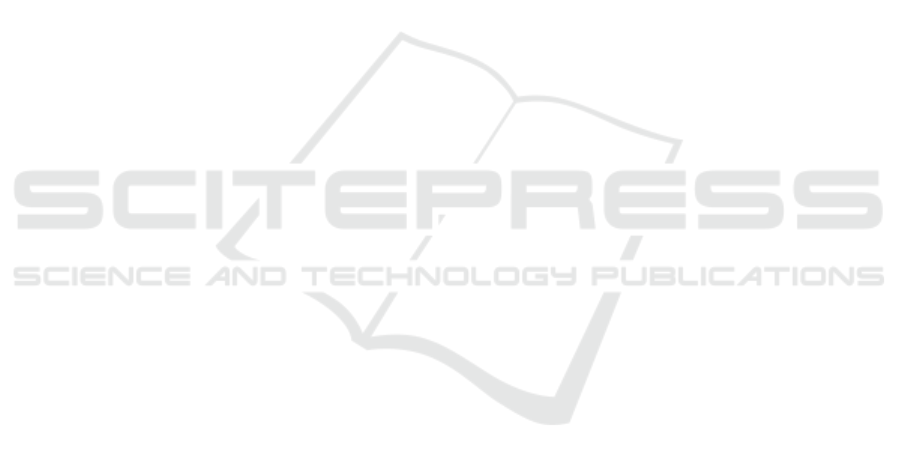
adjusted design parameters. All generated design
variants are consistent with the given boundary
conditions. A systematic evaluation and selection
process can be performed afterwards. Classic
approaches (without a digital re-execution) create
only one or a few design variants while this approach
explores the full solution space. It reveals full variety
of possible and consistent designs. This article
showed the process with the example of an
automotive dashboard and selected engineering tasks
(requirements formalization, cable wiring and
verification and validation). We see the approach
presented as a starting point for further digital
engineering efforts across all engineering domains.
The approach can be extended incrementally to
achieve a more digital product design process with
tremendous time and cost reduction while improving
overall product quality.
ACKNOWLEDGEMENTS
We would like to thank our collaborators: Dominik
Schopper and Claudia Tonhäuser at the University of
Stuttgart, Jens Schmidt, Roland Weil, Peter Arnold,
Marius Riestenpatt, Marc Eheim and Stefan Hess at
IILS mbH and Jan Martin, Jonathan Schmidt, Hanna
Dettki and Marco Piechotta at Daimler AG.
REFERENCES
Alber, R., Rudolph, S.”43 - A Generic Approach for
Engineering Design Grammars.” AAAI Spring Symposium
Computational Synthesis, 2003.
Artale, A., Franconi, E.”A Temporal Description Logic for
Reasoning about Actions and Pans.” Journal of Artificial
Intelligence Research 9, 1998.
Böhm, B.”A Spiral Model of Software Development and
Enhancement.” Computer 21, no. 5, 1988.
Dwyer, M., Avrunin G., Corbett ,J. ”Property Specification
Patterns for Finite-State Verification.” In Proceedings
of the Second Workshop on Formal Methods in
Software Practice, ACM, 1998.
IILS mbH,”Total Engineering Automation Vision and
Realization with Graph-Based Design Languages and
the Design Cockpit 43.” http://iils.de (May, 2018).
ITEA3, IDEALISEM. https://www.idealism.eu/
technologies (May, 2018).
ISO/IEC/IEEE 29148: 2011(E): ISO/IEC/IEEE Int.
Standard, Systems & Software Engineering Life Cycle
Processes Requirements Engineering. IEEE, 2011
Glinz, M.. ”On Non-Functional Requirements.” In
Requirements Engineering Conference, 2007
Gross, J., Rudolph, S. ”Generating Simulation Models from
UML-A FireSat Example.” Symposium on Theory of
Modeling & Simulation-DEVS Integrative M&S, 2012.
Gips, J., Stiny. G.”Production Systems and Grammars: A
Uniform Characterization.” Environment and Planning
B: Planning and Design 7, no. 4, 1980.
Kamp, H.”Tense Logic and the Theory of Linear Order.”,
1968.
Villa, T., Kam, T., Brayton, R., Sangiovanni-Vincentelli, A.
”Synthesis of Finite State Machines: Logic
Optimization.” Springer Science, 2012.
Kröplin, B, Rudolph, S. ”Entwurfsgrammatiken - Ein
Paradigmenwechsel.” Der Prüfingenieur 26, 2005.
Maalej, W., Thurimella, A.”Managing Requirements
Knowledge.” Springer, 2013.
Mavin, A., Wilkinson, P., Harwood, A., Novak, M.”Easy
Approach to Requirements Syntax (EARS).” In
Requirements Engineering Conference IEEE, 2009.
Pahl, G., Beitz, W.”Engineering Design:A Systematic
Approach.” Springer Science & Business Media, 2013.
Prior, A.”Past, Present and Future.” Oxford: Clarendon
Press, 1967.
Prior, A.”Time and Modality.” John Locke Lecture, 2003.
Prusinkiewicz, P., Lindenmayer, A.”The Algorithmic
Beauty of Plants.” Springer Science, 2012.
Riestenpatt, M., Rudolph, S.”Automated Fault-Tree
Analysis of Complex Systems with Graph-Based
Design Languages.” SECESA, 2014.
Rudolph, S.”A Semantic Validation Scheme for Graph-
Based Engineering Design Grammars.” In Design
Computing and Cognition06, Springer, 2006
Rudolph, S., Beichter, J., Eheim, M., Hess, S., Motzer, M.,
Weil R.,”On Multi-Disciplinary Architectural
Synthesis and Analysis of Complex Systems with
Graph-Based Design Languages.” DGLR, 2013.
Schäfer, J., Rudolph, S.”Satellite Design by Design
Grammars.” Aerospace Science & Technology 9, 2005.
Schmidt, J., Rudolph, S.”Graph-Based Design Languages:
A Lingua Franca for Product Design Including Abstract
Geometry.” IEEE, 2016.
Sophist GmbH,”MASTeR, Schablonen für alle Fälle”
2016.
Stiny, G.”Introduction to Shape and Shape Grammars.”
Environment & planning B: planning and design, 1980.
Vogel, S., Danckert B., Rudolph, S. ”Knowledge-Based
Design of SCR Systems Using Graph-Based Design
Languages.” MTZ worldwide 73, no. 9, 2012.
Walter, B., Hammes, J., Piechotta, M., Rudolph, S.”A
Formalization Method to Process Structured Natural
Language to Logic Expressions to Detect Redundant
Specification and Test Statements.” In Requirements
Engineering Conference, IEEE, 2017.
Walter, B., Schilling M., Piechotta, M., Rudolph, S.
”Improving Test Execution Efficiency through
Clustering and Reordering of Independent Test Steps.”
In Software Testing, Verification & Validation, 2018.
Walter, B., Martin, J., Rudolph, S.”A Method to
Automatically Derive the System State Machine from
Structured Natural Language Requirements through
Requirements Formalization.” INCOSE, 2018.
MODELSWARD 2019 - 7th International Conference on Model-Driven Engineering and Software Development
208