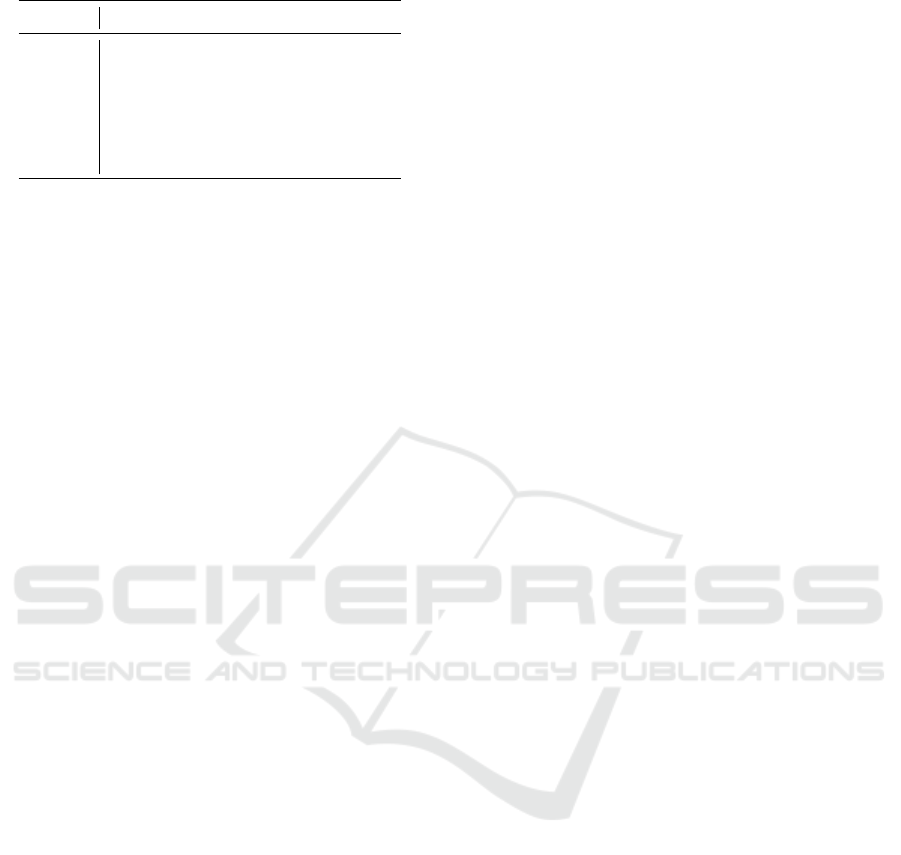
Table 4: Total makespan with varying n, m.
n m CP MILP-IMP MILP-DIS
10 2 46419 46451 46425
10 4 26028 26028 26028
20 2 94673 95736 97456
20 4 49206 49284 49394
30 2 133389 136744 140814
30 4 69938 70250 71033
method). The table reveals that CP outperforms all
the other approaches, which is not surprising since
IBM CP Optimizer is primarily designed to find good
solutions. With the exception of the instances with
n = 10, m = 2, MILP-IMP has smaller or the same
total makespan as MILP-DIS.
5 CONCLUSION
Managing the production is becoming increasingly
complex without computer-aided systems. On the
other hand, traditional scheduling constraints and ob-
jectives are not enough to design realistic produc-
tion schedules. In this work, we explored a schedul-
ing problem with a practical production constraint of
satisfying the contracted energy consumption limits.
This problem emerges in energy-demanding produc-
tion processes, such as glass tempering or steel hard-
ening, in which a material is heated in furnaces to
high temperature. The heating in the furnaces has to
be planned carefully; otherwise, the resulting energy
spikes lead to a violation of the energy limits.
We propose two exact algorithms for the studied
scheduling problem with dedicated machines: (i) a
Constraint Programming model and (ii) a Mixed In-
teger Linear Programming based iterative algorithm.
The iterative algorithm exploits the fact that the start
times do not need to be modeled explicitly, which al-
lows us to efficiently solve instances having a higher
number of shorter jobs. To compare the algorithms
with the approaches from literature, we adapted an ex-
isting Mixed Integer Linear Programming model for
a similar problem (Ha
¨
ıt and Artigues, 2011; Ha
¨
ıt and
Artigues, 2011). To summarize the experimental re-
sults on a dataset consisting of instances with 10 to
30 jobs, our best method proves the optimality for
54.9% instances, whereas the Mixed Integer Linear
Programming model inspired by the existing litera-
ture proves the optimality for 45.3% instances.
In the future, our aim is to extend our iterative al-
gorithm to the job shop scheduling problem with en-
ergy consumption limit, where the research challenge
is handling of the precedences between the operations
of the same job.
ACKNOWLEDGEMENTS
The work in this paper was supported by the Technol-
ogy Agency of the Czech Republic under the Centre
for Applied Cybernetics TE01020197.
REFERENCES
Bruzzone, A., Anghinolfi, D., Paolucci, M., and Tonelli,
F. (2012). Energy-aware scheduling for improving
manufacturing process sustainability: A mathematical
model for flexible flow shops. CIRP Annals - Manu-
facturing Technology, 61(1):459–462.
Fang, K., Uhan, N. A., Zhao, F., and Sutherland, J. W.
(2013). Flow shop scheduling with peak power con-
sumption constraints. Annals of Operations Research,
206(1):115–145.
Gajic, D., Hadera, H., Onofri, L., Harjunkoski, I., and Gen-
naro, S. D. (2017). Implementation of an integrated
production and electricity optimization system in melt
shop. Journal of Cleaner Production, 155:39 – 46.
Sustainable Development of Energy, Water and Envi-
ronmental Systems.
Gurobi (2018). Constraints. http://www.gurobi.
com/documentation/8.0/refman/constraints.html. Ac-
cessed September 18, 2018.
Hadera, H., Harjunkoski, I., Sand, G., Grossmann, I. E.,
and Engell, S. (2015). Optimization of steel pro-
duction scheduling with complex time-sensitive elec-
tricity cost. Computers & Chemical Engineering,
76:117–136.
Ha
¨
ıt, A. and Artigues, C. (2011). A hybrid CP/MILP
method for scheduling with energy costs. European
Journal of Industrial Engineering, 5(4):471–489.
Ha
¨
ıt, A. and Artigues, C. (2011). On electrical load tracking
scheduling for a steel plant. Computers & Chemical
Engineering, 35(12):3044–3047.
Laborie, P., Rogerie, J., Shaw, P., and Vil
´
ım, P. (2018).
IBM ILOG CP optimizer for scheduling. Constraints,
23(2):210–250.
Masmoudi, O., Yalaoui, A., Ouazene, Y., and Chehade, H.
(2017). Lot-sizing in a multi-stage flow line produc-
tion system with energy consideration. International
Journal of Production Research, 55(6):1640–1663.
Merkert, L., Harjunkoski, I., Isaksson, A., S
¨
aynevirta, S.,
Saarela, A., and Sand, G. (2015). Scheduling and en-
ergy – industrial challenges and opportunities. Com-
puters & Chemical Engineering, 72(0):183 – 198.
M
´
odos, I.,
ˇ
S
˚
ucha, P., and Hanz
´
alek, Z. (2017). Algo-
rithms for robust production scheduling with energy
consumption limits. Computers & Industrial Engi-
neering, 112:391 – 408.
Nolde, K. and Morari, M. (2010). Electrical load tracking
scheduling of a steel plant. Computers & Chemical
Engineering, 34(11):1899–1903.
Rapine, C., Goisque, G., and Akbalik, A. (2018). Energy-
aware lot sizing problem: Complexity analysis and ex-
ICORES 2019 - 8th International Conference on Operations Research and Enterprise Systems
60