonesia
KampusUNNES Sekaran Gunungpati, Semarang 50229, Indonesia
2
Faculty of Chemical and Natural Resources Engineering, Universiti Malaysia Pahang, Lebuhraya Tun Razak,
26300, Kuantan, Pahang Darul Makmur, Malaysia
Keywords: Stirred Tank , CFD, MRF, LES, axial pressure.
Abstract: Stirred tank is one of the most important process-support tools in the industrial world, either in the food,
pharmaceutical, oil or gas industries. The stirring process in a stirred tank involves miscible liquid stirring,
gas dispersion or immiscible liquid into the liquid phase, suspension of solid particles, heat and mass
transfer and chemical reactions. This research aims to study the characteristic of the stirring process by
simulating the stir-equipped tank with water fluid that will be validated by experimentation that has been
done. The stirring process is done by simulating computational fluid dynamics (CFD) using multiple
reference frame (MRF) simulation method, modeling large eddy simulation (LES) flow turbulence and
stirring speed variable. The stages in the simulation of the stirring process include pre-process, solving and
post process. The simulation results have been validated by experiments conducted by Ivan Fort et al. The
erosion at the bottom of the tank is predicted by observing the axial pressure distribution shown by the
observation point..
1 INTRODUCTION
Stirred tanks are widely used for mixing of two
miscible fluids in the chemical, food and process
industries (Zadghaffari et al, 2008). In the various
applications, stirred tanks are required to fulfill
several needs like suspension of solid particles,
dispersion of gases into liquids, heat and mass
transfer, etc.
Agitation of solid-liquid system will caused
erosion in apparatus wall stirred tank. Erosion on
solid-liquid system have been studied by researcher
such as CFD simulation and experimental analysis
of erosion in a slurry tank test rig (Azimian and
Bart, 2013) dan Slurry Erosion in Complex Flows :
Experiment and CFD (Graham, Lester & Wu, 2009).
Azimian et al (2013) have reported that hydro-
erosion occurs in practice in two ways, one is the
erosion by cavitations of liquid and on the other
hand is the erosion by solid particles entrained in
liquid flow known as slurry erosion.
Erosion rate is generally considered as the main
function of influence particle rate, velocity and
impact angle, so that the distribution of erosion rate
depend on those factor. If the erosion is not equally
distributed may cause tools damages. The uniform
distribution will be achieved if the characteristic of
erosion rate for geometrical agitated tank
modification has known as a basic of engineering
technology (Graham et al, 2009). The rate of erosion
distribution can be determined from erosion model,
which can be a very useful tool for prediction..
Computational modeling has always been
presented as an option for the hydrodynamic
analysis of such systems as it is far inexpensive and
enables the study of detailed description of
multiphase flow. CFD modelling, however, can only
be applied after proper validation (Wadnerkar et al.,
430
Triwibowo, B., Damayanti, A., Hisyam, A., Puspita, D. and Putri, D.
Computational Fluid Dynamic Simulation of Clearance Effect and Velocity in Liquid Mixing System.
DOI: 10.5220/0009012604300434
In Proceedings of the 7th Engineering Inter national Conference on Education, Concept and Application on Green Technology (EIC 2018), pages 430-434
ISBN: 978-989-758-411-4
Copyright
c
2020 by SCITEPRESS – Science and Technology Publications, Lda. All rights reserved