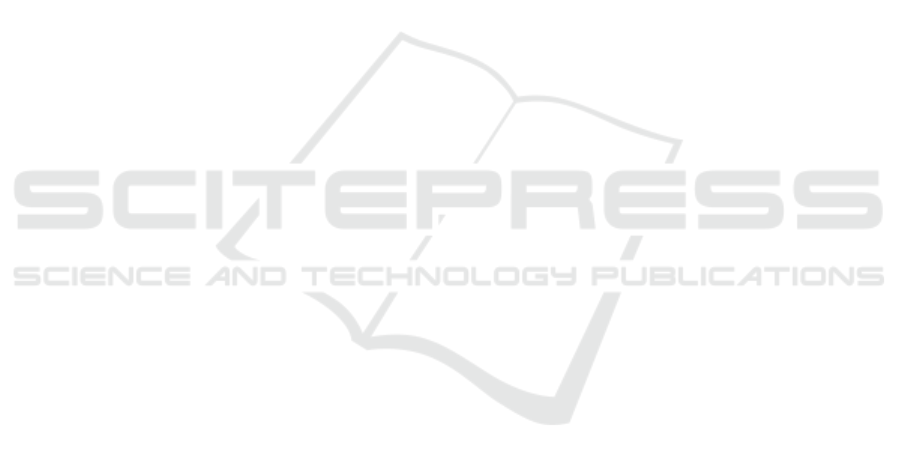
Note that index i is ommited in the above
equation, since in this case
is only one individu or
precisely one party, i.e. the representative of external
auditor.
The Likert-like scale of our research, is between
- 1 to +1 to represent the conformance status of ISO
9001 QMS usage. The reason to assign such a range
is to allow negative (for NC) and positive (for OFI
and PO) values. Similar reason is also used by Başak
Manders (Manders, de Vries and Blind, 2016, p.
147) allowing respondents to report both negative
and positive changes in order to measure the
performance of QMS implementation that ranges
between -2 to +2 (e.g. a scale from -2 to 2; -2=Large
decrease; -1=Small decrease; 0=No change; 1=Small
increase; 2=Large increase). Other usage of Likert-
like scale is proposed by R.A. Smith, A. Bester and
M. Moll (2014) that employ different way to assign
the non-conformity of the QMS in order to quantify
QMS performance measure. According to them non-
conformity grade consists of rating value and safety
weight, where rating value is grouped into three
levels, i.e. Low = 0.3; Medium = 0.8; and High =1
and safety weight as Management = 0.3; Enabling =
0.6; and Core = 1.
On the contrary, Nikolay (2016) did not apply
Likert-like scale but rather the number of non-
conformity findings. Compare to our method, there
are at least two differences. Firstly, our method
regards three types of audit findings, i.e. NC, OFI
and PO whereas Nikolay uses NC only. Secondly,
Nikolay traces the number of resolved NCs with
allocated cost for implementing corrective actions.
Future research development may adopt
Nikolay’s method by taking into account the number
of NCs of the past period that have been resolved by
corrective actions. This method concern with all
corrective actions to address identified non-
conformities of the past period are carried out before
the start of the planning period.
REFERENCES
BSI-CEN (2011) BSI Standards Publication: Guidelines
for auditing management systems (ISO
19011:2011). Brussels.
Charlet, L. (2017) The ISO Survey, International
Organization for Standardization. Available at:
https://www.iso.org/the-iso-survey.html
(Accessed: 1 November 2018).
Cheng, Y., Lyu, J. and Lin, Y. (2004) ‘Education
Improvement through ISO 9000 Implementation :
Experiences in Taiwan’, International Journal of
Engineering Education, 20(1), pp. 91–95.
Chyung, Y. et al. (2017) ‘Evidence-Based Survey Design:
The Use of a Midpoint on the Likert Scale’,
Performance Improvement, 56(10), pp. 15–23.
doi: doi:10.1002/pfi.21727.
Edirisooriya, G. (1997) ‘A Different Approach to Attitude
Scale Construction’, in Annual Meeting of the
American Educational Research Association.
Chicago, IL: American Educational Research
Association, pp. 1–21. Available at:
https://files.eric.ed.gov/fulltext/ED410244.pdf.
EU (2015) ‘Toolbox: Tool #42: Identifying the evaluation
criteria and questions’, in Toolbox for Better
Regulation in SWD (2015) 111. European
Commission, pp. 271–277. doi:
10.1163/1571809042388581.
Fons, L. A. S. (2011) ‘Measuring economic effects of
quality management systems’, The TQM Journal,
23(4), pp. 458–474. doi:
10.1108/17542731111139527.
Jamieson, S. (2004) ‘Likert scales : how to (ab)use them’,
Medical Education, 38(12), pp. 1217–1218. doi:
10.1111/j.1365-2929.2004.02012.x.
Kenny (2011) ‘Performance measures in focus’, National
Accountant, (April-May), pp. 24–26.
Kenny, G. and Bourne, M. (2015) ‘Performance
Measurement’, in Cooper, C. L. (ed.) Wiley
Encyclopedia of Management. John Wiley &
Sons. doi: 10.1002/9781118785317.weom120139.
Manders, B., de Vries, H. J. and Blind, K. (2016)
‘Technovation ISO 9001 and product innovation :
A literature review and research framework’,
Technovation. Elsevier, 48(Feb 1), pp. 41–55. doi:
10.1016/j.technovation.2015.11.004.
Neely, A. (2005) ‘The evolution of performance
measurement research: Developments in the last
decade and a research agenda for the next’,
International Journal of Operations & Production
Management, 25(12), pp. 1264–1277. doi:
10.1108/01443570510633648.
Neely, A., Gregory, M. and Platts, K. (1995)
‘Performance measurement system design: A
literature review and research agenda’,
International Journal of Operations & Production
Management, 15(4), pp. 80–116. Available at:
https://doi.org/10.1108/01443579510083622%0A
Downloaded.
Neely, A., Gregory, M. and Platts, K. (2005)
‘Performance measurement system design: A
literature review and research agenda’,
Quantifying the ISO 9001:2008 Quality Management System Audit Reports to Measure the Implementation Performance
875